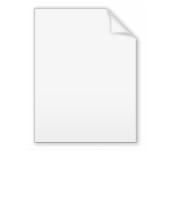
AISI steel grades
Encyclopedia
The Society of Automotive Engineers (SAE) designates SAE steel grades. These are four digit numbers which represent chemical composition standards for steel specifications. The American Iron and Steel Institute
(AISI) originally started a very similar system. Over time they used the same numbers to refer to the same alloy, but the AISI system used a letter prefix to denote the steelmaking
process. The prefix "C" denoted open-hearth furnace, electric arc furnace
or basic oxygen furnace, while "E" denotes electric arc furnace steel.
Prior to 1995 the AISI was also involved, and the standard was designated the AISI/SAE steel grades. The AISI stopped being involved because it never wrote any of the specifications.
An "H" suffix can be added to any designation to denote hardenability is a major requirement. The chemical requirements are loosened but hardness values defined for various distances on a Jominy test.
American Iron and Steel Institute
The American Iron and Steel Institute is an association of North American steel producers. Its predecessor organizations date back to 1855 making it one of the oldest trade associations in the United States. AISI assumed its present form in 1908, with Elbert H...
(AISI) originally started a very similar system. Over time they used the same numbers to refer to the same alloy, but the AISI system used a letter prefix to denote the steelmaking
Steelmaking
Steelmaking is the second step in producing steel from iron ore. In this stage, impurities such as sulfur, phosphorus, and excess carbon are removed from the raw iron, and alloying elements such as manganese, nickel, chromium and vanadium are added to produce the exact steel required.-Older...
process. The prefix "C" denoted open-hearth furnace, electric arc furnace
Electric arc furnace
An electric arc furnace is a furnace that heats charged material by means of an electric arc.Arc furnaces range in size from small units of approximately one ton capacity up to about 400 ton units used for secondary steelmaking...
or basic oxygen furnace, while "E" denotes electric arc furnace steel.
Prior to 1995 the AISI was also involved, and the standard was designated the AISI/SAE steel grades. The AISI stopped being involved because it never wrote any of the specifications.
Carbon and alloy steel
Carbon steels and alloy steels are designated by a four digit number, where the first digit indicates the main alloying element(s), the second digit indicates the secondary alloying element(s), and the last two digits indicate the amount of carbon, in hundredths of a percent by weight. For example, a 1060 steel is a plain-carbon steel containing 0.60 wt% C.An "H" suffix can be added to any designation to denote hardenability is a major requirement. The chemical requirements are loosened but hardness values defined for various distances on a Jominy test.
SAE designation | Type |
---|---|
1xxx | Carbon steels |
2xxx | Nickel steels |
3xxx | Nickel-chromium steels |
4xxx | Molybdenum steels |
5xxx | Chromium steels |
6xxx | Chromium-vanadium steels |
7xxx | Tungsten steels |
8xxx | Nickel-chromium-vanadium steels |
9xxx | Silicon-manganese steels |
SAE designation | Type |
---|---|
Carbon steels | |
10xx | Plain carbon (Mn 1.00% max) |
11xx | Resulfurized |
12xx | Resulfurized and rephosphorized |
15xx | Plain carbon (Mn 1.00% to 1.65%) |
Manganese steels | |
13xx | Mn 1.75% |
Nickel steels | |
23xx | Ni 3.50% |
25xx | Ni 5.00% |
Nickel-chromium steels | |
31xx | Ni 1.25%, Cr 0.65% or 0.80% |
32xx | Ni 1.25%, Cr 1.07% |
33xx | Ni 3.50%, Cr 1.50% or 1.57% |
34xx | Ni 3.00%, Cr 0.77% |
Molybdenum steels | |
40xx | Mo 0.20% or 0.25% or 0.25% Mo & 0.042 S |
44xx | Mo 0.40% or 0.52% |
Chromium-molybdenum (Chromoly) steels | |
41xx 41xx steel 41xx steel is a family of SAE steel grades, as specified by the Society of Automotive Engineers . Alloying elements include chromium and molybdenum, and as a result these materials are often referred to as chromoly steel or CRMO... |
Cr 0.50% or 0.80% or 0.95%, Mo 0.12% or 0.20% or 0.25% or 0.30% |
Nickel-chromium-molybdenum steels | |
43xx | Ni 1.82%, Cr 0.50% to 0.80%, Mo 0.25% |
43BVxx | Ni 1.82%, Cr 0.50%, Mo 0.12% or 0.35%, V 0.03% min |
47xx | Ni 1.05%, Cr 0.45%, Mo 0.20% or 0.35% |
81xx | Ni 0.30%, Cr 0.40%, Mo 0.12% |
81Bxx | Ni 0.30%, Cr 0.45%, Mo 0.12% |
86xx | Ni 0.55%, Cr 0.50%, Mo 0.20% |
87xx | Ni 0.55%, Cr 0.50%, Mo 0.25% |
88xx | Ni 0.55%, Cr 0.50%, Mo 0.35% |
93xx | Ni 3.25%, Cr 1.20%, Mo 0.12% |
94xx | Ni 0.45%, Cr 0.40%, Mo 0.12% |
97xx | Ni 0.55%, Cr 0.20%, Mo 0.20% |
98xx | Ni 1.00%, Cr 0.80%, Mo 0.25% |
Nickel-molybdenum steels | |
46xx | Ni 0.85% or 1.82%, Mo 0.20% or 0.25% |
48xx | Ni 3.50%, Mo 0.25% |
Chromium steels | |
50xx | Cr 0.27% or 0.40% or 0.50% or 0.65% |
50xxx | Cr 0.50%, C 1.00% min |
50Bxx | Cr 0.28% or 0.50% |
51xx | Cr 0.80% or 0.87% or 0.92% or 1.00% or 1.05% |
51xxx | Cr 1.02%, C 1.00% min |
51Bxx | Cr 0.80% |
52xxx | Cr 1.45%, C 1.00% min |
Chromium-vanadium steels | |
61xx | Cr 0.60% or 0.80% or 0.95%, V 0.10% or 0.15% min |
Tungsten-chromium steels | |
72xx | W 1.75%, Cr 0.75% |
Silicon-manganese steels | |
92xx | Si 1.40% or 2.00%, Mn 0.65% or 0.82% or 0.85%, Cr 0.00% or 0.65% |
High-strength low-alloy steels | |
9xx | Various SAE grades |
xxBxx | Boron steels |
xxLxx | Leaded steels |
Stainless steel
- 100 Series—austenitic chromium-nickel-manganese alloys
- Type 101—austenitic that is hardenable through cold working for furniture
- Type 102—austenitic general purpose stainless steel working for furniture
- 200 Series—austenitic chromium-nickel-manganese alloys
- Type 201—austenitic that is hardenable through cold working
- Type 202—austenitic general purpose stainless steel
- 300 Series—austenitic chromium-nickel alloys
- Type 301—highly ductile, for formed products. Also hardens rapidly during mechanical working. Good weldability. Better wear resistance and fatigue strength than 304.
- Type 302—same corrosion resistance as 304, with slightly higher strength due to additional carbon.
- Type 303—free machining version of 304 via addition of sulfurSulfurSulfur or sulphur is the chemical element with atomic number 16. In the periodic table it is represented by the symbol S. It is an abundant, multivalent non-metal. Under normal conditions, sulfur atoms form cyclic octatomic molecules with chemical formula S8. Elemental sulfur is a bright yellow...
and phosphorusPhosphorusPhosphorus is the chemical element that has the symbol P and atomic number 15. A multivalent nonmetal of the nitrogen group, phosphorus as a mineral is almost always present in its maximally oxidized state, as inorganic phosphate rocks...
. Also referred to as "A1" in accordance with ISO 3506. - Type 304—the most common grade; the classic 18/8 stainless steel. Outside of the US it is commonly known as "A2", in accordance with ISO 3506 (not to be confused with A2 tool steel).
- Type 304L—same as the 304 grade but contains less carbon to increase weldability. Is slightly weaker than 304.
- Type 304LN—same as 304L, but also nitrogen is added to obtain a much higher yield and tensile strength than 304L.
- Type 308—used as the filler metal when welding 304.
- Type 309—better temperature resistance than 304, also sometimes used as filler metal when welding dissimilar steels, along with inconelInconelInconel is a registered trademark of Special Metals Corporation that refers to a family of austenitic nickel-chromium-based superalloys. Inconel alloys are typically used in high temperature applications. It is often referred to in English as "Inco"...
. - Type 316—the second most common grade (after 304); for food and surgical stainless steelSurgical stainless steelSurgical stainless steel is a specific type of stainless steel, used in medical applications, made out of several components: chromium, nickel and molybdenum....
uses; alloy addition of molybdenum prevents specific forms of corrosion. It is also known as marine grade stainless steel due to its increased resistance to chloride corrosion compared to type 304. 316 is often used for building nuclear reprocessingNuclear reprocessingNuclear reprocessing technology was developed to chemically separate and recover fissionable plutonium from irradiated nuclear fuel. Reprocessing serves multiple purposes, whose relative importance has changed over time. Originally reprocessing was used solely to extract plutonium for producing...
plants. 316L is an extra low carbon grade of 316, generally used in stainless steel watches and marine applications, as well exclusively in the fabrication of reactor pressure vessels for boiling water reactorBoiling water reactorThe boiling water reactor is a type of light water nuclear reactor used for the generation of electrical power. It is the second most common type of electricity-generating nuclear reactor after the pressurized water reactor , also a type of light water nuclear reactor...
s, due to its high resistance to corrosion. Also referred to as "A4" in accordance with ISO 3506. 316Ti includes titanium for heat resistance, therefore it is used in flexible chimney liners. - Type 321—similar to 304 but lower risk of weld decay due to addition of titanium. See also 347 with addition of niobium for desensitization during welding.
- 400 Series—ferritic and martensitic chromium alloys
- Type 405—ferritic for welding applications
- Type 408—heat-resistant; poor corrosion resistance; 11% chromium, 8% nickel.
- Type 409—cheapest type; used for automobileAutomobileAn automobile, autocar, motor car or car is a wheeled motor vehicle used for transporting passengers, which also carries its own engine or motor...
exhausts; ferritic (iron/chromium only). - Type 410—martensitic (high-strength iron/chromium). Wear-resistant, but less corrosion-resistant.
- Type 416—easy to machine due to additional sulfur
- Type 420—Cutlery Grade martensitic; similar to the Brearley's original rustless steel. Excellent polishability.
- Type 430—decorative, e.g., for automotive trim; ferritic. Good formability, but with reduced temperature and corrosion resistance.
- Type 439—ferritic grade, a higher grade version of 409 used for catalytic converter exhaust sections. Increased chromium for improved high temperature corrosion/oxidation resistance.
- Type 440—a higher grade of cutlery steel, with more carbon, allowing for much better edge retention when properly heat-treated. It can be hardened to approximately RockwellRockwell scaleThe Rockwell scale is a hardness scale based on the indentation hardness of a material. The Rockwell test determines the hardness by measuring the depth of penetration of an indenter under a large load compared to the penetration made by a preload. There are different scales, denoted by a single...
58 hardness, making it one of the hardest stainless steels. Due to its toughness and relatively low cost, most display-only and replica swords or knives are made of 440 stainless. Available in four grades: 440A, 440B, 440C, and the uncommon 440F (free machinable). 440A, having the least amount of carbon in it, is the most stain-resistant; 440C, having the most, is the strongest and is usually considered more desirable in knifemaking than 440A, except for diving or other salt-water applications. - Type 446—For elevated temperature service
- 500 Series—heat-resisting chromium alloys
- 600 Series—martensitic precipitation hardening alloys
- 601 through 604: Martensitic low-alloy steels.
- 610 through 613: Martensitic secondary hardening steels.
- 614 through 619: Martensitic chromium steels.
- 630 through 635: Semiaustenitic and martensitic precipitation-hardening stainless steels.
- Type 630 is most common PH stainless, better known as 17-4; 17% chromium, 4% nickel.
- 650 through 653: Austenitic steels strengthened by hot/cold work.
- 660 through 665: Austenitic superalloys; all grades except alloy 661 are strengthened by second-phase precipitation.
- Type 2205—the most widely used duplex (ferritic/austenitic) stainless steel grade. It has both excellent corrosion resistance and high strength.
- Type 2304—lean duplex stainless steel. Similar to 2205 for strength but with lower pitting corrosion resistance due to low Molybdenum.
SAE designation | UNS designation | % Cr | % Ni | % C | % Mn | % Si | % P | % S | % N | Other |
---|---|---|---|---|---|---|---|---|---|---|
Austenitic | ||||||||||
201 | S20100 | 16–18 | 3.5–5.5 | 0.15 | 5.5–7.5 | 0.75 | 0.06 | 0.03 | 0.25 | - |
202 | S20200 | 17–19 | 4–6 | 0.15 | 7.5–10.0 | 0.75 | 0.06 | 0.03 | 0.25 | - |
205 | S20500 | 16.5–18 | 1–1.75 | 0.12–0.25 | 14–15.5 | 0.75 | 0.06 | 0.03 | 0.32–0.40 | - |
254 | S31254 | 20 | 18 | 0.02 max | - | - | - | - | 0.20 | 6 Mo; 0.75 Cu; "Super austenitic"; All values nominal |
301 | S30100 | 16–18 | 6–8 | 0.15 | 2 | 0.75 | 0.045 | 0.03 | - | - |
302 | S30200 | 17–19 | 8–10 | 0.15 | 2 | 0.75 | 0.045 | 0.03 | 0.1 | - |
302B | S30215 | 17–19 | 8–10 | 0.15 | 2 | 2.0–3.0 | 0.045 | 0.03 | - | - |
303 | S30300 | 17–19 | 8–10 | 0.15 | 2 | 1 | 0.2 | 0.15 min | - | Mo 0.60 (optional) |
303Se | S30323 | 17–19 | 8–10 | 0.15 | 2 | 1 | 0.2 | 0.06 | - | 0.15 Se min |
304 | S30400 | 18–20 | 8–10.50 | 0.08 | 2 | 0.75 | 0.045 | 0.03 | 0.1 | - |
304L | S30403 | 18–20 | 8–12 | 0.03 | 2 | 0.75 | 0.045 | 0.03 | 0.1 | - |
304Cu | S30430 | 17–19 | 8–10 | 0.08 | 2 | 0.75 | 0.045 | 0.03 | - | 3–4 Cu |
304N | S30451 | 18–20 | 8–10.50 | 0.08 | 2 | 0.75 | 0.045 | 0.03 | 0.10–0.16 | - |
305 | S30500 | 17–19 | 10.50–13 | 0.12 | 2 | 0.75 | 0.045 | 0.03 | - | - |
308 | S30800 | 19–21 | 10–12 | 0.08 | 2 | 1 | 0.045 | 0.03 | - | - |
309 | S30900 | 22–24 | 12–15 | 0.2 | 2 | 1 | 0.045 | 0.03 | - | - |
309S | S30908 | 22–24 | 12–15 | 0.08 | 2 | 1 | 0.045 | 0.03 | - | - |
310 | S31000 | 24–26 | 19–22 | 0.25 | 2 | 1.5 | 0.045 | 0.03 | - | - |
310S | S31008 | 24–26 | 19–22 | 0.08 | 2 | 1.5 | 0.045 | 0.03 | - | - |
314 | S31400 | 23–26 | 19–22 | 0.25 | 2 | 1.5–3.0 | 0.045 | 0.03 | - | - |
316 | S31600 | 16–18 | 10–14 | 0.08 | 2 | 0.75 | 0.045 | 0.03 | 0.10 | 2.0–3.0 Mo |
316L | S31603 | 16–18 | 10–14 | 0.03 | 2 | 0.75 | 0.045 | 0.03 | 0.10 | 2.0–3.0 Mo |
316F | S31620 | 16–18 | 10–14 | 0.08 | 2 | 1 | 0.2 | 0.10 min | - | 1.75–2.50 Mo |
316N | S31651 | 16–18 | 10–14 | 0.08 | 2 | 0.75 | 0.045 | 0.03 | 0.10–0.16 | 2.0–3.0 Mo |
317 | S31700 | 18–20 | 11–15 | 0.08 | 2 | 0.75 | 0.045 | 0.03 | 0.10 max | 3.0–4.0 Mo |
317L | S31703 | 18–20 | 11–15 | 0.03 | 2 | 0.75 | 0.045 | 0.03 | 0.10 max | 3.0–4.0 Mo |
321 | S32100 | 17–19 | 9–12 | 0.08 | 2 | 0.75 | 0.045 | 0.03 | 0.10 max | Ti 5(C+N) min, 0.70 max |
329 | S32900 | 23–28 | 2.5–5 | 0.08 | 2 | 0.75 | 0.04 | 0.03 | - | 1–2 Mo |
330 | N08330 | 17–20 | 34–37 | 0.08 | 2 | 0.75–1.50 | 0.04 | 0.03 | - | - |
347 | S34700 | 17–19 | 9–13 | 0.08 | 2 | 0.75 | 0.045 | 0.030 | - | Nb + Ta, 10 x C min, 1 max |
348 | S34800 | 17–19 | 9–13 | 0.08 | 2 | 0.75 | 0.045 | 0.030 | - | Nb + Ta, 10 x C min, 1 max, but 0.10 Ta max; 0.20 Ca |
384 | S38400 | 15–17 | 17–19 | 0.08 | 2 | 1 | 0.045 | 0.03 | - | - |
SAE designation | UNS designation | % Cr | % Ni | % C | % Mn | % Si | % P | % S | % N | Other |
Ferritic | ||||||||||
405 | S40500 | 11.5–14.5 | - | 0.08 | 1 | 1 | 0.04 | 0.03 | - | 0.1–0.3 Al, 0.60 max |
409 | S40900 | 10.5–11.75 | 0.05 | 0.08 | 1 | 1 | 0.045 | 0.03 | - | Ti 6 x C, but 0.75 max |
429 | S42900 | 14–16 | 0.75 | 0.12 | 1 | 1 | 0.04 | 0.03 | - | - |
430 | S43000 | 16–18 | 0.75 | 0.12 | 1 | 1 | 0.04 | 0.03 | - | - |
430F | S43020 | 16–18 | - | 0.12 | 1.25 | 1 | 0.06 | 0.15 min | - | 0.60 Mo (optional) |
430FSe | S43023 | 16–18 | - | 0.12 | 1.25 | 1 | 0.06 | 0.06 | - | 0.15 Se min |
434 | S43400 | 16–18 | - | 0.12 | 1 | 1 | 0.04 | 0.03 | - | 0.75–1.25 Mo |
436 | S43600 | 16–18 | - | 0.12 | 1 | 1 | 0.04 | 0.03 | - | 0.75–1.25 Mo; Nb+Ta 5 x C min, 0.70 max |
442 | S44200 | 18–23 | - | 0.2 | 1 | 1 | 0.04 | 0.03 | - | - |
446 | S44600 | 23–27 | 0.25 | 0.2 | 1.5 | 1 | 0.04 | 0.03 | - | - |
SAE designation | UNS designation | % Cr | % Ni | % C | % Mn | % Si | % P | % S | % N | Other |
Martensitic | ||||||||||
403 | S40300 | 11.5–13.0 | 0.60 | 0.15 | 1 | 0.5 | 0.04 | 0.03 | - | - |
410 | S41000 | 11.5–13.5 | 0.75 | 0.15 | 1 | 1 | 0.04 | 0.03 | - | - |
414 | S41400 | 11.5–13.5 | 1.25–2.50 | 0.15 | 1 | 1 | 0.04 | 0.03 | - | - |
416 | S41600 | 12–14 | - | 0.15 | 1.25 | 1 | 0.06 | 0.15 min | - | 0.060 Mo (optional) |
416Se | S41623 | 12–14 | - | 0.15 | 1.25 | 1 | 0.06 | 0.06 | - | 0.15 Se min |
420 | S42000 | 12–14 | - | 0.15 min | 1 | 1 | 0.04 | 0.03 | - | - |
420F | S42020 | 12–14 | - | 0.15 min | 1.25 | 1 | 0.06 | 0.15 min | - | 0.60 Mo max (optional) |
422 | S42200 | 11.0–12.5 | 0.50–1.0 | 0.20–0.25 | 0.5–1.0 | 0.5 | 0.025 | 0.025 | - | 0.90–1.25 Mo; 0.20–0.30 V; 0.90–1.25 W |
431 | S41623 | 15–17 | 1.25–2.50 | 0.2 | 1 | 1 | 0.04 | 0.03 | - | - |
440A | S44002 | 16–18 | - | 0.60–0.75 | 1 | 1 | 0.04 | 0.03 | - | 0.75 Mo |
440B | S44003 | 16–18 | - | 0.75–0.95 | 1 | 1 | 0.04 | 0.03 | - | 0.75 Mo |
440C | S44004 | 16–18 | - | 0.95–1.20 | 1 | 1 | 0.04 | 0.03 | - | 0.75 Mo |
SAE designation | UNS designation | % Cr | % Ni | % C | % Mn | % Si | % P | % S | % N | Other |
Heat resisting | ||||||||||
501 | S50100 | 4–6 | - | 0.10 min | 1 | 1 | 0.04 | 0.03 | - | 0.40–0.65 Mo |
502 | S50200 | 4–6 | - | 0.1 | 1 | 1 | 0.04 | 0.03 | - | 0.40–0.65 Mo |
Duplex | ||||||||||
2205 | S31803 S32205 |
22 | 5 | 0.03 max | - | - | - | - | 0.15 | 3 Mo; All values nominal |
2304 | S32304 | 23 | 4 | 0.03 max | - | 1.00 max | 0.04 max | 0.04 max | 0.15 | 0.10-0.60 Mo |
Super duplex | ||||||||||
2507 | S32750 | 25 | 7 | 0.03 max | - | - | - | - | 0.28 | 4 Mo; All values nominal |
Martensitic precipitation hardening | ||||||||||
630 | S17400 | 15-17 | 3-5 | 0.07 | 1 | 1 | 0.04 | 0.03 | - | Cu 3-5, Ta 0.15-0.45 |
See also
- ASTM InternationalASTM InternationalASTM International, known until 2001 as the American Society for Testing and Materials , is an international standards organization that develops and publishes voluntary consensus technical standards for a wide range of materials, products, systems, and services...
- EN standard
- Steel gradesSteel gradesSteel grades to classify various steels by their composition and physical properties have been developed by a number of standards organizations.*SAE steel grades*British Standards*International Organization for Standardization ISO/TS 4949:2003...
- Unified numbering systemUnified numbering systemThe unified numbering system is an alloy designation system widely accepted in North America. It consists of a prefix letter and five digits designating a material composition. A prefix of S indicates stainless steel alloys, C for copper, brass, or bronze alloys, T for tool steels, etc...