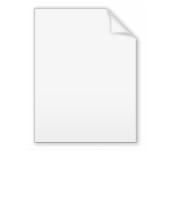
Automated optical inspection
Encyclopedia
Automated optical inspection (AOI) is an automated visual inspection of a wide range of products, such as printed circuit board
s (PCBs), LCDs, transistor
s, automotive parts, lids and labels on product packages or agricultural products (seed corn or fruits). In case of PCB-inspection, a camera autonomously scans the device under test
(DUT) for variety of surface feature defects such as scratches and stains, open circuits, short circuits, thinning of the solder as well as missing components, incorrect components, and incorrectly placed components. Agricultural inspections might check for variations in part color, perhaps to find ripe fruit. AOI is a type of white box testing
. It is commonly used in the manufacturing process because it is a non-contact test method. AOI is able to perform most of the visual checks performed previously by manual operators, and far more swiftly and accurately. AOI systems are implemented at many stages through the manufacturing process. They are used for inspecting parts that have limited and known variations. For defect or flaw detection, the AOI system looks for differences from a perfect part.
There are systems capable of bare board inspection, Solder Paste inspection (SPI), as well as inspecting the component placement prior to reflow, the post-reflow component conditions, and post-reflow solder joints
. These inspection devices all have some common attributes that affect capability, accuracy, and reliability.
In this way AOI can be used to detect problems early in the production process. Since faults cost more to fix later in the production process, it is essential to notice problems early. For example, problems in the solder and assembly area of a PCB can be seen early in the production process and information used to feedback quickly to previous stages, avoiding the production of too many boards with the same problem.
Low costs and programming efforts make AOI a practical and powerful quality tool for both prototypes and high-volume assembles.
It is often paired with the testing provided by boundary scan
test, in-circuit test
, x-ray test, and functional test.
In many cases, smaller circuit board designs are driving up the demand for AOI versus in-circuit test.
or an AOI system can acquire millions of data points (pixels) in a fraction of a second. These data points are used for visual inspection and precision measurement.
AOI visually scans the surface of the PCB. The board is lit by several light sources and observed by a scanner or by a number of high definition cameras. This enables the monitoring of all areas of the board, even those hidden in one direction by other components. It should be noted that each manufacturer of AOI systems utilizes different inspection algorithms and lighting techniques, each of these systems may have varying strengths and weaknesses depending upon the item/product it is inspecting.
The test engineer has the option to choose which light source to use for the lighting: a LED
, fluorescent light
, or in certain industries other light sources such as IR or UV. This depends on the area to be inspected, industry, and other variables. Some users believe that LED light measures post-print solder brick height more accurately than a fluorescent light source. This accuracy also makes LED light a good tool for post-reflow solder joint inspection. Fluorescent light, on the other hand is excellent for inspection of component placement pre-reflow but is typically used for location inspection only. The problem with it is that because of the frequent light changes the fluorescent lamps can degrade quickly. For these above reasons LED lighting has become very popular among most AOI companies in the PCB industry.
The adoption of standard LED-based lighting has improved AOI systems because it is very stable and easily controlled when compared to older incandescent and fluorescent lighting. LEDs are not perfect: they become darker with age, but this can be easily compensated for by increasing the current to the LED or group of LEDs.
Another lighting method projects a pattern of light on an object, often by using a laser
with a holographic lens or a white light source with an attached projection grid. The distortions of this structured light pattern can be measured and processed to recover the object's 3D structure. AOI systems using structured light can, for example, compare complex objects such as engine blocks or PCBs to the designed shape in CAD files. These techniques in the PCB industry are referred to as laser triangulation and phase shift profilometry Profilometer
respectively. Both are valid techniques for acquiring three dimensional (3-D) information from the PCB
The position of the light sources and laser inside the machine are important. Angles of approach are calculated into the inspection algorithms providing enhanced accuracy of the measurements. Also the angle of approach can be particularly important in certain applications because surrounding objects may interfere with the light approach to the target object. An example would be a tall component on a circuit board that blocks the visual approach of the light/camera system to the target component or solder deposit for example.
Then the type of cameras must be chosen. There are several types in use today. Streaming video 2D frame grabbers are common. They utilize a motion capture video camera that extracts one frame from a streaming video and creates a still image. However, the system sacrifices image quality for speed and efficiency.
A second type of camera imaging system is the Line Scan Still Image Camera. In this system, a still camera is placed relatively close to the target. Because of this, this system requires a very good lighting system. Unfortunately, the image can be distorted by subsystem imperfections such as transporter movement. This makes obtaining precise positioning and measurements difficult when compared to other types of systems. A benefit of the Line Scan Still Image Camera is the image acquisition speed, which is faster than a CCD camera
.
Another camera imaging system is the 2D Charge-coupled device
or CCD. The CCD is used for high-end and special applications such as space and military technologies. This system creates high precision still images in color that are more accurate than other systems.
Each industry is different in how image acquisition signals are transferred to the camera. It can be hardware driven via a mechanical signal such as a proximity sensor, laser interruption, drive system encoder position, or software. Regardless of the signal the AOI system interprets the signal which triggers the vision assembly (which could be a single frame grabber and camera combination or more advanced as already discussed) that the object is in a known location and to begin image acquisition. The vision computer then triggers the camera/cameras to simultaneously acquire images of the device.
The AOI system needs to be able to add the learned information acquired from the above inspection techniques to its memory. It has to "remember" the different types of components, their positions and also to check the quality of the soldered joints. It must be able to recognize and adapt to differences in the appearances of the board resulting from normal process variations, but must be able to recognize any that affect performance. To achieve this it is normal to run a number of good boards (golden boards) through the system before full production starts so that the system can "learn" the board. Currently the best AOI machines can be set up relatively quickly and then they are reliably able to inspect boards.
This can be done by offline programming. This reduces production downtime, and the programmer has time to enter accurate parameters without stopping an assembly line. These systems also have a component database that saves data so that it does not have to be entered every time a new board is produced.
In case of automotive parts inspection for example, the system should know what features to measure or for sorting agricultural products the color of ripe fruit should be known.
(SPC) results in these areas. The results of the inspection are used to reject defective parts.
To reduce the computation required by the vision computer so that parts are quickly inspected it is a good idea to use a type of mechanical restraint known as staging or fixturing
. The part is positioned in a known location and variability in where the parts are and how they look is decreased.
Other data collection concerns are factory software integration of inspection results, how long to keep the data/measurements, and what data is available. Each AOI system is going to vary in what is available and each industry and customer will have varying needs. For example military and aerospace industries may have the need to store data for years or until the expected end of life (EOL) of a product while commercial manufacturing such as mobile phones may only require data for a few weeks or possibly even just for that day or shift.
Accuracy of inspection is becoming even more important with the smaller devices especially in the PCB industry devices such as 0201 and 01005 resistors and capacitors are so small that the human eye can not detect their presence or absence on a PCB.
Inline systems on the other hand are part of the production line so the PCBs move into and go out of the machine automatically.
Closed-top machines eliminate any light pollution
because they are closed from all sides. In this way only artificial light is available inside the machine making these type of systems much more efficient.
(AXI), ball grid array
(BGA) and "J" leaded components are limited to polarity, missing, and placement error detection. That is why Combined AOI/AXI systems can provide the necessary mixture for high-performance and are becoming more and more popular.
equipment is reducing the need for expensive rework and repair while increasing throughput. As PCB assembly manufacturers aim for a zero-tolerance regime, the demand for pre-solder paste and pre-reflow optical inspection equipment that detect faults such as poor quality solder joints, tombstoning, and other post reflow defects is expected to rise significantly.
Technological improvements in AOI equipment have resulted in higher throughput, repeatability, and reliability as well as increasing quality and production yields for the PCB assembly manufacturers.
AOI's for a PCB board with components may inspect the following features:
The triggering of a defects report may be either rule based (e.g. no lines on the board should be smaller than 50μ) or CAD based in which the board is locally compared with the intended design.
This inspection is much more reliable and repeatable than manual visual inspection.
Printed circuit board
A printed circuit board, or PCB, is used to mechanically support and electrically connect electronic components using conductive pathways, tracks or signal traces etched from copper sheets laminated onto a non-conductive substrate. It is also referred to as printed wiring board or etched wiring...
s (PCBs), LCDs, transistor
Transistor
A transistor is a semiconductor device used to amplify and switch electronic signals and power. It is composed of a semiconductor material with at least three terminals for connection to an external circuit. A voltage or current applied to one pair of the transistor's terminals changes the current...
s, automotive parts, lids and labels on product packages or agricultural products (seed corn or fruits). In case of PCB-inspection, a camera autonomously scans the device under test
Device under test
Device under test , also known as unit under test , is a term commonly used to refer to a manufactured product undergoing testing.-In semiconductor testing:...
(DUT) for variety of surface feature defects such as scratches and stains, open circuits, short circuits, thinning of the solder as well as missing components, incorrect components, and incorrectly placed components. Agricultural inspections might check for variations in part color, perhaps to find ripe fruit. AOI is a type of white box testing
White box testing
White-box testing is a method of testing software that tests internal structures or workings of an application, as opposed to its functionality...
. It is commonly used in the manufacturing process because it is a non-contact test method. AOI is able to perform most of the visual checks performed previously by manual operators, and far more swiftly and accurately. AOI systems are implemented at many stages through the manufacturing process. They are used for inspecting parts that have limited and known variations. For defect or flaw detection, the AOI system looks for differences from a perfect part.
There are systems capable of bare board inspection, Solder Paste inspection (SPI), as well as inspecting the component placement prior to reflow, the post-reflow component conditions, and post-reflow solder joints
Reflow soldering
Reflow soldering is a process in which a solder paste is used to temporarily attach one or several electrical components to their contact pads, after which the entire assembly is subjected to controlled heat, which melts the solder, permanently connecting the joint...
. These inspection devices all have some common attributes that affect capability, accuracy, and reliability.
In this way AOI can be used to detect problems early in the production process. Since faults cost more to fix later in the production process, it is essential to notice problems early. For example, problems in the solder and assembly area of a PCB can be seen early in the production process and information used to feedback quickly to previous stages, avoiding the production of too many boards with the same problem.
Low costs and programming efforts make AOI a practical and powerful quality tool for both prototypes and high-volume assembles.
It is often paired with the testing provided by boundary scan
Boundary scan
Boundary scan is a method for testing interconnects on printed circuit boards or sub-blocks inside an integrated circuit. Boundary scan is also widely used as a debugging method to watch integrated circuit pin states, measure voltage, or analyze sub-blocks inside an integrated circuit.The Joint...
test, in-circuit test
In-circuit test
In-circuit test is an example of white box testing where an electrical probe tests a populated printed circuit board , checking for shorts, opens, resistance, capacitance, and other basic quantities which will show whether the assembly was correctly fabricated...
, x-ray test, and functional test.
In many cases, smaller circuit board designs are driving up the demand for AOI versus in-circuit test.
Process
A machine visionMachine vision
Machine vision is the process of applying a range of technologies and methods to provide imaging-based automatic inspection, process control and robot guidance in industrial applications. While the scope of MV is broad and a comprehensive definition is difficult to distil, a "generally accepted...
or an AOI system can acquire millions of data points (pixels) in a fraction of a second. These data points are used for visual inspection and precision measurement.
AOI visually scans the surface of the PCB. The board is lit by several light sources and observed by a scanner or by a number of high definition cameras. This enables the monitoring of all areas of the board, even those hidden in one direction by other components. It should be noted that each manufacturer of AOI systems utilizes different inspection algorithms and lighting techniques, each of these systems may have varying strengths and weaknesses depending upon the item/product it is inspecting.
Light source
Lighting preprocesses the image to amplify features that need to be inspected and suppress noise. Advances in lighting have improved the capabilities of vision systems, in part by reducing the computation required by the vision computer. In essence this means that the lighting combinations ideally will improve the image quality to improve the efficiency of the AOI system's decision making process. Most AOI systems will have predefined lighting combinations depending upon the mode of operation and type of product being inspected, these combinations will require no user interaction and the system software/algorithms will manipulate and choose the best image for analysis. However some customization is often required and with that these systems will provide interfacing for the end user.The test engineer has the option to choose which light source to use for the lighting: a LED
LEd
LEd is a TeX/LaTeX editing software working under Microsoft Windows. It is a freeware product....
, fluorescent light
Fluorescent lamp
A fluorescent lamp or fluorescent tube is a gas-discharge lamp that uses electricity to excite mercury vapor. The excited mercury atoms produce short-wave ultraviolet light that then causes a phosphor to fluoresce, producing visible light. A fluorescent lamp converts electrical power into useful...
, or in certain industries other light sources such as IR or UV. This depends on the area to be inspected, industry, and other variables. Some users believe that LED light measures post-print solder brick height more accurately than a fluorescent light source. This accuracy also makes LED light a good tool for post-reflow solder joint inspection. Fluorescent light, on the other hand is excellent for inspection of component placement pre-reflow but is typically used for location inspection only. The problem with it is that because of the frequent light changes the fluorescent lamps can degrade quickly. For these above reasons LED lighting has become very popular among most AOI companies in the PCB industry.
The adoption of standard LED-based lighting has improved AOI systems because it is very stable and easily controlled when compared to older incandescent and fluorescent lighting. LEDs are not perfect: they become darker with age, but this can be easily compensated for by increasing the current to the LED or group of LEDs.
Another lighting method projects a pattern of light on an object, often by using a laser
Laser
A laser is a device that emits light through a process of optical amplification based on the stimulated emission of photons. The term "laser" originated as an acronym for Light Amplification by Stimulated Emission of Radiation...
with a holographic lens or a white light source with an attached projection grid. The distortions of this structured light pattern can be measured and processed to recover the object's 3D structure. AOI systems using structured light can, for example, compare complex objects such as engine blocks or PCBs to the designed shape in CAD files. These techniques in the PCB industry are referred to as laser triangulation and phase shift profilometry Profilometer
Profilometer
Profilometer is a measuring instrument used to measure a surface's profile, in order to quantify its roughness.While the historical notion of a profilometer was a device similar to a phonograph that measures a surface as the surface is moved relative to the contact profilometer's stylus, this...
respectively. Both are valid techniques for acquiring three dimensional (3-D) information from the PCB
The position of the light sources and laser inside the machine are important. Angles of approach are calculated into the inspection algorithms providing enhanced accuracy of the measurements. Also the angle of approach can be particularly important in certain applications because surrounding objects may interfere with the light approach to the target object. An example would be a tall component on a circuit board that blocks the visual approach of the light/camera system to the target component or solder deposit for example.
Capturing an image
If a scanner is used it has to scan the surface of the PCB from above only once. If image cameras are used, one must first determine the number of cameras needed. There are systems with only one camera which scans the DUT from above and systems with a couple of cameras from all sides. To be able to scan the device from all points of view, the cameras should be able to move in both X- and Y-direction controlled by software. To program this software the test engineer must have the CAD data.Then the type of cameras must be chosen. There are several types in use today. Streaming video 2D frame grabbers are common. They utilize a motion capture video camera that extracts one frame from a streaming video and creates a still image. However, the system sacrifices image quality for speed and efficiency.
A second type of camera imaging system is the Line Scan Still Image Camera. In this system, a still camera is placed relatively close to the target. Because of this, this system requires a very good lighting system. Unfortunately, the image can be distorted by subsystem imperfections such as transporter movement. This makes obtaining precise positioning and measurements difficult when compared to other types of systems. A benefit of the Line Scan Still Image Camera is the image acquisition speed, which is faster than a CCD camera
Charge-coupled device
A charge-coupled device is a device for the movement of electrical charge, usually from within the device to an area where the charge can be manipulated, for example conversion into a digital value. This is achieved by "shifting" the signals between stages within the device one at a time...
.
Another camera imaging system is the 2D Charge-coupled device
Charge-coupled device
A charge-coupled device is a device for the movement of electrical charge, usually from within the device to an area where the charge can be manipulated, for example conversion into a digital value. This is achieved by "shifting" the signals between stages within the device one at a time...
or CCD. The CCD is used for high-end and special applications such as space and military technologies. This system creates high precision still images in color that are more accurate than other systems.
Each industry is different in how image acquisition signals are transferred to the camera. It can be hardware driven via a mechanical signal such as a proximity sensor, laser interruption, drive system encoder position, or software. Regardless of the signal the AOI system interprets the signal which triggers the vision assembly (which could be a single frame grabber and camera combination or more advanced as already discussed) that the object is in a known location and to begin image acquisition. The vision computer then triggers the camera/cameras to simultaneously acquire images of the device.
Programming
The AOI system takes time to "learn" the object which in the PCB industry is typically a circuit board. Several methods of learning exist but the two most common are image matching and algorithm based. Image matching is when a "golden board" is introduced to the system and the attributes of each component, solder deposit, etc. are learned into the system. This could include but not limited to color, white pixel count, dark pixel count, transition points, and relative position of transition points. Image based systems require a few example products typically to learn all possible variations. The other method is algorithm based programming; this is where the user can apply rules and measurement algorithms for inspection. Algorithm based programming typically also requires product examples for programming but not usually as many as image based programming. There are pros and cons for each technique which can include setup time, complexity of the system, program transportability, time to generate a program, and call effectiveness.The AOI system needs to be able to add the learned information acquired from the above inspection techniques to its memory. It has to "remember" the different types of components, their positions and also to check the quality of the soldered joints. It must be able to recognize and adapt to differences in the appearances of the board resulting from normal process variations, but must be able to recognize any that affect performance. To achieve this it is normal to run a number of good boards (golden boards) through the system before full production starts so that the system can "learn" the board. Currently the best AOI machines can be set up relatively quickly and then they are reliably able to inspect boards.
This can be done by offline programming. This reduces production downtime, and the programmer has time to enter accurate parameters without stopping an assembly line. These systems also have a component database that saves data so that it does not have to be entered every time a new board is produced.
In case of automotive parts inspection for example, the system should know what features to measure or for sorting agricultural products the color of ripe fruit should be known.
Data collection
To obtain the necessary data one can use 3D software imaging or LED light measurements, which are common methods for measuring solder joint parameters. Typical systems use both methods to obtain accurate measurements. These systems use a directed light source or refracting light to measure height, area, and volume. The vision computer and its software analyze data (images) and calculate statistical process controlStatistical process control
Statistical process control is the application of statistical methods to the monitoring and control of a process to ensure that it operates at its full potential to produce conforming product. Under SPC, a process behaves predictably to produce as much conforming product as possible with the least...
(SPC) results in these areas. The results of the inspection are used to reject defective parts.
To reduce the computation required by the vision computer so that parts are quickly inspected it is a good idea to use a type of mechanical restraint known as staging or fixturing
Fixture (tool)
A fixture is a work-holding or support device used in the manufacturing industry. What makes a fixture unique is that each one is built to fit a particular part or shape. The main purpose of a fixture is to locate and in some cases hold a workpiece during either a machining operation or some...
. The part is positioned in a known location and variability in where the parts are and how they look is decreased.
Other data collection concerns are factory software integration of inspection results, how long to keep the data/measurements, and what data is available. Each AOI system is going to vary in what is available and each industry and customer will have varying needs. For example military and aerospace industries may have the need to store data for years or until the expected end of life (EOL) of a product while commercial manufacturing such as mobile phones may only require data for a few weeks or possibly even just for that day or shift.
System memory
System memory is also important. Upgradeable systems that have the capacity for expanded memory are desirable. Databases expand every day particularly with the increase in lead-free components, solders, boards and assemblies that are rapidly entering the industry.System speed
System speed is influenced largely by the size and complexity of the boards being inspected and the level of inspection. Control over the pace of the production line can be influenced by the AOI system. Since one hundred percent inspection is not always necessary, valuable time can be saved by dialing in the appropriate inspection level.System accuracy
The accuracy for finding defects such as missing components, skewed components, reversed components, or wrong valued components depends not only on the capability of the inspection system but also on the accuracy of the program supplied by the user.Accuracy of inspection is becoming even more important with the smaller devices especially in the PCB industry devices such as 0201 and 01005 resistors and capacitors are so small that the human eye can not detect their presence or absence on a PCB.
Stand-alone and inline AOI systems
When using Stand-alone machines the PCB has to be inserted into and after the test taken out of the machine manually.Inline systems on the other hand are part of the production line so the PCBs move into and go out of the machine automatically.
Closed- and open-top AOI systems
Inside Open-top machines the artificial light is distracted by light sources different than the ones used by the system itself (e.g. sunlight).Closed-top machines eliminate any light pollution
Light pollution
Light pollution, also known as photopollution or luminous pollution, is excessive or obtrusive artificial light.The International Dark-Sky Association defines light pollution as:...
because they are closed from all sides. In this way only artificial light is available inside the machine making these type of systems much more efficient.
AOI and combined AOI/AXI systems
Today's AOI systems have the capability to inspect visible solder joints on capacitors, resistors, and other components. However, without additional capabilities such as Automated x-ray inspectionAutomated x-ray inspection
Automated inspection is a technology based on the same principles as automated optical inspection . It uses as its source, instead of visible light, to automatically inspect features, which are typically hidden from view....
(AXI), ball grid array
Ball grid array
A ball grid array is a type of surface-mount packaging used for integrated circuits.- Description :The BGA is descended from the pin grid array , which is a package with one face covered with pins in a grid pattern. These pins conduct electrical signals from the integrated circuit to the printed...
(BGA) and "J" leaded components are limited to polarity, missing, and placement error detection. That is why Combined AOI/AXI systems can provide the necessary mixture for high-performance and are becoming more and more popular.
Inspection in surface-mount technology
The growing demand for Surface-mount technologySurface-mount technology
Surface mount technology is a method for constructing electronic circuits in which the components are mounted directly onto the surface of printed circuit boards . An electronic device so made is called a surface mount device...
equipment is reducing the need for expensive rework and repair while increasing throughput. As PCB assembly manufacturers aim for a zero-tolerance regime, the demand for pre-solder paste and pre-reflow optical inspection equipment that detect faults such as poor quality solder joints, tombstoning, and other post reflow defects is expected to rise significantly.
Technological improvements in AOI equipment have resulted in higher throughput, repeatability, and reliability as well as increasing quality and production yields for the PCB assembly manufacturers.
AOI's for a PCB board with components may inspect the following features:
- Area Defects
- Billboarding
- Component offset
- Component polarity
- Component presence/absence
- Component skew
- Excessive solder joints
- Flipped component
- Height Defects
- Insufficient paste around Leads
- Insufficient solder joints
- Lifted leads
- No-population tests
- Paste registration
- Severely damaged components
- Solder bridges
- Tombstoning
- Volume defects
- Wrong part
Bare PCB inspection
AOI for a bare PCB board inspection may detect these features:- Line width violations.
- Spacing violation.
- Excess copper.
- Missing pad. I.e. a feature that should be on the board is missing.
- Shorts circuits.
- Cuts.
- Hole breakage. I.e. a drilled hole (via) is outside of its landing pad.
The triggering of a defects report may be either rule based (e.g. no lines on the board should be smaller than 50μ) or CAD based in which the board is locally compared with the intended design.
This inspection is much more reliable and repeatable than manual visual inspection.
Related technologies
The following are related technologies and are also used in electronic production to test for the correct operation of Electronics Printed Circuit boards- AXI Automated x-ray inspectionAutomated x-ray inspectionAutomated inspection is a technology based on the same principles as automated optical inspection . It uses as its source, instead of visible light, to automatically inspect features, which are typically hidden from view....
- JTAG Joint Test Action Group
- ICT In-circuit testIn-circuit testIn-circuit test is an example of white box testing where an electrical probe tests a populated printed circuit board , checking for shorts, opens, resistance, capacitance, and other basic quantities which will show whether the assembly was correctly fabricated...
- Functional testing
- under vehicle inspectionUnder vehicle inspectionAn under-vehicle inspection system generally consists of still or video cameras mounted within a ramp and used at facility access points, particularly at secure facilities. An under-vehicle inspection system is used to detect threats—such as bombs—that are hidden underneath vehicles...
External links
- Automated optical inspection overview
- AOI-Systems (ORPROVision) − AOI-Systems (ORPROVision AOI)