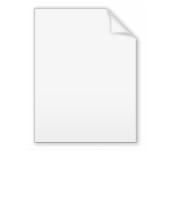
Automatic Continuous Online Monitoring of Polymerization Reactions
Encyclopedia
Automatic continuous online monitoring of polymerization reactions (ACOMP) was developed at Tulane University
by Prof. Reed in 1998, with the first publication appearing in 1998. Polymerization reactions are difficult to monitor in real-time, so characteristics and properties of the polymers aren't known, oftentimes, until after the reaction is already complete. ACOMP monitors these reactions in real-time by automatically and continuously diluting small streams of polymer out of the reactor and then running the sample though widely accepted detectors such as Refractive Index, Light Scattering, and Intrinsic Viscosity to completely characterize the polymer as it is being "born." ACOMP can be used as an analytical method in R&D, as a tool for reaction optimization at the bench and pilot plant level and, eventually, for feedback control of full-scale reactors. ACOMP measures in a model-independent fashion the evolution of average molar mass and intrinsic viscosity, monomer conversion kinetics and, in the case of copolymers, also the average composition drift and distribution. ACOMP is applicable in the areas of free radical and controlled radical homo- and copolymerization, polyelectrolyte synthesis, heterogeneous phase reactions, including emulsion polymerization, adaptation to batch and continuous reactors, and modifications of polymers.
in New Orleans, Louisiana
uses this technology for its various research projects.
The ACOMP 'front-end' samples the reactor continuously, producing a dilute and highly conditioned sample stream on which multiple analytical measurements are simultaneously and continuously made. These include light scattering, viscosity, refractivity, conductivity, ultra-violet absorption, etc. The types of instruments can be tailored to the specific application. This massive data flow yields at each instant the amount of reagents converted to polymer, polymer molecular weight, intrinsic viscosity, average composition drift and distribution, and many other properties. ACOMP gives a comprehensive picture of what is occurring in the polymerization reactor, so that it is known when the reaction is complete, if there are problems during the reaction, and whether the product is being produced according to specification. With this, optimum energy efficiency and product quality can be achieved through online adjustments to process variables, such as temperature, pressure, reagent feed rates, reaction time, etc.
With the wealth of data that it provides, ACOMP is the most useful choice for anyone attempting to monitor and characterize polymerization reactions in an R&D or industrial setting. Current monitoring methods for polymerization reactions are limited in scope. In-situ probes, such as Fourier Transform Infra-Red (FTIR) and Raman scattering can provide measures of monomer conversion only, but no direct measures of molecular weight or other characteristics, such as the onset of microgelation or other problems. These probes require empirical models and calibration schemes and can easily foul in harsh reactor environments. Alternatively, samples manually extracted from the reactor are often simply measured off-line using traditional analytical methods, such as gas chromatography. This can involve technicians literally running constantly between the plant and the analytical lab, introducing large lag times between sample collection and results, by which time something has potentially already gone wrong in the reaction. This approach is inefficient, makes poor use of personnel time, and often exposes technicians to safety risks. Other methods involve post-reaction analysis of failed batches, to ascertain what went wrong during the polymerization. All of these methods have some utility but are inferior to the advantage provided by the widely applicable ACOMP platform for monitoring the reaction continuously and comprehensively online with potential for feedback loops for reaction control.
ACOMP is fully proven at the laboratory level, and was commercially available for this use under license from Varian Inc., up until the beginning of 2009. Due to the current financial crisis and massive layoffs, however, Varian Inc. cancelled the license with Tulane for the ACOMP patents, and now PolyRMC is seeking to develop the technology further. Specifically, PolyRMC is looking for potential collaborators for a technology transfer on a non-profit basis through the Center. This would involve preliminary testing to prove the feasibility of adapting the technology to a specific product. It would also involve actual implementation on a larger scale reactor i.e. a pilot reactor or even a full-sized reactor.
The potential for decreasing reaction times by running reactions closer to their thresholds could provide energy savings, and increase output without any further capital investments. Monitoring reactions in real-time can also provide data on the quality of the polymer being produced so that product consistency can be controlled more closely, and finally wasted batches, due to failed polymerizations, can be eliminated. All of these advantages could make ACOMP very cost-advantageous for any end-users of the technology, and help to increase the overall efficiency of the polymer manufacturing sector as a whole. Other potential national or global impact of ACOMP mass-adaptation may include 1) saving petroleum based and other non-renewable resources in polymer production, 2) advances in novel material properties, quality, versatility, yield, and applications which can lead to better energy saving materials, such as light-weight construction and transportation materials, oil recovery polymers, etc., 3) less greenhouse gas emission per pound of product, 4) less chemical contamination of soil, water, air and surrounding communities and 5) enhanced profitability due to efficiency and quality gains, leading to 6) retention and expansion of this manufacturing sector in the US, with its broad spectrum of blue and white collar jobs, and 7) a quantitative basis for evaluating energy efficiency of polymer manufacturing.
Diagram of an ACOMP set-up
Tulane University
Tulane University is a private, nonsectarian research university located in New Orleans, Louisiana, United States...
by Prof. Reed in 1998, with the first publication appearing in 1998. Polymerization reactions are difficult to monitor in real-time, so characteristics and properties of the polymers aren't known, oftentimes, until after the reaction is already complete. ACOMP monitors these reactions in real-time by automatically and continuously diluting small streams of polymer out of the reactor and then running the sample though widely accepted detectors such as Refractive Index, Light Scattering, and Intrinsic Viscosity to completely characterize the polymer as it is being "born." ACOMP can be used as an analytical method in R&D, as a tool for reaction optimization at the bench and pilot plant level and, eventually, for feedback control of full-scale reactors. ACOMP measures in a model-independent fashion the evolution of average molar mass and intrinsic viscosity, monomer conversion kinetics and, in the case of copolymers, also the average composition drift and distribution. ACOMP is applicable in the areas of free radical and controlled radical homo- and copolymerization, polyelectrolyte synthesis, heterogeneous phase reactions, including emulsion polymerization, adaptation to batch and continuous reactors, and modifications of polymers.
ACOMP as a tool for efficiency
ACOMP is envisioned as an energy saving and efficiency optimizing technology for the polymer manufacturing industry. The possibility for feedback control in polymerization reactions presents manufacturers with a tool to improve the efficiency of their process by instantly seeing the properties of the polymers as they produce them essentially creating polymers that are "Born Characterized." Different reaction parameters such as temperature, pressure, and reagent feeds can be adjusted according to what ACOMP analyzes in real-time thus maximizing the efficiency of the reaction and reducing the common problem of inconsistent product quality and wasted batches. The non-profit Tulane Center for Polymer Reaction Monitoring and Characterization (PolyRMC) at Tulane UniversityTulane University
Tulane University is a private, nonsectarian research university located in New Orleans, Louisiana, United States...
in New Orleans, Louisiana
Louisiana
Louisiana is a state located in the southern region of the United States of America. Its capital is Baton Rouge and largest city is New Orleans. Louisiana is the only state in the U.S. with political subdivisions termed parishes, which are local governments equivalent to counties...
uses this technology for its various research projects.
Description
PolyRMC founding director, Professor Wayne Reed and coworkers invented an instrument platform for monitoring a wide array of polymerization reactions in real-time. This proprietary platform, termed Automatic Continuous Online Monitoring of Polymerization reactions, or ACOMP, has been demonstrated in the laboratory environment since 1998, with over 30 publications in high-impact, peer-reviewed journals. , ACOMP monitors and analyzes polymerization reactions as they occur. ACOMP has been applied to polycondensation, free radical, controlled radical, other 'living' type reactions, and post-polymerization reactions, such as grafting, etc., and has been applied in solvent, bulk and inhomogeneous phases, such as emulsion and inverse emulsion, and in batch, semi-continuous and continuous reactors.The ACOMP 'front-end' samples the reactor continuously, producing a dilute and highly conditioned sample stream on which multiple analytical measurements are simultaneously and continuously made. These include light scattering, viscosity, refractivity, conductivity, ultra-violet absorption, etc. The types of instruments can be tailored to the specific application. This massive data flow yields at each instant the amount of reagents converted to polymer, polymer molecular weight, intrinsic viscosity, average composition drift and distribution, and many other properties. ACOMP gives a comprehensive picture of what is occurring in the polymerization reactor, so that it is known when the reaction is complete, if there are problems during the reaction, and whether the product is being produced according to specification. With this, optimum energy efficiency and product quality can be achieved through online adjustments to process variables, such as temperature, pressure, reagent feed rates, reaction time, etc.
With the wealth of data that it provides, ACOMP is the most useful choice for anyone attempting to monitor and characterize polymerization reactions in an R&D or industrial setting. Current monitoring methods for polymerization reactions are limited in scope. In-situ probes, such as Fourier Transform Infra-Red (FTIR) and Raman scattering can provide measures of monomer conversion only, but no direct measures of molecular weight or other characteristics, such as the onset of microgelation or other problems. These probes require empirical models and calibration schemes and can easily foul in harsh reactor environments. Alternatively, samples manually extracted from the reactor are often simply measured off-line using traditional analytical methods, such as gas chromatography. This can involve technicians literally running constantly between the plant and the analytical lab, introducing large lag times between sample collection and results, by which time something has potentially already gone wrong in the reaction. This approach is inefficient, makes poor use of personnel time, and often exposes technicians to safety risks. Other methods involve post-reaction analysis of failed batches, to ascertain what went wrong during the polymerization. All of these methods have some utility but are inferior to the advantage provided by the widely applicable ACOMP platform for monitoring the reaction continuously and comprehensively online with potential for feedback loops for reaction control.
ACOMP is fully proven at the laboratory level, and was commercially available for this use under license from Varian Inc., up until the beginning of 2009. Due to the current financial crisis and massive layoffs, however, Varian Inc. cancelled the license with Tulane for the ACOMP patents, and now PolyRMC is seeking to develop the technology further. Specifically, PolyRMC is looking for potential collaborators for a technology transfer on a non-profit basis through the Center. This would involve preliminary testing to prove the feasibility of adapting the technology to a specific product. It would also involve actual implementation on a larger scale reactor i.e. a pilot reactor or even a full-sized reactor.
The potential for decreasing reaction times by running reactions closer to their thresholds could provide energy savings, and increase output without any further capital investments. Monitoring reactions in real-time can also provide data on the quality of the polymer being produced so that product consistency can be controlled more closely, and finally wasted batches, due to failed polymerizations, can be eliminated. All of these advantages could make ACOMP very cost-advantageous for any end-users of the technology, and help to increase the overall efficiency of the polymer manufacturing sector as a whole. Other potential national or global impact of ACOMP mass-adaptation may include 1) saving petroleum based and other non-renewable resources in polymer production, 2) advances in novel material properties, quality, versatility, yield, and applications which can lead to better energy saving materials, such as light-weight construction and transportation materials, oil recovery polymers, etc., 3) less greenhouse gas emission per pound of product, 4) less chemical contamination of soil, water, air and surrounding communities and 5) enhanced profitability due to efficiency and quality gains, leading to 6) retention and expansion of this manufacturing sector in the US, with its broad spectrum of blue and white collar jobs, and 7) a quantitative basis for evaluating energy efficiency of polymer manufacturing.
Diagram of an ACOMP set-up