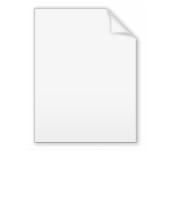
Contract manufacturer
Encyclopedia
A contract manufacturer is a manufacturer that contracts with a firm for components or products. It is a form of outsourcing
.
, defense
, computer
, semiconductor
, energy
, medical, food manufacturing, personal care
, and automotive
fields. Some types of contract manufacturing include CNC machining, complex assembly, aluminum die casting, grinding, broaching, gears, and forging. The pharmaceutical industry utilizes this process with CMs called Contract manufacturing organizations.
to other companies. However, production
outside of the company does come with many risks attached. Companies must identify what their core competencies
are first before deciding whether or not they should contract manufacture. A company’s core competencies
are what make them competitive in the market
place. If a company allows another company to take control of them, it loses control over that advantage.
When making the decision on whether or not a company should contract manufacture, the company should weigh the benefits and risks associated with it. For small companies, contract manufacturing may not be a good business strategy. For large companies that are trying to grow and extend into new markets, contract manufacturing is likely to be a good choice.
.
Outsourcing
Outsourcing is the process of contracting a business function to someone else.-Overview:The term outsourcing is used inconsistently but usually involves the contracting out of a business function - commonly one previously performed in-house - to an external provider...
.
Business model
In a contract manufacturing business model, the hiring firm approaches the contract manufacturer with a design or formula. The contract manufacturer will quote the parts based on processes, labor, tooling, and material costs. Typically a hiring firm will request quotes from multiple CMs. After the bidding process is complete, the hiring firm will select a source, and then, for the agreed-upon price, the CM acts as the hiring firm's factory, producing and shipping units of the design on behalf of the hiring firm.Industries that utilize the practice
Many industries utilize this process, especially the aerospaceAerospace
Aerospace comprises the atmosphere of Earth and surrounding space. Typically the term is used to refer to the industry that researches, designs, manufactures, operates, and maintains vehicles moving through air and space...
, defense
Defense industry
The defense industry, also called the military industry, comprises government and commercial industry involved in research, development, production, and service of military materiel, equipment and facilities...
, computer
Computer industry
Computer industry is a collective term used to describe the whole range of businesses involved in developing computer software, designing computer hardware and computer networking infrastructures, the manufacture of computer components and the provision of information technology services.-See...
, semiconductor
Semiconductor industry
The semiconductor industry is the aggregate collection of companies engaged in the design and fabrication of semiconductor devices. It formed around 1960, once the fabrication of semiconductors became a viable business...
, energy
Energy industry
The energy industry is the totality of all of the industries involved in the production and sale of energy, including fuel extraction, manufacturing, refining and distribution...
, medical, food manufacturing, personal care
Personal care
Personal care or toiletries is the industry which manufactures consumer products used for beautification and in personal hygiene.-Subsectors:Subsectors of personal care include cosmetics and feminine hygiene....
, and automotive
Automotive industry
The automotive industry designs, develops, manufactures, markets, and sells motor vehicles, and is one of the world's most important economic sectors by revenue....
fields. Some types of contract manufacturing include CNC machining, complex assembly, aluminum die casting, grinding, broaching, gears, and forging. The pharmaceutical industry utilizes this process with CMs called Contract manufacturing organizations.
Why Contract Manufacture?
There are many benefits as well as risks to contract manufacturing. Companies are finding many reasons why they should be outsourcing their productionProduction (economics)
In economics, production is the act of creating 'use' value or 'utility' that can satisfy a want or need. The act may or may not include factors of production other than labor...
to other companies. However, production
Production (economics)
In economics, production is the act of creating 'use' value or 'utility' that can satisfy a want or need. The act may or may not include factors of production other than labor...
outside of the company does come with many risks attached. Companies must identify what their core competencies
Core competency
A core competency is a concept in management theory originally advocated by CK Prahalad, and Gary Hamel, two business book writers. In their view a core competency is a specific factor that a business sees as being central to the way it, or its employees, works...
are first before deciding whether or not they should contract manufacture. A company’s core competencies
Core competency
A core competency is a concept in management theory originally advocated by CK Prahalad, and Gary Hamel, two business book writers. In their view a core competency is a specific factor that a business sees as being central to the way it, or its employees, works...
are what make them competitive in the market
Market
A market is one of many varieties of systems, institutions, procedures, social relations and infrastructures whereby parties engage in exchange. While parties may exchange goods and services by barter, most markets rely on sellers offering their goods or services in exchange for money from buyers...
place. If a company allows another company to take control of them, it loses control over that advantage.
When making the decision on whether or not a company should contract manufacture, the company should weigh the benefits and risks associated with it. For small companies, contract manufacturing may not be a good business strategy. For large companies that are trying to grow and extend into new markets, contract manufacturing is likely to be a good choice.
Benefits
- Cost Savings – Companies save on their cost of capitalCost of capitalThe cost of capital is a term used in the field of financial investment to refer to the cost of a company's funds , or, from an investor's point of view "the shareholder's required return on a portfolio of all the company's existing securities"...
because they do not have to pay for a facility and the equipment needed for productionProduction (economics)In economics, production is the act of creating 'use' value or 'utility' that can satisfy a want or need. The act may or may not include factors of production other than labor...
. They can also save on labor costs such as wages, training and benefits. Some companies may look to contract manufacture in low-costLow-cost country sourcingLow-cost country sourcing is procurement strategy in which a company sources materials from countries with lower labour and production costs in order to cut operating expenses. LCCS falls under a broad category of procurement efforts called global sourcing. The process of low cost sourcing...
countries, such as China, to benefit from the low cost of labor. - Mutual Benefit to Contract Site – A contract between the manufacturer and the company it’s producing for may last several years. The manufacturer will know that it will have a steady flow of business until then.
- Advanced Skills – Companies can take advantage of skills that they may not possess, but the contract manufacturer does. The contract manufacturer is likely to have relationships formed with raw materialRaw materialA raw material or feedstock is the basic material from which a product is manufactured or made, frequently used with an extended meaning. For example, the term is used to denote material that came from nature and is in an unprocessed or minimally processed state. Latex, iron ore, logs, and crude...
suppliers or methods of efficiency within their productionProduction (economics)In economics, production is the act of creating 'use' value or 'utility' that can satisfy a want or need. The act may or may not include factors of production other than labor...
. - Quality – Contract Manufacturers are likely to have their own methods of qualitycontrol in place that helps them to detect counterfeitCounterfeitTo counterfeit means to illegally imitate something. Counterfeit products are often produced with the intent to take advantage of the superior value of the imitated product...
or damaged materials early on. - Focus– Companies can focus on their core competenciesCore competencyA core competency is a concept in management theory originally advocated by CK Prahalad, and Gary Hamel, two business book writers. In their view a core competency is a specific factor that a business sees as being central to the way it, or its employees, works...
better if they can hand off base productionProduction (economics)In economics, production is the act of creating 'use' value or 'utility' that can satisfy a want or need. The act may or may not include factors of production other than labor...
to an outside company.. - Economies of ScaleEconomies of scaleEconomies of scale, in microeconomics, refers to the cost advantages that an enterprise obtains due to expansion. There are factors that cause a producer’s average cost per unit to fall as the scale of output is increased. "Economies of scale" is a long run concept and refers to reductions in unit...
– Contract Manufacturers have multiple customers that they produce for. Because they are servicing multiple customers, they can offer reduced costs in acquiring raw materialsRaw materialA raw material or feedstock is the basic material from which a product is manufactured or made, frequently used with an extended meaning. For example, the term is used to denote material that came from nature and is in an unprocessed or minimally processed state. Latex, iron ore, logs, and crude...
by benefiting from economies of scaleEconomies of scaleEconomies of scale, in microeconomics, refers to the cost advantages that an enterprise obtains due to expansion. There are factors that cause a producer’s average cost per unit to fall as the scale of output is increased. "Economies of scale" is a long run concept and refers to reductions in unit...
. The more units there are in one shipment, the less expensive the price per unit will be.
Risks
- Lack of Control – As soon as a company signs the contract allowing another company to produce their product, they lose a significant amount of control over that product. They can only suggest strategies to the contract manufacturer; they cannot force them to implement them.
- Relationships - It is imperative that the company forms a good relationship with its contract manufacture. The company must keep in mind that it is not the only customer to the manufacturer. They cannot force them to produce their product before a competitor’s. Most companies mitigate this risk by working cohesively with the manufacturer and awarding good performance with more of their business.
- Quality concerns – When entering into a contract, companies must make sure that the manufacturer’s standards are in line with their own. They should also evaluate the methods in which they test product to make sure the products being produced are of good quality. The company has to rely on the contract manufacturer for having good suppliers that also meet these standards.
- Intellectual PropertyIntellectual propertyIntellectual property is a term referring to a number of distinct types of creations of the mind for which a set of exclusive rights are recognized—and the corresponding fields of law...
Loss – When entering into a contract, a company is letting someone else in on their formulas or technologies. This is why it is very important that a company not give out any of its core competenciesCore competencyA core competency is a concept in management theory originally advocated by CK Prahalad, and Gary Hamel, two business book writers. In their view a core competency is a specific factor that a business sees as being central to the way it, or its employees, works...
to contract manufacturers. It is very easy for an employee to download such information from a computer and steal it. The recent uptake in intellectual propertyIntellectual propertyIntellectual property is a term referring to a number of distinct types of creations of the mind for which a set of exclusive rights are recognized—and the corresponding fields of law...
loss has companies and government officials struggling to find the best method of security. Usually, it comes down to the integrity of the employees. - OutsourcingOutsourcingOutsourcing is the process of contracting a business function to someone else.-Overview:The term outsourcing is used inconsistently but usually involves the contracting out of a business function - commonly one previously performed in-house - to an external provider...
Risks – Although outsourcingOutsourcingOutsourcing is the process of contracting a business function to someone else.-Overview:The term outsourcing is used inconsistently but usually involves the contracting out of a business function - commonly one previously performed in-house - to an external provider...
to low-costLow-cost country sourcingLow-cost country sourcing is procurement strategy in which a company sources materials from countries with lower labour and production costs in order to cut operating expenses. LCCS falls under a broad category of procurement efforts called global sourcing. The process of low cost sourcing...
countries has become very popular, it does bring along risks such as language barriers, cultural differences and long lead times. This could make the management of contract manufacturers more difficult, expensive and time-consuming. - CapacityCapacity utilizationCapacity utilization is a concept in economics and managerial accounting which refers to the extent to which an enterprise or a nation actually uses its installed productive capacity...
Constraints – If a company does not make up a large portion of the contract manufacturer’s business, they may find that they are de-prioritized over other companies during high productionProduction (economics)In economics, production is the act of creating 'use' value or 'utility' that can satisfy a want or need. The act may or may not include factors of production other than labor...
periods. Thus, they may not be able to get the product they need when they need it. - Loss of Flexibility and Responsiveness - Without direct control over the manufacturing facility, the company will lose some of its ability to respond to disruptions in the supply chain. It may also hurt their ability to respond to demand fluctuations, risking their customer service levels.
Protectionism
In an international context, establishing a foreign subsidiary as a contract manufacturer can have favorable tax benefits for the parent company, allowing them to reduce overall tax liabilities and increase profits, depending upon the activities of the contract manufacturer. This is a form of protectionismProtectionism
Protectionism is the economic policy of restraining trade between states through methods such as tariffs on imported goods, restrictive quotas, and a variety of other government regulations designed to allow "fair competition" between imports and goods and services produced domestically.This...
.
See also
- Interactive Contract ManufacturingInteractive Contract ManufacturingInteractive contract manufacturing is a neologism to describe the business model of companies that design, build, and deliver interactive assets for their business partners. In this model, advertising agencies team with an ICM in order to provide their clients with websites, interactive campaigns...
(ICM) - Electronic Contract Manufacturing (ECM)
- Electronics manufacturing servicesElectronics manufacturing servicesElectronic manufacturing services is a term used for companies that design, test, manufacture, distribute, and provide return/repair services for electronic components and assemblies for original equipment manufacturers...
(EMS) - Original design manufacturerOriginal Design ManufacturerAn original design manufacturer is a company which designs and manufactures a product which is specified and eventually branded by another firm for sale. Such companies allow the brand firm to produce without having to engage in the organization or running of a factory...
(ODM) - Private labelPrivate labelPrivate label products or services are typically those manufactured or provided by one company for offer under another company's brand. Private label goods and services are available in a wide range of industries from food to cosmetics to web hosting...
- Bill of materialsBill of materialsA bill of materials is a list of the raw materials, sub-assemblies, intermediate assemblies, sub-components, components, parts and the quantities of each needed to manufacture an end product...
(BOM)