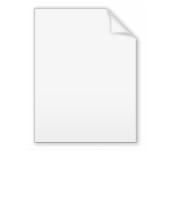
D3o
Encyclopedia
D3O formally "D3o" is a dilatant
material commonly used for impact protection. It has been categorized into smart fabrics and intelligent textiles by the Research and Markets.
The material is believed to lead the innovation of smart fabrics in impact protection.
D3O became widely used in impact protection due to its properties. In its raw state it flows freely when moved slowly, but on shock, locks together to absorb and disperse energy, before instantly returning to its flexible state. This characteristic provides protection, as well as material flexibility, which in turn offers many benefits to the wearer.
Energy is distributed throughout the synthetic elastomeric polymer
and the enhanced chemistry continues to distribute energy on throughout the matrix, reducing the effect of impact.
Immediately after that realization Palmer teamed up with Dr. Phil Green, a fellow co-worker from the University of Hertfordshire’s Research and Development Centre and the two decided that they would make a more versatile and lightweight protection material for the human body.
Palmer was so assured that he was onto something big, he quit his job, sold his home, slept on his friends couch and cashed in on all of his savings to start his company called D3O. In 2000, Palmer and a group of hired scientists began to develop a polymer that which held the same name as the company, D3O. They sought out to manufacture a high-performance shock absorption material that had high-flexibility and maintained a good comfort level.
All the sporting goods protective helmets and apparel on the market at the time were bulky, stiff and uncomfortable. Furthermore, if the material suffered from impact it would no longer provide good protection, thus it would need to be replaced. Palmer knew that he would have to make D3O lightweight, breathable, washable and elastic in order to have a competitive edge in the market.
In 2005, Palmer and his team completed development of D3O, a polymer elastomeric foam, constructed of a long chain polymer with offshoots. It is made of intelligent molecules and is thus categorized into smart fabrics and intelligent textiles. The material which is bright orange in color and soft and flexible like putty is completely unique as it is extremely lightweight (as thin as 8mm) and can be molded into countless shapes and sizes depending on its end use. D3O stays soft and flexible with you when you move it in a normal manner, yet when it is introduced to any form of impact the offshoots lock together and become hard within a 1,000th of a second to absorb and spread the force, significantly reducing the effect of impact.
This transformation is possible due to the way these unique molecules move with each other. When the material is being moved at low speed it is soft and flexible, because the bond between the molecules is not that strong, so they can slip past each other. Yet when the material is asked to move quickly by a sudden hard force the molecules re-arrange themselves in a very structured way and create proper hydrogen bonds. So in other words, when you impact the molecules they do not have time to move and they quickly lock into position.
D3O belongs to the family of non-Newtonian fluids, which also includes cornstarch, ketchup and shampoo. What makes a fluid non-Newtonian is its viscosity, which means how they move depending on the forces that they are subjected to. Non-Newtonian fluids can become either more or less solid as they are moved. For example, shampoo and ketchup become less solid when they are rapidly moved (helping them to be squeezed out of a bottle), versus D3O and cornstarch which become more solid as the molecules are moved.
The hardest part of the development per Palmer was making D3O elastic, the product had to be able to bounce back to its original form after an impact. Working with the D3O base material they tried countless elastic polymers, yet none of them wanted to mix with the D3O ”they would just lump together” said Palmer. Finally they found a formula that would work, which is still a company secret. The D3O product officially became commercialized in 2006 and made its debut at the 2006 Winter Olympics as a component used in the Spyder GS race suit made for USA and Canadian ski teams.
Since the D3O is a soft flexible putty it can be molded to add protection to any type of clothing. Currently it is being sewn into motorcycle gear, jeans, ballet pointe shoes, and bicycle helmets that resemble beanie’s. Although the D3O polymer itself is not breathable, it can be produced with perforations thus encouraging airflow. D3O maintains its properties at temperatures ranging from -4 to 122°C. And apparel with D3O inserts can be washed at warm temperatures and air-dried.
In 2009 the Ministery of Defense awarded D3O £100,000 to fit solder helmets to reduce half of the kinetic energy of a bullet or shrapnel. And in May 2011 Kyrano UK a jeans manufacturer released comfortable motorcycle riding jeans that have removable D3O hip and knee body armour.
This new development in textiles will have a huge impact in protective wear and will prevent countless injuries and possibly even deaths. For the future Palmer, who is still the Managing Director of the D3O Lab, hopes to make D3O microbial and abrasion resistant.
Dilatant
A dilatant material is one in which viscosity increases with the rate of shear strain. Such a shear thickening fluid, also known by the acronym STF, is an example of a non-Newtonian fluid....
material commonly used for impact protection. It has been categorized into smart fabrics and intelligent textiles by the Research and Markets.
The material is believed to lead the innovation of smart fabrics in impact protection.
D3O became widely used in impact protection due to its properties. In its raw state it flows freely when moved slowly, but on shock, locks together to absorb and disperse energy, before instantly returning to its flexible state. This characteristic provides protection, as well as material flexibility, which in turn offers many benefits to the wearer.
Energy is distributed throughout the synthetic elastomeric polymer
Polymer
A polymer is a large molecule composed of repeating structural units. These subunits are typically connected by covalent chemical bonds...
and the enhanced chemistry continues to distribute energy on throughout the matrix, reducing the effect of impact.
History
In 1999 Richard Palmer was sitting at a ski lodge in the Alps nursing a bruised knee and thought to himself that there had to be a better, more comfortable way to protect oneself from sporting injuries. “It occurred to me that all the available impact protection systems work on a macro scale, and because of that they are restrictive, uncomfortable and actually pretty ineffective. I knew if I could get a system to work on a molecular level we could have an amazing product”.Immediately after that realization Palmer teamed up with Dr. Phil Green, a fellow co-worker from the University of Hertfordshire’s Research and Development Centre and the two decided that they would make a more versatile and lightweight protection material for the human body.
Palmer was so assured that he was onto something big, he quit his job, sold his home, slept on his friends couch and cashed in on all of his savings to start his company called D3O. In 2000, Palmer and a group of hired scientists began to develop a polymer that which held the same name as the company, D3O. They sought out to manufacture a high-performance shock absorption material that had high-flexibility and maintained a good comfort level.
All the sporting goods protective helmets and apparel on the market at the time were bulky, stiff and uncomfortable. Furthermore, if the material suffered from impact it would no longer provide good protection, thus it would need to be replaced. Palmer knew that he would have to make D3O lightweight, breathable, washable and elastic in order to have a competitive edge in the market.
In 2005, Palmer and his team completed development of D3O, a polymer elastomeric foam, constructed of a long chain polymer with offshoots. It is made of intelligent molecules and is thus categorized into smart fabrics and intelligent textiles. The material which is bright orange in color and soft and flexible like putty is completely unique as it is extremely lightweight (as thin as 8mm) and can be molded into countless shapes and sizes depending on its end use. D3O stays soft and flexible with you when you move it in a normal manner, yet when it is introduced to any form of impact the offshoots lock together and become hard within a 1,000th of a second to absorb and spread the force, significantly reducing the effect of impact.
This transformation is possible due to the way these unique molecules move with each other. When the material is being moved at low speed it is soft and flexible, because the bond between the molecules is not that strong, so they can slip past each other. Yet when the material is asked to move quickly by a sudden hard force the molecules re-arrange themselves in a very structured way and create proper hydrogen bonds. So in other words, when you impact the molecules they do not have time to move and they quickly lock into position.
D3O belongs to the family of non-Newtonian fluids, which also includes cornstarch, ketchup and shampoo. What makes a fluid non-Newtonian is its viscosity, which means how they move depending on the forces that they are subjected to. Non-Newtonian fluids can become either more or less solid as they are moved. For example, shampoo and ketchup become less solid when they are rapidly moved (helping them to be squeezed out of a bottle), versus D3O and cornstarch which become more solid as the molecules are moved.
The hardest part of the development per Palmer was making D3O elastic, the product had to be able to bounce back to its original form after an impact. Working with the D3O base material they tried countless elastic polymers, yet none of them wanted to mix with the D3O ”they would just lump together” said Palmer. Finally they found a formula that would work, which is still a company secret. The D3O product officially became commercialized in 2006 and made its debut at the 2006 Winter Olympics as a component used in the Spyder GS race suit made for USA and Canadian ski teams.
Since the D3O is a soft flexible putty it can be molded to add protection to any type of clothing. Currently it is being sewn into motorcycle gear, jeans, ballet pointe shoes, and bicycle helmets that resemble beanie’s. Although the D3O polymer itself is not breathable, it can be produced with perforations thus encouraging airflow. D3O maintains its properties at temperatures ranging from -4 to 122°C. And apparel with D3O inserts can be washed at warm temperatures and air-dried.
In 2009 the Ministery of Defense awarded D3O £100,000 to fit solder helmets to reduce half of the kinetic energy of a bullet or shrapnel. And in May 2011 Kyrano UK a jeans manufacturer released comfortable motorcycle riding jeans that have removable D3O hip and knee body armour.
This new development in textiles will have a huge impact in protective wear and will prevent countless injuries and possibly even deaths. For the future Palmer, who is still the Managing Director of the D3O Lab, hopes to make D3O microbial and abrasion resistant.
D3O applications
D3O has been applied in the following areas:- Military
- Workwear
- Medical
- Sports, including ski and snowboard, lacrosse, baseball, volleyball, tennis, ballet, boxing, shooting and sailing, mountain biking and cycling, equestrian and water sports
- Motorcycle apparel
- Footwear
- Cases for electronic devices