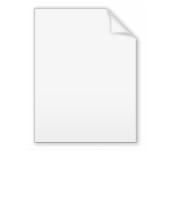
Internal Benchmarking
Encyclopedia
Internal benchmarking is a system where the different locations within an organization that do or produce similar products compare how they are producing the similar outputs. The purpose of this activity is to learn from each other and adapt the best practices at all locations thereby reducing costs and improving quality of the similar products and / or processes. Reference IBM
Technical Report TR02.834 dated March 1979 authored by H. James Harrington
.
, production control, quality engineer, cost accounting
, production
and customer engineering personnel formed a team from all locations that manufactured similar products. This team would meet to review each step in the production process bi-annually. The data at each step in the process was compared to related to:
AS a result of these reviews, agreed-to procedures were established and a centralized location was defined to evaluate any proposed changes to the process that may be suggested between the bi-annual meetings. Usually at these bi-annual meetings a number of good ideas are generated that are assigned to the different locations to evaluate. This led to an ongoing continuous improvement of all the common products at a rate of 10–20% per year.
IBM
International Business Machines Corporation or IBM is an American multinational technology and consulting corporation headquartered in Armonk, New York, United States. IBM manufactures and sells computer hardware and software, and it offers infrastructure, hosting and consulting services in areas...
Technical Report TR02.834 dated March 1979 authored by H. James Harrington
H. James Harrington
H. James Harrington is a American author, engineer, entrepreneur, and consultant in performance improvement. Over his career he has developed many concepts, including poor-quality cost and business process improvement....
.
Benefits
- Decreases the cost of producing the output
- Increases customer satisfaction
- Improves the organization’s reputation
- Improves the quality of your product
- Reduces rework and scrap
- Reduces support cost
- Allows product to be exchanged between locations
Internal benchmarking process
At IBM the product development, manufacturing engineeringManufacturing engineering
Manufacturing engineering is a field dealing with different manufacturing practices and the research and development of processes, machines and equipment.-Overview:...
, production control, quality engineer, cost accounting
Cost accounting
Cost accounting information is designed for managers. Since managers are taking decisions only for their own organization, there is no need for the information to be comparable to similar information from other organizations...
, production
Manufacturing
Manufacturing is the use of machines, tools and labor to produce goods for use or sale. The term may refer to a range of human activity, from handicraft to high tech, but is most commonly applied to industrial production, in which raw materials are transformed into finished goods on a large scale...
and customer engineering personnel formed a team from all locations that manufactured similar products. This team would meet to review each step in the production process bi-annually. The data at each step in the process was compared to related to:
- How the operation was performed
- The equipment that was used
- The cost of the activity
- The time required to do the activity
- The measurements and the distribution of the measurements
- The quality levels
- The interchangeability of the in-process product with the processes at the other location
- The operator instructions
- Review of performance data at the higher levels of assembly and at the customer locations
AS a result of these reviews, agreed-to procedures were established and a centralized location was defined to evaluate any proposed changes to the process that may be suggested between the bi-annual meetings. Usually at these bi-annual meetings a number of good ideas are generated that are assigned to the different locations to evaluate. This led to an ongoing continuous improvement of all the common products at a rate of 10–20% per year.