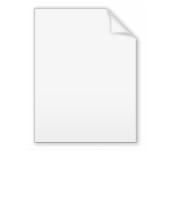
Ishikawa diagram
Encyclopedia
Ishikawa diagrams are causal diagram
s that show the causes of a certain event -- created by Kaoru Ishikawa
(1990). Common uses of the Ishikawa diagram are product design
and quality defect prevention, to identify potential factors causing an overall effect. Each cause or reason for imperfection is a source of variation. Causes are usually grouped into major categories to identify these sources of variation. The categories typically include:
Ishikawa diagrams were proposed by Kaoru Ishikawa
in the 1960s, who pioneered quality management processes in the Kawasaki
shipyards, and in the process became one of the founding father of modern management.
It was first used in the 1940s, and is considered one of the seven basic tools of quality control
. It is known as a fishbone diagram because of its shape, similar to the side view of a fish skeleton.
Mazda
Motors famously used an Ishikawa diagram in the development of the Miata sports car, where the required result was "Jinba Ittai" (Horse and Rider as One — jap. 人馬一体). The main causes included such aspects as "touch" and "braking" with the lesser causes including highly granular factors such as "50/50 weight distribution" and "able to rest elbow on top of driver's door". Every factor identified in the diagram was included in the final design.
Causes can be derived from brainstorming sessions. These groups can then be labeled as categories of the fishbone. They will typically be one of the traditional categories mentioned above but may be something unique to the application in a specific case. Causes can be traced back to root causes with the 5 Whys
technique.
Typical categories are:
– Was the document properly interpreted?
– Was the information properly circulated to all the functions?
– Did the recipient understand the information?
– Was the proper training to perform the task administered to the person?
– Was too much judgment required to perform the task?
– Were guidelines for judgment available?
– Did the environment influence the actions of the individual?
– Are there distractions in the workplace?
– Is fatigue a mitigating factor?
- Is his work efficiency acceptable?
- Is he responsible/accountable?
- Is he qualified?
- Is he experienced?
- Is he medically fit and healthy?
– How much experience does the individual have in performing this task?
- can he carry out the operation without error?
Machines
– Was the correct tool/tooling used?
- Does it meet production requirements?
- Does it meet process capabilities?
– Are files saved with the correct extension to the correct location?
– Is the equipment affected by the environment?
– Is the equipment being properly maintained (i.e., daily/weekly/monthly
preventative maintenance schedule)
– Does the software or hardware need to be updated?
– Does the equipment or software have the features to support our
needs/usage?
- Was the machine properly maintained?
– Was the machine properly programmed?
– Is the tooling/fixturing adequate for the job?
– Does the machine have an adequate guard?
– Was the equipment used within its capabilities and limitations?
– Are all controls including emergency stop button clearly labeled and/or
color coded or size differentiated?
– Is the equipment the right application for the given job?
Measurement
– Does the gauge have a valid calibration date?
– Was the proper gauge used to measure the part, process, chemical,
compound, etc.?
– Was a gauge capability study ever performed?
- Do measurements vary significantly from operator to operator?
- Do operators have a tough time using the prescribed gauge?
- Is the gauge fixturing adequate?
– Does the gauge have proper measurement resolution?
– Did the environment influence the measurements taken?
Material (Includes Raw Material, Consumables and Information )
– Is all needed information available and accurate?
– Can information be verified or cross-checked?
– Has any information changed recently / do we have a way of keeping the
information up to date?
– What happens if we don't have all of the information we need?
– Is a Material Safety Data Sheet
(MSDS) readily available?
– Was the material properly tested?
– Was the material substituted?
– Is the supplier’s process defined and controlled?
- Was the raw material defective?
- was the raw material the wrong type for the job?
– Were quality requirements adequate for the part's function?
– Was the material contaminated?
– Was the material handled properly (stored, dispensed, used & disposed)?
Method
– Was the canister, barrel, etc. labeled properly?
– Were the workers trained properly in the procedure?
– Was the testing performed statistically significant?
– Was data tested for true root cause?
– How many “if necessary” and “approximately” phrases are found in this
process?
– Was this a process generated by an Integrated Product Development (IPD)
Team?
– Did the IPD Team employ Design for Environmental (DFE) principles?
– Has a capability study ever been performed for this process?
– Is the process under Statistical Process Control
(SPC)?
– Are the work instructions clearly written?
– Are mistake-proofing devices/techniques employed?
– Are the work instructions complete?
- Is the work standard upgraded and to current revision?
– Is the tooling adequately designed and controlled?
– Is handling/packaging adequately specified?
– Was the process changed?
– Was the design changed?
- Are the lighting and ventilation adequate?
– Was a process Failure Modes Effects Analysis (FMEA) ever performed?
– Was adequate sampling done?
– Are features of the process critical to safety clearly spelled out to the
Operator?
Environment
– Is the process affected by temperature changes over the course of a day?
– Is the process affected by humidity, vibration, noise, lighting, etc.?
– Does the process run in a controlled environment?
– Are associates distracted by noise, uncomfortable temperatures,
fluorescent lighting, etc.?
Management
- Is management involvement seen?
– Inattention to task
– Task hazards not guarded properly
– Other (horseplay, inattention....)
– Stress demands
– Lack of Process
– Training or education lacking
– Poor employee involvement
– Poor recognition of hazard
– Previously identified hazards were not eliminated
Causal diagram
A causal diagram is a graphical tool that enables the visualisation of causal relationships between variables in a causal model. A typical causal diagram will comprise a set of variables defined as being within the scope of the model being represented...
s that show the causes of a certain event -- created by Kaoru Ishikawa
Kaoru Ishikawa
was a Japanese university professor and influential quality management innovator best known in North America for the Ishikawa or cause and effect diagram that is used in the analysis of industrial process.- Biography :...
(1990). Common uses of the Ishikawa diagram are product design
Product design
-Introduction:Product design is the process of creating a new product to be sold by a business or enterprise to its customers. It is concerned with the efficient and effective generation and development of ideas through a process that leads to new products.Product designers conceptualize and...
and quality defect prevention, to identify potential factors causing an overall effect. Each cause or reason for imperfection is a source of variation. Causes are usually grouped into major categories to identify these sources of variation. The categories typically include:
- People: Anyone involved with the process
- Methods: How the process is performed and the specific requirements for doing it, such as policies, procedures, rules, regulations and laws
- Machines: Any equipment, computers, tools etc. required to accomplish the job
- Materials: Raw materials, parts, pens, paper, etc. used to produce the final product
- Measurements: Data generated from the process that are used to evaluate its quality
- Environment: The conditions, such as location, time, temperature, and culture in which the process operates
Overview
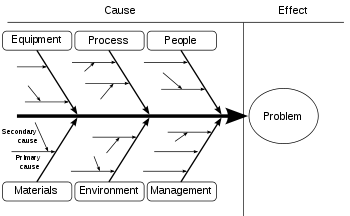
Kaoru Ishikawa
was a Japanese university professor and influential quality management innovator best known in North America for the Ishikawa or cause and effect diagram that is used in the analysis of industrial process.- Biography :...
in the 1960s, who pioneered quality management processes in the Kawasaki
Kawasaki Heavy Industries
is an international corporation based in Japan. It has headquarters in both Chūō-ku, Kobe and Minato, Tokyo.The company is named after its founder Shōzō Kawasaki and has no connection with the city of Kawasaki, Kanagawa....
shipyards, and in the process became one of the founding father of modern management.
It was first used in the 1940s, and is considered one of the seven basic tools of quality control
Quality control
Quality control, or QC for short, is a process by which entities review the quality of all factors involved in production. This approach places an emphasis on three aspects:...
. It is known as a fishbone diagram because of its shape, similar to the side view of a fish skeleton.
Mazda
Mazda
is a Japanese automotive manufacturer based in Fuchū, Aki District, Hiroshima Prefecture, Japan.In 2007, Mazda produced almost 1.3 million vehicles for global sales...
Motors famously used an Ishikawa diagram in the development of the Miata sports car, where the required result was "Jinba Ittai" (Horse and Rider as One — jap. 人馬一体). The main causes included such aspects as "touch" and "braking" with the lesser causes including highly granular factors such as "50/50 weight distribution" and "able to rest elbow on top of driver's door". Every factor identified in the diagram was included in the final design.
Causes
Causes in the diagram are often categorized, such as to the 8 M's, described below. Cause-and-effect diagrams can reveal key relationships among various variables, and the possible causes provide additional insight into process behavior.Causes can be derived from brainstorming sessions. These groups can then be labeled as categories of the fishbone. They will typically be one of the traditional categories mentioned above but may be something unique to the application in a specific case. Causes can be traced back to root causes with the 5 Whys
5 Whys
The 5 Whys is a questions-asking method used to explore the cause/effect relationships underlying a particular problem. Ultimately, the goal of applying the 5 Whys method is to determine a root cause of a defect or problem.- Example :...
technique.
Typical categories are:
The 8 Ms (used in manufacturing)
- Machine (technology)
- Method (process)
- Material (Includes Raw Material, Consumables and Information.)
- Man Power (physical work)/Mind Power (brain work): KaizenKaizen, Japanese for "improvement", or "change for the better" refers to philosophy or practices that focus upon continuous improvement of processes in manufacturing, engineering, game development, and business management. It has been applied in healthcare, psychotherapy, life-coaching, government,...
s, Suggestions - Measurement (Inspection)
- Milieu/Mother Nature (Environment)
- Management/Money Power
- Maintenance
The 8 Ps (used in service industry)
- Product=Service
- Price
- Place
- Promotion/Entertainment
- People(key person)
- Process
- Physical Evidence
- Productivity & Quality
Questions to be asked while building a Fishbone Diagram
Man/Operator– Was the document properly interpreted?
– Was the information properly circulated to all the functions?
– Did the recipient understand the information?
– Was the proper training to perform the task administered to the person?
– Was too much judgment required to perform the task?
– Were guidelines for judgment available?
– Did the environment influence the actions of the individual?
– Are there distractions in the workplace?
– Is fatigue a mitigating factor?
- Is his work efficiency acceptable?
- Is he responsible/accountable?
- Is he qualified?
- Is he experienced?
- Is he medically fit and healthy?
– How much experience does the individual have in performing this task?
- can he carry out the operation without error?
Machines
– Was the correct tool/tooling used?
- Does it meet production requirements?
- Does it meet process capabilities?
– Are files saved with the correct extension to the correct location?
– Is the equipment affected by the environment?
– Is the equipment being properly maintained (i.e., daily/weekly/monthly
preventative maintenance schedule)
– Does the software or hardware need to be updated?
– Does the equipment or software have the features to support our
needs/usage?
- Was the machine properly maintained?
– Was the machine properly programmed?
– Is the tooling/fixturing adequate for the job?
– Does the machine have an adequate guard?
– Was the equipment used within its capabilities and limitations?
– Are all controls including emergency stop button clearly labeled and/or
color coded or size differentiated?
– Is the equipment the right application for the given job?
Measurement
– Does the gauge have a valid calibration date?
– Was the proper gauge used to measure the part, process, chemical,
compound, etc.?
– Was a gauge capability study ever performed?
- Do measurements vary significantly from operator to operator?
- Do operators have a tough time using the prescribed gauge?
- Is the gauge fixturing adequate?
– Does the gauge have proper measurement resolution?
– Did the environment influence the measurements taken?
Material (Includes Raw Material, Consumables and Information )
– Is all needed information available and accurate?
– Can information be verified or cross-checked?
– Has any information changed recently / do we have a way of keeping the
information up to date?
– What happens if we don't have all of the information we need?
– Is a Material Safety Data Sheet
Material safety data sheet
A Material Safety Data Sheet is a form with data regarding the properties of a particular substance....
(MSDS) readily available?
– Was the material properly tested?
– Was the material substituted?
– Is the supplier’s process defined and controlled?
- Was the raw material defective?
- was the raw material the wrong type for the job?
– Were quality requirements adequate for the part's function?
– Was the material contaminated?
– Was the material handled properly (stored, dispensed, used & disposed)?
Method
– Was the canister, barrel, etc. labeled properly?
– Were the workers trained properly in the procedure?
– Was the testing performed statistically significant?
– Was data tested for true root cause?
– How many “if necessary” and “approximately” phrases are found in this
process?
– Was this a process generated by an Integrated Product Development (IPD)
Team?
– Did the IPD Team employ Design for Environmental (DFE) principles?
– Has a capability study ever been performed for this process?
– Is the process under Statistical Process Control
Statistical process control
Statistical process control is the application of statistical methods to the monitoring and control of a process to ensure that it operates at its full potential to produce conforming product. Under SPC, a process behaves predictably to produce as much conforming product as possible with the least...
(SPC)?
– Are the work instructions clearly written?
– Are mistake-proofing devices/techniques employed?
– Are the work instructions complete?
- Is the work standard upgraded and to current revision?
– Is the tooling adequately designed and controlled?
– Is handling/packaging adequately specified?
– Was the process changed?
– Was the design changed?
- Are the lighting and ventilation adequate?
– Was a process Failure Modes Effects Analysis (FMEA) ever performed?
– Was adequate sampling done?
– Are features of the process critical to safety clearly spelled out to the
Operator?
Environment
– Is the process affected by temperature changes over the course of a day?
– Is the process affected by humidity, vibration, noise, lighting, etc.?
– Does the process run in a controlled environment?
– Are associates distracted by noise, uncomfortable temperatures,
fluorescent lighting, etc.?
Management
- Is management involvement seen?
– Inattention to task
– Task hazards not guarded properly
– Other (horseplay, inattention....)
– Stress demands
– Lack of Process
– Training or education lacking
– Poor employee involvement
– Poor recognition of hazard
– Previously identified hazards were not eliminated
Criticism
In a discussion of the nature of a cause it is customary to distinguish between necessary and sufficient conditions for the occurrence of an event. A necessary condition for the occurrence of a specified event is a circumstance in whose absence the event cannot occur. A sufficient condition for the occurrence of an event is a circumstance in whose presence the event must occur. A sufficient condition naturally contains one or several necessary ones. Ishikawa diagrams are meant to use the necessary conditions and split the "sufficient" ones into the "necessary" parts. Some critics failing this simple logic have asked which conditions (necessary or sufficient) are addressed by the diagram in caseFurther reading
- Ishikawa, Kaoru (1990); (Translator: J. H. Loftus); Introduction to Quality Control; 448 p; ISBN 4-906224-61-X
- Dale, Barrie G. et al. (2007); Managing Quality 5th ed; ISBN 978-1-4051-4279-3