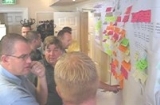
Lean construction
Encyclopedia
Lean Construction is a combination of original research and development in design and construction with an adaption of lean manufacturing
principles and practices to the end-to-end design and construction process. Unlike manufacturing, construction is a project based-production process. Lean construction is concerned with the holistic pursuit of concurrent and continuous improvements in all dimensions of the built and natural environment: design, construction, activation, maintenance, salvaging, and recycling (Abdelhamid 2007). This approach tries to manage and improve construction processes with minimum cost and maximum value by considering customer needs. (Koskela et al. 2002)
The term "Lean Construction" was coined by the International Group for Lean Construction in its first meeting in 1993. (Gleeson et al. 2007)
Evidence from research and observations indicated that the conceptual models of Construction Management and the tools it utilizes (work breakdown structure
, critical path method
, and earned value management
) fail to deliver projects ‘on-time, at budget, and at desired quality’ (Abdelhamid 2004). With recurring negative experiences on projects, evidenced by endemic quality problems and rising litigation, it became evident that the governing principles of construction management needed revisiting. In fact, respondents to the 6th annual Survey of Construction Owners by CMAA (2006) included a comment: "While the cost of steel and cement are making headlines, the less publicized failures in the management of construction projects can be disastrous. Listen carefully to the message in this comment. We are not talking about just materials, methods, equipment, or contract documents. We are talking about how we work to deliver successful capital projects and how we manage the costs of inefficiency."
to develop a more overarching production management paradigm for project-based production systems where production is conceptualized in three complementary ways, namely, as a Transformation (T), as a Flow(F), and as Value generation(V). Koskela and Howell (2002) have also presented a comprehensive review of the shortcomings existing management theory – specifically as related to the planning, execution, and control paradigms – in project-based production systems. Both conceptualizations provide a solid intellectual foundation of Lean Construction as evident from both research and practice (Abdelhamid 2004).
Recognizing that construction sites reflect prototypical behavior of complex and chaotic systems, especially in the flow of both material and information on and off site, Bertelsen (2003a and 2003b) suggested that construction should be modeled using chaos and complex systems theory. Bertelsen (2003b) specifically argues that construction could and should be understood in three complimentary ways, namely, as a project-based production process, as an industry that provides autonomous agents, and as a social system. With more developments in this line of thinking, it is very likely that the Lean Construction governing paradigm will change to it. And so, the process will keep on repeating!
Lean Construction recognizes that desired ends affect the means to achieve these ends, and that available means will affect realized ends (Lichtig 2004). Essentially, Lean construction aims to embody the benefits of the Master Builder concept (Abdelhamid et al. 2008).
Lean construction supplements traditional construction management approaches with (Abdelhamid 2007): (1) two critical and necessary dimensions for successful capital project delivery by requiring the deliberate consideration of material and information flow and value generation in a production system; and (2) different project and production management (planning-execution-control) paradigms.
While lean construction is identical to Lean Production in spirit, it is different in how it was conceived as well how it is practiced.
The common spirit flows from shared principles:
The differences in detail flow from a recognition that construction is a project based production where the product is generally a prototype.
As Sowards stated (2004) the priority for all construction work is to:
While Lean Construction’s main tool for making design and construction processes more predictable is the Last Planner System® (see below) and derivatives of it, other lean tools already proven in manufacturing have been adapted to the construction industry with equal success. These include: 5S, Kanban
, Kaizen
events, quick setup/changeover, Poka Yoke, Visual Control and Five Whys (Mastroianni and Abdelhamid 2003, Salem et al. 2005).
In lean design set based design, design structure matrices and target value design strategies are proving valuable.
"One can think of Lean Construction in a way similar to mesoeconomics
. Lean Construction draws upon the principles of project-level management and upon the principles that govern production-level management. Lean Construction recognizes that any successful project undertaking will inevitably involve the interaction between project and production management." (Abdelhamid 2007)
----
[IPD is a clever solution to the tough organizational and contracting problems faced in today’s market. It relies on careful participant selection, transparency and continuing dialog. Construction consumers might consider rethinking their contracting strategies to share more fully in the benefits.](Matthews and Howell 2005)
[IPD is a Relational Contracting approach that aligns project objectives with the interests of key participants. It creates an organization able to apply the principles and practices of the Lean Project Delivery System.] (Matthews and Howell 2005)
Company', in other business sectors they are called an 'Extended Lean Enterprise'.
The UK 'Building Down Barriers Handbook of Supply Chain Management-The Essentials' states that: 'The commercial core of supply chain management is setting up long-term relationships based on improving the value of what the supply chain delivers, improving quality and reducing underlying costs through taking out waste and inefficiency. This is the opposite of 'business as usual' in the construction sector, where people do things on project after project in the same old inefficient ways, forcing each other to give up profits and overhead recovery in order to deliver at what seems the market price. What results is a fight over who keeps any of the meagre margins that result from each project, or attempts to recoup 'negative margins' through 'claims', The last thing that receives time or energy in this desperate, project-by-project gladiatorial battle for survival is consideration of how to reduce underlying costs or improve quality'.
LPS begins with collaborative scheduling/programming engaging the main project suppliers from the start. Risk analysis ensures that float is built in where it will best protect programme integrity and predictability. Where appropriate the process can be used for programme compression too. In this way, one constructor took 6 weeks out of an 18-week programme for the construction of a 40 bed hotel. Benefits to the client are enormous.
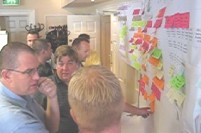
Figure 1: intense discussion during a programme compression workshop
Before work starts, team leaders make tasks ready so that when work should be done, it can be. Why put work into production if a pre-requisite is missing? This MakeReady process continues throughout the project.
Figure 2: part of a MakeReady form for documenting the process of making tasks ready (this one for use in design)
There is a weekly work planning (WWP) meeting involving all the last planners – design team leaders and/or trade supervisors on site. It is in everyone’s interest to explore inter-dependencies between tasks and prevent colleagues from over-committing.

Figure 3: part of a Weekly Work Plan form used by trade foremen on site or design team leaders to prepare for the WWP meeting.
This weekly work planning processes is built around promises. The agreed programme defines when tasks should be done and acts as a request to the supplier to do that task. The last planners (that is the trade foremen on site or design team leaders in a design process) only promise once they have clarified the conditions of satisfaction and are clear that the task can be done.
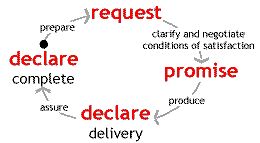
Figure 4: the promise cycle (after Fernando Flores
)
Once the task is complete the last planner responsible declares completion so that site management or the next trade can assure themselves that it is complete to an appropriate standard.
A key measure of the success of the Last Planner system is PPC. This measures the Percentage of Promises Completed on time. As PPC increases. project productivity and profitability increase, with step changes at around 70% and 85%. This score is measured site-wide and displayed around the site. Weekly measures are used by the project and by individual suppliers as the basis for learning how to improve the predictability of the work programme and hence the PPC scores.
A key part of the continual improvement process is a study of the reasons why tasks promised in the WWP are delivered late. The following chart shows typical reasons:
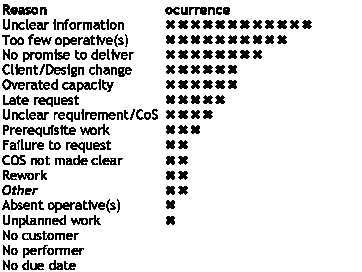
Figure 5: example of a reasons Pareto chart
Recording the reasons in a Pareto chart like the one above makes it easy to see where attention is most likely to yield the most results. Using tools like 5 Why analysis and cause-effect diagrams will help the team understand how they can improve the clarity of information and ensure that there are sufficient operatives.
Last Planner® benefits don’t stop at project predictability, profit and productivity; it contributes to positive changes in other industry KPIs. Danish research shows almost half the accidents and up to 70% less sickness absence on LPS® managed sites.
The Lean Construction Institute developed the Last Planner System®, and allows owners, clients or their construction companies to use is to improve their design and construction performance. LCI makes no charge for this and places no limits on its use within a company. LCI encourages companies that find it useful to become contributors to the Lean Construction Institute.
LCI retains a registered Trademark on the term and Copyright in the idea and materials to prevent people who misunderstand or misrepresent the system from using it in trade. Consulting companies or individuals wishing to use the Last Planner™ System in trade (commercial offering of service) must first be approved by LCI. Consultants are expected to make financial and other contributions to LCI in recognition of the work and effort LCI put into developing Last Planner®.
Last Planner System® development continues under the direction of Lean Construction Institute Directors Professor Glenn Ballard and Greg Howell with support from users around the world. For more information about the development process see Ballard (1994, 2000) and Ballard & Howell (2004) for example.
For a more detailed description and list of benefits see here
For more on Learning how to implement Last Planner® see here
1. What is Lean Construction?
2. Is Lean Construction just applying Lean Production in construction?
3. When did Lean Construction begin?
4. What are the major differences between a project run based on Lean Construction and one that is not?
5. Building Information Modeling (BIM) aims to build a collaborative relation between designers and constructors, so how is that different from LC?
6. Is Lean Construction like Leadership in Energy & Environmental Design (LEED) where you have to commit to a certain level of compliance and the project is checked against that?
7. What percentage of the US construction industry is adopting it?
8. Is Lean Construction accepted more in other countries than in the US?
9. What is the primary difference between Lean Production and Lean Construction?
10. Can the concept of Heijunka be used in construction? Why?
11. Contrast “lean work structuring” with “work breakdown structure”.
12. What are the differences between project control and production control?
13. Is Value Stream Mapping (VSM) a tool for construction?
14. Is Integrated Project Delivery the same as Lean Construction?
[IPD is a registered business mark by Lean Construction Institute with the US PTO - Class 37; Registration # 2,971,009]
These papers will be helpful to explain IPD and IFoA http://www.leanconstruction.org/lcj/V2_N1/LCJ_05_003.pdf and http://www.leanconstruction.org/lcj/V2_N1/LCJ_05_008.pdf
for discussions of Alliancing, PPC2000 and IFoA please see http://www.lean-in-public.org/lips_en_proceedings.html
Lean manufacturing
Lean manufacturing, lean enterprise, or lean production, often simply, "Lean," is a production practice that considers the expenditure of resources for any goal other than the creation of value for the end customer to be wasteful, and thus a target for elimination...
principles and practices to the end-to-end design and construction process. Unlike manufacturing, construction is a project based-production process. Lean construction is concerned with the holistic pursuit of concurrent and continuous improvements in all dimensions of the built and natural environment: design, construction, activation, maintenance, salvaging, and recycling (Abdelhamid 2007). This approach tries to manage and improve construction processes with minimum cost and maximum value by considering customer needs. (Koskela et al. 2002)
The term "Lean Construction" was coined by the International Group for Lean Construction in its first meeting in 1993. (Gleeson et al. 2007)
Historical Development
The seminal work of Lauri Koskela in 1992 challenged the Construction Management community to consider the inadequacies of the time-cost-quality tradeoff paradigm. Another paradigm-breaking anomaly was that observed by Ballard (1994), Ballard and Howell (1994a and 1994b), Howell and Ballard (1994a and 1994b) and Howell (1998). Analysis of project plan failures indicated that “normally only about 50% of the tasks on weekly work plans are completed by the end of the plan week” and that constructors could mitigate most of the problems through “active management of variability, starting with the structuring of the project (temporary production system) and continuing through its operation and improvement.” (Ballard and Howell 2003).Evidence from research and observations indicated that the conceptual models of Construction Management and the tools it utilizes (work breakdown structure
Work breakdown structure
A work breakdown structure , in project management and systems engineering, is a deliverable oriented decomposition of a project into smaller components. It defines and groups a project's discrete work elements in a way that helps organize and define the total work scope of the project.A work...
, critical path method
Critical path method
The critical path method is an algorithm for scheduling a set of project activities. It is an important tool for effective project management.-History:...
, and earned value management
Earned value management
Earned value management is a project management technique for measuring project performance and progress in an objective manner. EVM has the ability to combine measurements of scope, schedule, and cost in a single integrated system. Earned Value Management is notable for its ability to provide...
) fail to deliver projects ‘on-time, at budget, and at desired quality’ (Abdelhamid 2004). With recurring negative experiences on projects, evidenced by endemic quality problems and rising litigation, it became evident that the governing principles of construction management needed revisiting. In fact, respondents to the 6th annual Survey of Construction Owners by CMAA (2006) included a comment: "While the cost of steel and cement are making headlines, the less publicized failures in the management of construction projects can be disastrous. Listen carefully to the message in this comment. We are not talking about just materials, methods, equipment, or contract documents. We are talking about how we work to deliver successful capital projects and how we manage the costs of inefficiency."
A New Paradigm
Koskela (2000) argued that the mismatch between the conceptual models and observed reality underscored the lack of robustness in the existing constructs and signaled the need for a theory of production in construction. Koskela then used the ideal production system embodied in the Toyota Production SystemToyota Production System
The Toyota Production System is an integrated socio-technical system, developed by Toyota, that comprises its management philosophy and practices. The TPS organizes manufacturing and logistics for the automobile manufacturer, including interaction with suppliers and customers...
to develop a more overarching production management paradigm for project-based production systems where production is conceptualized in three complementary ways, namely, as a Transformation (T), as a Flow(F), and as Value generation(V). Koskela and Howell (2002) have also presented a comprehensive review of the shortcomings existing management theory – specifically as related to the planning, execution, and control paradigms – in project-based production systems. Both conceptualizations provide a solid intellectual foundation of Lean Construction as evident from both research and practice (Abdelhamid 2004).
Recognizing that construction sites reflect prototypical behavior of complex and chaotic systems, especially in the flow of both material and information on and off site, Bertelsen (2003a and 2003b) suggested that construction should be modeled using chaos and complex systems theory. Bertelsen (2003b) specifically argues that construction could and should be understood in three complimentary ways, namely, as a project-based production process, as an industry that provides autonomous agents, and as a social system. With more developments in this line of thinking, it is very likely that the Lean Construction governing paradigm will change to it. And so, the process will keep on repeating!
What is lean construction?
Lean construction is a “way to design production systems to minimize waste of materials, time, and effort in order to generate the maximum possible amount of value (Koskela et al. 2002) ”. Designing a production system to achieve the stated ends is only possible through the collaboration of all project participants (Owner, A/E, Constructors, Facility Managers, End-user) at early stages of the project. This goes beyond the contractual arrangement of design/build or constructability reviews where constructors, and sometime facility managers, merely react to designs instead of informing and influencing the design (Abdelhamid et al. 2008).Lean Construction recognizes that desired ends affect the means to achieve these ends, and that available means will affect realized ends (Lichtig 2004). Essentially, Lean construction aims to embody the benefits of the Master Builder concept (Abdelhamid et al. 2008).
Lean construction supplements traditional construction management approaches with (Abdelhamid 2007): (1) two critical and necessary dimensions for successful capital project delivery by requiring the deliberate consideration of material and information flow and value generation in a production system; and (2) different project and production management (planning-execution-control) paradigms.
While lean construction is identical to Lean Production in spirit, it is different in how it was conceived as well how it is practiced.
The common spirit flows from shared principles:
-
- Whole System Optimisation through Collaboration and systematic learning
- continual improvement/pursuit of perfection involving everyone in the system
- a focus on delivering the value desired by the owner/client/end-user
- allowing value to flow by systematically eliminating obstacles to value creation and those parts of the process that create no value
- creating pull production
The differences in detail flow from a recognition that construction is a project based production where the product is generally a prototype.
As Sowards stated (2004) the priority for all construction work is to:
- keep work flowing so that the crews are always productive installing product;
- reduce inventory of material and tools and
- reduce costs.
While Lean Construction’s main tool for making design and construction processes more predictable is the Last Planner System® (see below) and derivatives of it, other lean tools already proven in manufacturing have been adapted to the construction industry with equal success. These include: 5S, Kanban
Kanban
, also spelled kamban, and literally meaning "signboard" or "billboard", is a concept related to lean and just-in-time production. According to Taiichi Ohno, the man credited with developing Just-in-time, kanban is one means through which JIT is achieved.Kanban is not an inventory control system...
, Kaizen
Kaizen
, Japanese for "improvement", or "change for the better" refers to philosophy or practices that focus upon continuous improvement of processes in manufacturing, engineering, game development, and business management. It has been applied in healthcare, psychotherapy, life-coaching, government,...
events, quick setup/changeover, Poka Yoke, Visual Control and Five Whys (Mastroianni and Abdelhamid 2003, Salem et al. 2005).
In lean design set based design, design structure matrices and target value design strategies are proving valuable.
"One can think of Lean Construction in a way similar to mesoeconomics
Mesoeconomics
Mesoeconomics is a neologism used to describe the study of economic arrangements which are not based either on the microeconomics of buying and selling and supply and demand, nor on the macroeconomic reasoning of aggregate totals of demand, but on the importance of under what structures these...
. Lean Construction draws upon the principles of project-level management and upon the principles that govern production-level management. Lean Construction recognizes that any successful project undertaking will inevitably involve the interaction between project and production management." (Abdelhamid 2007)
----
Integrated Project Delivery
Integrated Project Delivery (IPD) - a registered business mark by Lean Construction Institute with the US PTO - is a delivery system that seek to align interests, objectives and practices, even in a single business, through a team-based approach. The team primary Team Members would include the Architect, key technical consultants as well as a general contractor and key subcontractors.[IPD is a clever solution to the tough organizational and contracting problems faced in today’s market. It relies on careful participant selection, transparency and continuing dialog. Construction consumers might consider rethinking their contracting strategies to share more fully in the benefits.](Matthews and Howell 2005)
[IPD is a Relational Contracting approach that aligns project objectives with the interests of key participants. It creates an organization able to apply the principles and practices of the Lean Project Delivery System.] (Matthews and Howell 2005)
Practical applications
In the UK, a major R&D project, Building Down Barriers, was launched in 1997 to adapt the Toyota Production System for use in the construction sector. The resulting supply chain management toolset was tested and refined on two pilot projects and the comprehensive and detailed process-based toolset was published in 2000 as the 'Building Down Barriers Handbook of Supply Chain Management-The Essentials'. The project demonstrated very clearly that lean thinking would only deliver major performance improvements if the construction sector learned from the extensive experience of other business sectors. Lean thinking must become the way that all the firms in the design and construction supply chain co-operate with each other at a strategic level that over-arches individual projects. In the aerospace sector, these long-term supply-side relationships are called a 'VirtualVirtual
The term virtual is a concept applied in many fields with somewhat differing connotations, and also, differing denotations.The term has been defined in philosophy as "that which is not real" but may display the salient qualities of the real....
Company', in other business sectors they are called an 'Extended Lean Enterprise'.
The UK 'Building Down Barriers Handbook of Supply Chain Management-The Essentials' states that: 'The commercial core of supply chain management is setting up long-term relationships based on improving the value of what the supply chain delivers, improving quality and reducing underlying costs through taking out waste and inefficiency. This is the opposite of 'business as usual' in the construction sector, where people do things on project after project in the same old inefficient ways, forcing each other to give up profits and overhead recovery in order to deliver at what seems the market price. What results is a fight over who keeps any of the meagre margins that result from each project, or attempts to recoup 'negative margins' through 'claims', The last thing that receives time or energy in this desperate, project-by-project gladiatorial battle for survival is consideration of how to reduce underlying costs or improve quality'.
Last Planner System®
The Last Planner System® (LPS) improves both design and construction schedule/programme predictability – work completed as and when promised. It is a system of inter-related elements – full benefits come when all are implemented together, over time. Based on simple paper forms, it can be administered using Post-it notes, paper, pencil, eraser and photocopier. A spreadsheet can help.LPS begins with collaborative scheduling/programming engaging the main project suppliers from the start. Risk analysis ensures that float is built in where it will best protect programme integrity and predictability. Where appropriate the process can be used for programme compression too. In this way, one constructor took 6 weeks out of an 18-week programme for the construction of a 40 bed hotel. Benefits to the client are enormous.
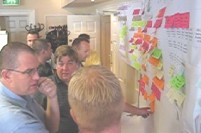
Figure 1: intense discussion during a programme compression workshop
Before work starts, team leaders make tasks ready so that when work should be done, it can be. Why put work into production if a pre-requisite is missing? This MakeReady process continues throughout the project.

Figure 2: part of a MakeReady form for documenting the process of making tasks ready (this one for use in design)
There is a weekly work planning (WWP) meeting involving all the last planners – design team leaders and/or trade supervisors on site. It is in everyone’s interest to explore inter-dependencies between tasks and prevent colleagues from over-committing.

Figure 3: part of a Weekly Work Plan form used by trade foremen on site or design team leaders to prepare for the WWP meeting.
This weekly work planning processes is built around promises. The agreed programme defines when tasks should be done and acts as a request to the supplier to do that task. The last planners (that is the trade foremen on site or design team leaders in a design process) only promise once they have clarified the conditions of satisfaction and are clear that the task can be done.
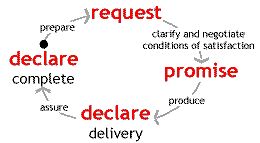
Figure 4: the promise cycle (after Fernando Flores
Fernando Flores
Carlos Fernando Flores Labra is a Chilean engineer, entrepreneur and politician. He is a former cabinet minister of president Salvador Allende and was senator for the Arica and Parinacota and Tarapacá regions between 2001 and 2009...
)
Once the task is complete the last planner responsible declares completion so that site management or the next trade can assure themselves that it is complete to an appropriate standard.
A key measure of the success of the Last Planner system is PPC. This measures the Percentage of Promises Completed on time. As PPC increases. project productivity and profitability increase, with step changes at around 70% and 85%. This score is measured site-wide and displayed around the site. Weekly measures are used by the project and by individual suppliers as the basis for learning how to improve the predictability of the work programme and hence the PPC scores.
A key part of the continual improvement process is a study of the reasons why tasks promised in the WWP are delivered late. The following chart shows typical reasons:
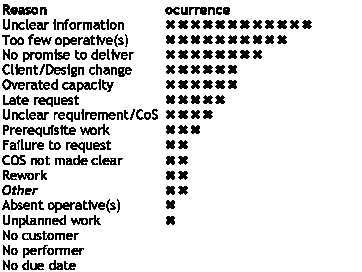
Figure 5: example of a reasons Pareto chart
Recording the reasons in a Pareto chart like the one above makes it easy to see where attention is most likely to yield the most results. Using tools like 5 Why analysis and cause-effect diagrams will help the team understand how they can improve the clarity of information and ensure that there are sufficient operatives.
Last Planner® benefits don’t stop at project predictability, profit and productivity; it contributes to positive changes in other industry KPIs. Danish research shows almost half the accidents and up to 70% less sickness absence on LPS® managed sites.
The Lean Construction Institute developed the Last Planner System®, and allows owners, clients or their construction companies to use is to improve their design and construction performance. LCI makes no charge for this and places no limits on its use within a company. LCI encourages companies that find it useful to become contributors to the Lean Construction Institute.
LCI retains a registered Trademark on the term and Copyright in the idea and materials to prevent people who misunderstand or misrepresent the system from using it in trade. Consulting companies or individuals wishing to use the Last Planner™ System in trade (commercial offering of service) must first be approved by LCI. Consultants are expected to make financial and other contributions to LCI in recognition of the work and effort LCI put into developing Last Planner®.
Last Planner System® development continues under the direction of Lean Construction Institute Directors Professor Glenn Ballard and Greg Howell with support from users around the world. For more information about the development process see Ballard (1994, 2000) and Ballard & Howell (2004) for example.
For a more detailed description and list of benefits see here
For more on Learning how to implement Last Planner® see here
Differences between Lean Construction approach and Project Management Institute (PMI) approach
The differences between lean approach and PMI approach are listed below:- Managing the interaction between activities and combined effects of dependence and variation, is a first concern in lean construction because their interactions highly affects the time and cost of projects(Howell,1999);in comparison, these interactions are not considered in PMI.
- In lean construction optimization efforts focus on making work flow reliable (Ballard, LPDS,2000 ); in contrast PMI focuses on improving productivity of each activity which can make errors and reducing quality and result in rework.
- The project is structured and managed as a value generating process (value is defined as satisfying customer requirements) (Howell, 1999), while PMI considers less cost as value.
- In lean approach, downstream stakeholders are involved in front end planning and design through cross functional teams (Ballard, LPDS, 2000); on the other hand PMI doesn’t consider this issue.
- In lean construction, project control has the job of execution (Ballard, PhD thesis, 2000); whereas, control in PMI method relies on variance detection after-the-fact.
- In lean method, pull techniques are used to govern the flow of materials and information through networks of cooperating specialists (Ballard, PhD thesis, 2000); in contrast, PMI uses push techniques for releasing the information and materials.
- Capacity and inventory buffers are used to absorb variation(Mura). Feedback loops are included at every level, to make rapid system adjustments, (Ballard, PhD thesis, 2000); in comparison, PMI doesn’t consider adjustments.
- Lean construction tries to mitigate variation in every aspect (product quality, rate of work) and manage the remaining variation, while PMI doesn’t consider variation mitigation and management. (Ballard, PhD thesis, 2000)
- Lean approach tries to make continuous improvements in the process, workflows and product (Howell, 1999); whereas PMI approach doesn’t pay that much attention to continuous improvement.
- In lean construction, decision making is distributed in design production control systems (Ballard, PhD thesis, 2000); by comparison, in PMI decision making is centered to one manager some times.
- Lean construction tries to increase transparency between the stakeholders, mangers and labourers, in order to know the impact of their work on the whole project (Howell, 1999); on the other hand, PMI doesn’t consider transparency in its methods.
- In lean construction a buffer of sound assignments is maintained for each crew or production unit (Ballard, PhD thesis, 2000); in contrast, PMI method doesn’t consider a backlog for crews.
- Lean construction is developing new forms of commercial contracts to give incentives to suppliers for reliable work flow and optimization at the deliverable-to-the-client level (Howell, 1999); while PMI doesn’t have such policy.
- Lean construction production system design resists the tendency toward local suboptimization. (Ballard thesis); however, PMI persists on optimizing each activity.
- The PMI-driven approach only considers managing a project at the macro-level. This is necessary but not sufficient for the success of projects. Lean Construction encompasses Project and Production Management, and formally recognizes that any successful project undertaking will inevitably involve the interaction between project and production management. (Abdelhamid et al. 2008)
Lean Construction FAQs
- Answers provided by Lean Construction Institute (LCI) Executive Director Greg Howell and Academic Forum Chairperson Tariq Abdelhamid -
1. What is Lean Construction?
- Lean Construction a different way to see, understand and act in the world. For example, waste in current practice is normally understood as labor utilization. Learning to see contingency as waste is the big step we need if we are to make a step change in construction, one commensurate with managing inventory just in time.
- Lean Construction is a philosophy - it is something that people do. Lean Construction a comprehensive system of ideas that lead to the flawless delivery of the built environment. This philosophy is practiced using the Lean Project Delivery System, which continues to evolve as more is learned from practice and research.
2. Is Lean Construction just applying Lean Production in construction?
- No. Lean Construction started as an attempt to reform the way work in projects is managed. Once it was appreciated that work moves between specialists in construction by the administrative act of making an assignment, it was possible to adapt principles and practices direct from Toyota Production System. However, Lean Construction is more than Lean Production in Construction. The project-oriented execution of construction projects made it necessary to develop unique methods and tools for construction.
3. When did Lean Construction begin?
- LC began with two main insights. First, the inability of the current planning system to produce reliable workflow. Second, the lack of a theoretical understanding of what is production in construction. This was in the middle 1980s to early 1990s. A more formal start could be identified as the first meeting of the International Group for Lean Construction in 1993. Lean Construction remains to be a research and practice area in constant flux.
4. What are the major differences between a project run based on Lean Construction and one that is not?
- Lean works because the work on the project is designed and managed by those who do it. LC designs and activates the network of commitments necessary to deliver the project.
- The “tragedy of the commons” is prevented. This tragedy results because individually rational decisions are destructive to the overall project. Instead of local optimization driven by labor utilization, Lean Construction targets system optimization that is driven by throughput. Work on Lean Construction projects is deliberately and systematically organized to maximize the project and not the pieces, and commercial terms are adjusted to align interests, and promote improvement and minimize risk to the involved parties.
- Another difference is that the construction process, the building operation and maintenance, and the recycling/salvage needs are inputs to the design and not outputs of it; inputs needed to start the work are provided and issues (waste) that prevent finishing started work are eliminated; problem solving and learning is the job of those involved in the project and not just part of the job; Where possible, materials are brought to the site in the same way concrete is; The aim is for a zero punchlist and not to zero-out the punchlist.
5. Building Information Modeling (BIM) aims to build a collaborative relation between designers and constructors, so how is that different from LC?
- BIM is technology. It doesn't aim, it does make possible different conversations because it is a great tool for spatial representation of design. LC structures those conversations and connecting design, logistics and installation. LC designs and activates the network of commitments necessary to deliver the project. It is necessary to enable Lean Construction ideals but not sufficient.
6. Is Lean Construction like Leadership in Energy & Environmental Design (LEED) where you have to commit to a certain level of compliance and the project is checked against that?
- No. Lean is a way to manage and improve work. LEED and GREEN are value propositions - an end. Lean Construction is the means to better arrive at that end.
7. What percentage of the US construction industry is adopting it?
- There is no definitive way of knowing. The number of LCI state-based chapters are increasing which reflects an increased interest in the industry. The corporate and individual membership of LCI is increasing, again indicating interest is rising. The AGC of America Building Division has began to develop Lean Construction training for construction site professionals. AGC estimates that one in seven contractors is using Lean Construction. According to LCI, there is still time to be an early adopter.
8. Is Lean Construction accepted more in other countries than in the US?
- There is significant implementation in Germany, UK, Denmark (the longest running with strong Union support), Sweden, Brazil, Chile, Peru, Taiwan, Malaysia, India, Egypt, Israel, and Nigeria.
9. What is the primary difference between Lean Production and Lean Construction?
- Lean production is the inspiration for lean construction, but cannot be grafted onto construction.
- Production & construction are different; construction is more like ship-building or airplane-building, where the workers move and the product is stationary instead of the product moving between stationary workers like in production.
- In production, typically the same part is produced in mass volume. This is not the same as construction, unless major generalizations are made (i.e. a wall is a wall, even if made of different material and on different projects). So, Lean Construction focuses heavily on the similarity in the process of constructing more so than on the product of construction.
- Sven Bertelsen (a Lean Construction Scholar) encouraged the move from construction on to project production in general because he sees the project as the basic form of production where mass production is just the simplified version Toyota and Shingo demonstrated as new thoughts but construction has to establish its own thinking.
- Lean Production primarily focuses on the reduction of the time from order, of any transaction be it assembly, billing, supply, etc, to delivery. This reduction of time is achieved by the elimination of waste (the unproductive use of resources) that is captured in the mnemonic word “ DOWNTIME”. Respect for people and continuous improvement guides the reduction of waste. Lean Construction has been inspired by this but also by other paradigms. Production in construction is conceptualized as a transformation of inputs to outputs through a flow process of materials and information that is directed at maximizing value to the client. Lean Production is not about maximizing value to the client, otherwise, the Cadillac would cost the same as the Chevy, the Lexus would cost the same as the Camry, etc. Lean Construction also draws on the new theories regarding project management as well as social science, and complexity theory. A construction project is considered as a project-based production system.
10. Can the concept of Heijunka be used in construction? Why?
- Heijunka = production leveling. Production leveling for a manufacturing plant relies on being able to “create” stable demand, so that the Takt time for the plant is constant. Toyota does this through its marketing and sales division. The TPS is quite vulnerable otherwise. Of course, it is not always perfect but they strive for this stability, especially with tactics such as mixed-model production.
- Construction is project-based and the requirements needed to complete a project are known – the quantities are known, with a time and budget constraint. A construction project needs stability and reliability in the workflow so that it is not going in fits and stops. This is achieved using the Lookahead and weekly work planning process with a constraint screening process (elements of the trademarked Last Planner System), and not just an FYI (for-your-information) coordination meeting. The act of keeping a workable backlog is designed to keep work flowing and progressing.
- The use of the line of balance (linear scheduling, flow lines) is a nice tool to visualize the production rates of different activity and avoid the interruption of work as well as the problem of overproduction. However, in Lean Construction it is not desirable to have one crew finish too fast or too slow.
- Crew balancing is not an example of heijunka. Crew balancing may lead us to locally optimize at the expense of the system throughput.
11. Contrast “lean work structuring” with “work breakdown structure”.
- A WBS should not be used as the sole planning tool for a project. It is a great brainstorming tool to understand the project. It is probably the best scheme to develop a MASTER schedule. The problem is using it for more than what it is capable of. Project cost and project duration can't be determined by simply working the WBS. The WBS is looking at activities in an independent fashion in support of transformation thinking. The WBS assumes that optimizing the part will optimize the whole – reduce the part cost and duration and you will reduce the cost and the duration of the whole. Get the lowest price and the shortest time for drywall separate from electrical and plumbing and you find on site that the work of these three trades is so intertwined that the cost and duration you received for drywall was a pipe dream.
- A WBS is a tool to use in Lean Work Structuring.
- LWS is thinking production, operation, maintenance, and recyclablity during design. It also focuses on work package (not trade or contract packages), i.e. the wall, or the ceiling, and how that work will be accomplished throughout its upstream and downstream stages.
12. What are the differences between project control and production control?
- Project control monitors progress using lagging indicators such as schedule and cost variance. It is sometimes too late to do anything about the project going off-track or it takes too much to get it back on track. So, project control is reactive. Think of the stock market. The DJI - Dow Jones Industrial Average – only informs about what has happened to the market after the fact. It’s like taking the temperature of a patient – it indicates whether a person has fever but not why.
- In Lean Construction, production control is practiced with an aim to make things happen to prevent the project from having a fever. Production control is pro-active because work is facilitated by removing the known process and system constraints.
13. Is Value Stream Mapping (VSM) a tool for construction?
- VSM has a place in construction. And this applies to many other tools and techniques that are being used to enable Lean Construction ideals, but are not widely known or shared by those practicing them. The Last Planner System is one example.
- As far as VSM is concerned, it provides a big picture view of the flow problems in whatever system is under study. It's a flow improvement tool and not a process improvement tool (flow kaizen vs. process kaizen). A great bottleneck finder.
- VSM has been applied to reduce the time for processing specialty contractor payment applications (from 40 days to 5 or so – see IGLC11 in a paper by Mastroianni and Abdelhamid). An architecture office also is using it for streamlining the submittal and show drawings review and approval process because of delays and complaints by contractors. An example for application on a construction site is that of a construction company that specializes in suspended ceiling and drywall installation. They used VSM to identify time that drywall sheets and tiles spend before being put in place. They used the results to justify the cost of using a temp warehouse (supermarket) close to the site and deploying a pull delivery system. The result, using the SAME installation process, was less time per SQFT because material handling was almost down to single touch – from the truck to the installation location. Interestingly, they then used work sampling techniques (as described in Oglesby, Parker and Howell 1989) to improve the dry walling process itself.
- In Brazil, VSM is being used mostly by academics. As any other tool developed for manufacturing it needs some adaptation in order to become useful for construction. Researchers at the University of Campinas (UNICAMP) have developed some innovative applications of VSM for administrative and design processes and also as part of production system design of construction projects. They have published a few papers in previous IGLC conferences.
14. Is Integrated Project Delivery the same as Lean Construction?
- No. In fact, the ideals of Lean Construction are enabled by using the Integrated Project Delivery approach. IPD is necessary but not sufficient. In other words, just having an IPD will not guarantee meeting the Lean Construction ideals. IPD is defined on this page (scroll up).
- IPD is a Relational Contracting approach that aligns project objectives with the interests of key participants, through a team-based approach. The primary Team Members would include the Architect, key technical consultants as well as a general contractor and key subcontractors. It creates an organization able to apply the principles and practices of the Lean Project Delivery System.] (Matthews and Howell 2005). IPD is defined at http://www.leanconstruction.org/glossary.htm. For more information see http://www.leanconstruction.org/lcj/V2_N1/LCJ_05_003.pdf
[IPD is a registered business mark by Lean Construction Institute with the US PTO - Class 37; Registration # 2,971,009]
Commercial arrangements that support IPD and Lean Project Delivery
There are at least five principal forms of contract that support Lean construction- Integrated Form of Agreement for Lean Project Delivery (IFoA)(USA) developed around explicit lean construction principles for Sutter Health by their legal counsel, Will Lichtig, and used by various other owners/clients.
- ConsensusDOCS300 (USA) a derivative of IFoA http://www.consensusdocs.org/
- AIA C191-2009 Standard Form Multi-Party Agreement for IPD (USA) AIA uses IPD to refer to a new project delivery system. http://www.aia.org/groups/aia/documents/pdf/aias076340.pdf for a list of distributors
- PPC2000 International (UK) http://www.acarchitects.co.uk/publications.htm
- Alliancing Agreement (Australia) a new standard form is under development
These papers will be helpful to explain IPD and IFoA http://www.leanconstruction.org/lcj/V2_N1/LCJ_05_003.pdf and http://www.leanconstruction.org/lcj/V2_N1/LCJ_05_008.pdf
for discussions of Alliancing, PPC2000 and IFoA please see http://www.lean-in-public.org/lips_en_proceedings.html
LC Networks, Teaching and Research
- The International Group for Lean Construction (IGLC) holds an annual conference
- The Lean Construction Institute conducts research and industry outreach activities
- There are national Lean Construction Institutes in UK, Denmark, Sweden, Norway, Chile and Germany
- The European Group for Lean Construction holds meetings twice a year
- The Lean Construction Journal launched October 2003.
- (P2SL) Project Production Systems Laboratory at the University of California, Berkeley] The Project Production Systems Laboratory (P2SL) is dedicated to developing and deploying knowledge and tools to manage project production systems and organizations producing and delivering goods and services through such systems. Research includes lean construction.
- (CIREC) The Construction Industry Research and Education Center at the School of Planning, Design and Construction, Michigan State University investigates and develops efficient and effective construction processes, guided by Lean Construction principles, that result in a built environment with maximum value to both the construction client and participants. The center provides research, outreach, and education services to the construction industry.
- A number of universities around the worldWorldWorld is a common name for the whole of human civilization, specifically human experience, history, or the human condition in general, worldwide, i.e. anywhere on Earth....
teach and conduct research on lean construction.- First program to teach Lean Construction as modules within its existing graduate offering is University of California, Berkeley (circa 1997).
- First program to teach Lean Construction as a named, full graduate course offering (CMP831: Lean Construction Principles and Methods) is Michigan State University (2002).
- First PhD in Lean Construction was awarded to Dr. Lauri Koskela in 2000 and to Dr. Glenn Ballard, also in 2000!
- First Masters in Lean Construction is from
- Universities active in LC research and Teaching:
- US: U.C. Berkeley; Michigan State University; San Diego State University; Texas A & M; Washington State University; Virginia Tech; Arizona State University; Purdue University; Bowling Green University; North Carolina State University; University of Texas – Austin; University of Colorado –Boulder;
- UK: University of Salford; University of Edinburgh, University of Manchester;
- Brazil:
- Chile: Centro de Excelencia en Gestion de Produccion GEPUC - Pontificia Universidad Catolica de Chile (http://www.gepuc.cl)
- Finland
- Denmark
- Australia
- Israel
- New Zealand
- Thailand
- South Korea
- Japan
- Hong Kong
- Netherlands
- No University yet offers a fully integrated lean construction programme.
- moladiMoladiMoladi is a South African construction company specialising in a reusable plastic formwork for use in affordable housing and low cost housing projects, mainly in third world countries. The process involves creating a mould the form of the complete house. This wall mould is then filled with an...
Lean Construction of mass low cost housing
-
- there is a proposal for a global Masters programme by action research and learning to be delivered by a group of collaborating universities. (sample course materials at http://www.leanconstructionlighthouse.org)
- There are a number of practitioner support and networking groups on the web
- Lean Construction Institute on LinkedinLinkedInLinkedIn is a business-related social networking site. Founded in December 2002 and launched in May 2003, it is mainly used for professional networking. , LinkedIn reports more than 120 million registered users in more than 200 countries and territories. The site is available in English, French,...
- Lean Construction Institute UK on LinkedinLinkedInLinkedIn is a business-related social networking site. Founded in December 2002 and launched in May 2003, it is mainly used for professional networking. , LinkedIn reports more than 120 million registered users in more than 200 countries and territories. The site is available in English, French,...
- Lean Construction Network on LinkedinLinkedInLinkedIn is a business-related social networking site. Founded in December 2002 and launched in May 2003, it is mainly used for professional networking. , LinkedIn reports more than 120 million registered users in more than 200 countries and territories. The site is available in English, French,...
. LCN offers a number of Regional Sub-groups
- Lean Construction Institute on Linkedin
-
- http://www.agcleanforum.org The AGC of America Lean Construction Forum