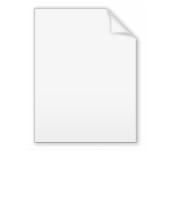
M9 Armored Combat Earthmover
Encyclopedia
The M9 Armored Combat Earthmover is a highly mobile armored tracked vehicle that provides combat engineer support to front-line forces. Its tasks include eliminating enemy obstacles, maintenance and repair of roads and supply routes, and construction of fighting positions.
for guns, tanks and other battlefield systems to increase their survivability. The ACE breaches berms, prepares anti-tank ditches, prepares combat roads, removes roadblocks and prepares access routes at water obstacles.
The engine, drive train and driver's compartment are laid out in the rear of the vehicle, while the front features an 8.7 cubic yard (6.7 m³) bowl, apron and dozer blade. Armor consists of welded aluminum with selected steel and aramid-laminated plates. An armored cupola containing eight vision blocks covers the driver's compartment. The vehicle hull is a welded and bolted aluminum structure with a two speed winch capable of 25,000 pound (110 kN) line pull. Towing pintle and airbrake connections are provided. It is equipped with a unique suspension system which allows the front of the vehicle to be raised, lowered, or tilted to permit dozing, excavating, rough grading and ditching functions. In addition, the M9 has armor protection against small arms and artillery fragmentation, a smoke screening capability and chemical-biological protection for the operator. It is capable of 30 mph (50 km/h) road speed, is transportable in C-130, C-141, and C-5 aircraft and can swim at 3 mph (5 km/h) under ideal conditions (though with the deletion of the swim mission, swim related components are no longer required to be maintained for the M9 ACE).
By raising the dozer blade and using its scraper blade, the ACE can fill itself with ballast to improve dozing efficiency. Another key feature of the M9 is its unique hydropneumatic suspension system. The principal components are eight high-pressure hydraulic rotary actuators (four on each side) which connect to the roadwheel stations. During high-speed travel, this system assures a smooth ride through the use of shock-absorbing accumulators. In earthmoving operations, the operator rotates the actuators, thus lowering the apron and blade for digging.
A typical combat engineer battalion will contain 22 ACES - seven per company plus an operational readiness float. The active Army has a total of 447 M9 ACEs.
The M9 ACE System Improvement Plan (SIP) is a multi-phased program designed to improve the performance, durability, readiness and MANPRINT characteristics of the vehicle. The multi-phased nature of the program is necessitated by the available funding stream. SIP Phase 1 consisted of: bolt-on front track retainers, steel skid plates, high pressure hydraulic filters, battery box deflector, scarifier blade uplocks, scarifier blade for half the fleet, inserts for improved winches, ejector debris shield, and modified rear bump stops. Kits were applied at units by depot and DOL teams during 1993 and early 1994. SIP Phase 2 consists of: thicker roadarm retainers, preformed radiator hoses, lengthened oil drain line, redesigned parking brake linkage and steering rod, vent fan filter, tachometer/speedometer grease fittings, inclinometers, and steel CB/GS linkage. They are funded for and installed by units or through attrition.
Hydraulic troubleshooting procedures - Reformat all hydraulic troubleshooting procedures to simplify fault isolation. The ACE has an extensive and complex hydraulic system. Insufficient hydraulic troubleshooting expertise is the single largest contributor to M9 NMCM downtime. It also contributes to NMCS time because good components are being removed and replacements ordered unnecessarily. Unit mechanics require detailed and complete troubleshooting procedures which are easy to use. Goal is to cut troubleshooting time and eliminate ambiguous or faulty troubleshooting paths. No hardware changes to the vehicles are included in this project.
Actuator mounting rings - Provide a stronger mounting system for the rotary actuators. Currently, actuator mounting bolts screw into steel inserts in the aluminum hull. The inserts pull out, resulting in loose actuators, hull damage, hydraulic line failures and damage to roadarms and actuators. Under this project, steel rings will be fastened inside the hull. The actuator bolts will pass through the existing mounting points and screw into the steel rings. The field modification installs rings at the front actuator station only; however, the rings can be installed at the three other stations as well if those hull inserts should come loose.
Bowl access plates - Provide easy access to the front actuators for troubleshooting and maintenance. Front actuators, accumulators and hydraulic lines require both scheduled and unscheduled maintenance. Currently, mechanics must perform troubleshooting and repairs from underneath the ACE, working in dark and cramped conditions. This increases maintenance time and leads to leaking hydraulic fittings. Access through the bowl floor will decrease maintenance time and eliminate most causes of actuator hydraulic leaks.
Hydraulic filtration improvements - Hydraulic cleanliness is critical on the ACE. To achieve the cleanest possible hydraulic system, a more efficient return line filter and a high pressure filter at the compensating pump output will be added. Three hydraulic tests points are being added at the high pressure filters. Also as part of this project, the two compensating pump suction hoses will be modified to prevent collapse and cavitation. Finally, the compensating pump adjustment will be improved by replacing the existing adjusting clamp with an adjusting screw and jam nut
.
'Hub and sprocket redesign - Current hub requires two unique sprockets. The outer one tends to bend and is difficult to fabricate, resulting in producibility delays and lengthy NMCS downtime. This project will eliminate the current outer sprocket and permit use of the inner sprocket in both positions. Goal is to eliminate shortages and higher cost of outer sprockets, and reduce maintenance burden. Also, the hub will be piloted onto the final drive output shaft, reducing the shear load and resultant failure of mounting bolts.
Semi-automatic track tensioner/adjuster - Currently, the operator checks and manually adjusts track tension using a grease gun before each mission. The new system will allow the operator to adjust track hydraulically from within the driver's compartment. With the manual system, the tension setting is a compromise, since the track needs sufficient slack to allow the suspension to go from sprung mode (travel) to unsprung mode (dozing). The semi-automatic track tensioner will relax the track to change between sprung and unsprung and then re-tension the track allowing a tighter envelope. This will reduce the number of track throws and associated damage and wear to suspension components and adjacent hull components.
Final drive improvements - Design an oil level indicator and modify the output shaft. Operators cannot assess the condition or lack of oil because there is no method to check oil level. This project will permit detection of water, contamination or loss of oil. Also, the output shaft will be modified to accommodate the redesigned sprocket hub.
Improved winch - With the current winch, the ACE has a limited ability to self-recover. This project will increase winch rating from 25,000 lbf to 35,000 lbf (110 to 155 kN), double cable length from 100 feet to 200 feet (30 to 60 m), and add a friction brake to enable the M9 to hold a load on a slope.
Steel dozer blade - Develop a steel replacement for the existing aluminum dozer blade. The current aluminum blade suffers damage when used in rocky terrain, is marginally suited for use with scarifier teeth, and generally wears down. Repair is difficult and involves time-consuming aluminum welding, resulting in extensive mission downtime. The complex hollow-box design also means that replacement blades are very expensive and have long leadtimes. A steel dozer blade will be less expensive, more resistant to wear and easier to repair if damaged.
"Dozer Blade Update" - The blades are no longer aluminum. The blades are made of steel. They are fabricated in Pennsylvania.
Automatic blade folder - This project is now part of SIP 4 - Let the operator remotely fold or unfold dozer blade from the crew compartment. This procedure now takes up to 1/2 hour to perform, requires crew to be exposed and stops the ongoing mission. Failure to fold the blade during cross-country travel could result in vehicle damage or operator injury. This project is not a readiness enhancement, rather it offers a major performance improvement to the mission.
In Operation Desert Storm the M9 Armored Combat Earthmover (ACE) performed exceptionally well in support of combat operations. The ACE proved to be a successful combination of armored vehicle and combat earthmover that was capable of keeping pace with the manoeuvre units, while providing crew survivability. While not as efficient as the D7 Dozer in earth moving, its ability to move with maneuver forces over several hundred kilometers of desert allowed it to successfully perform a wide variety of missions such as construction of combat roads and trails, survivability positions and berms. It is however, a fallacy that the ACE can move as fast as an M1 or M2. The vehicle is governed to prevent this.
But the training of ACE operators appeared to be inadequate. Operators were unfamiliar with the techniques associated with dozing, scraping, cut and fill ops, and grading. The ACE experienced trouble in reducing the berms associated with Iraqi tank ditches (berm on enemy side). Due to the location of the driver in relation to the vehicle blade, he cannot see the blade or determine when he is about to tip over. The ACE needs a front mounted telescope or a side mounted periscope to overcome this deficiency. The ACE led the way in breaching the border berm between Saudi Arabia and Iraq, and in reducing trench-lines during the assault breach. In both instances the ACE performed extremely well. Problems were encountered, however, due to the ACE's shortcomings. One commander referred to the ACE operator as "Alone, Unarmed, and Unafraid". This highlights the ACE's major shortcomings as a piece of mobility equipment used during direct fire engagements. ACE operators, usually 19 year old PFC's, led the 7th Corps breach into hostile country, alone, unarmed and unafraid. Fortunately, they met with very light resistance. Otherwise, mortality among ACE operators would have been very high. The ACE is a single operator vehicle, without the moral and physical advantages of a crew with an NCO in charge, and without the advantage of a weapon for local suppression. Habitually, maneuver task forces provided two Bradley Fighting Vehicles to protect the ACE during breaching ops. While this is a high price to pay for protection of one vehicle, commanders deemed it necessary for the success of their operations. Commanders felt that the ACE needs an additional crewman and a protective weapon such as a .50 caliber machine gun or the Mark 19 automatic grenade launcher.
History
The M9 is a highly mobile, armored, amphibious combat earthmover. It was first fielded in 1986. capable of supporting forces in both offensive and defensive operations. It performs critical combat engineer tasks such as digging hull defilade fighting positionsHull-down
The term hull-down describes the situation where the upper part of a vessel or vehicle is visible, but the main, lower body is not; the opposite term hull-up describes the situation where all of the body is visible....
for guns, tanks and other battlefield systems to increase their survivability. The ACE breaches berms, prepares anti-tank ditches, prepares combat roads, removes roadblocks and prepares access routes at water obstacles.
The engine, drive train and driver's compartment are laid out in the rear of the vehicle, while the front features an 8.7 cubic yard (6.7 m³) bowl, apron and dozer blade. Armor consists of welded aluminum with selected steel and aramid-laminated plates. An armored cupola containing eight vision blocks covers the driver's compartment. The vehicle hull is a welded and bolted aluminum structure with a two speed winch capable of 25,000 pound (110 kN) line pull. Towing pintle and airbrake connections are provided. It is equipped with a unique suspension system which allows the front of the vehicle to be raised, lowered, or tilted to permit dozing, excavating, rough grading and ditching functions. In addition, the M9 has armor protection against small arms and artillery fragmentation, a smoke screening capability and chemical-biological protection for the operator. It is capable of 30 mph (50 km/h) road speed, is transportable in C-130, C-141, and C-5 aircraft and can swim at 3 mph (5 km/h) under ideal conditions (though with the deletion of the swim mission, swim related components are no longer required to be maintained for the M9 ACE).
By raising the dozer blade and using its scraper blade, the ACE can fill itself with ballast to improve dozing efficiency. Another key feature of the M9 is its unique hydropneumatic suspension system. The principal components are eight high-pressure hydraulic rotary actuators (four on each side) which connect to the roadwheel stations. During high-speed travel, this system assures a smooth ride through the use of shock-absorbing accumulators. In earthmoving operations, the operator rotates the actuators, thus lowering the apron and blade for digging.
A typical combat engineer battalion will contain 22 ACES - seven per company plus an operational readiness float. The active Army has a total of 447 M9 ACEs.
Status
Insufficient funds were available to purchase all Armored Combat Earthmovers (ACE) required during initial and subsequent procurements. A total of 448 systems have been fielded with 57 additional ACEs needed to complete fielding to 87 percent of Force Package II and prepositioned stocks. In addition Phase III of the System Improvement Plan has yet to be started. This phase includes a variety of track, hull and blade enhancements. Microclimatic cooling system is planned to be fielded FY 96. System Improvement Plan Phase I & II is complete. Phase III & IV is under development.The M9 ACE System Improvement Plan (SIP) is a multi-phased program designed to improve the performance, durability, readiness and MANPRINT characteristics of the vehicle. The multi-phased nature of the program is necessitated by the available funding stream. SIP Phase 1 consisted of: bolt-on front track retainers, steel skid plates, high pressure hydraulic filters, battery box deflector, scarifier blade uplocks, scarifier blade for half the fleet, inserts for improved winches, ejector debris shield, and modified rear bump stops. Kits were applied at units by depot and DOL teams during 1993 and early 1994. SIP Phase 2 consists of: thicker roadarm retainers, preformed radiator hoses, lengthened oil drain line, redesigned parking brake linkage and steering rod, vent fan filter, tachometer/speedometer grease fittings, inclinometers, and steel CB/GS linkage. They are funded for and installed by units or through attrition.
SIP Phase 3 - Detailed Description of Projects
Hardened track pin with modified track shoe - Current track pins bend, causing NMCM time in two different ways. They deform the bushings, resulting in track maintenance, and they are difficult to remove when bent. Harder track pins will allow higher torque which will reduce bending moment. This will reduce frequency of track failures and make pin removal easier when track needs to be separated. In addition to the hardened pins, future buys of track will also have a larger pocket for the track pin nut. This will make it easier to get a socket on the nut even after the track edges get worn.Hydraulic troubleshooting procedures - Reformat all hydraulic troubleshooting procedures to simplify fault isolation. The ACE has an extensive and complex hydraulic system. Insufficient hydraulic troubleshooting expertise is the single largest contributor to M9 NMCM downtime. It also contributes to NMCS time because good components are being removed and replacements ordered unnecessarily. Unit mechanics require detailed and complete troubleshooting procedures which are easy to use. Goal is to cut troubleshooting time and eliminate ambiguous or faulty troubleshooting paths. No hardware changes to the vehicles are included in this project.
Actuator mounting rings - Provide a stronger mounting system for the rotary actuators. Currently, actuator mounting bolts screw into steel inserts in the aluminum hull. The inserts pull out, resulting in loose actuators, hull damage, hydraulic line failures and damage to roadarms and actuators. Under this project, steel rings will be fastened inside the hull. The actuator bolts will pass through the existing mounting points and screw into the steel rings. The field modification installs rings at the front actuator station only; however, the rings can be installed at the three other stations as well if those hull inserts should come loose.
Bowl access plates - Provide easy access to the front actuators for troubleshooting and maintenance. Front actuators, accumulators and hydraulic lines require both scheduled and unscheduled maintenance. Currently, mechanics must perform troubleshooting and repairs from underneath the ACE, working in dark and cramped conditions. This increases maintenance time and leads to leaking hydraulic fittings. Access through the bowl floor will decrease maintenance time and eliminate most causes of actuator hydraulic leaks.
Hydraulic filtration improvements - Hydraulic cleanliness is critical on the ACE. To achieve the cleanest possible hydraulic system, a more efficient return line filter and a high pressure filter at the compensating pump output will be added. Three hydraulic tests points are being added at the high pressure filters. Also as part of this project, the two compensating pump suction hoses will be modified to prevent collapse and cavitation. Finally, the compensating pump adjustment will be improved by replacing the existing adjusting clamp with an adjusting screw and jam nut
Jam nut
A jam nut is a low profile type of nut, typically half as tall as a standard nut. It is commonly used as a type of locknut, where it is "jammed" up against a standard nut to lock the two in place...
.
'Hub and sprocket redesign - Current hub requires two unique sprockets. The outer one tends to bend and is difficult to fabricate, resulting in producibility delays and lengthy NMCS downtime. This project will eliminate the current outer sprocket and permit use of the inner sprocket in both positions. Goal is to eliminate shortages and higher cost of outer sprockets, and reduce maintenance burden. Also, the hub will be piloted onto the final drive output shaft, reducing the shear load and resultant failure of mounting bolts.
Semi-automatic track tensioner/adjuster - Currently, the operator checks and manually adjusts track tension using a grease gun before each mission. The new system will allow the operator to adjust track hydraulically from within the driver's compartment. With the manual system, the tension setting is a compromise, since the track needs sufficient slack to allow the suspension to go from sprung mode (travel) to unsprung mode (dozing). The semi-automatic track tensioner will relax the track to change between sprung and unsprung and then re-tension the track allowing a tighter envelope. This will reduce the number of track throws and associated damage and wear to suspension components and adjacent hull components.
Final drive improvements - Design an oil level indicator and modify the output shaft. Operators cannot assess the condition or lack of oil because there is no method to check oil level. This project will permit detection of water, contamination or loss of oil. Also, the output shaft will be modified to accommodate the redesigned sprocket hub.
Improved winch - With the current winch, the ACE has a limited ability to self-recover. This project will increase winch rating from 25,000 lbf to 35,000 lbf (110 to 155 kN), double cable length from 100 feet to 200 feet (30 to 60 m), and add a friction brake to enable the M9 to hold a load on a slope.
Steel dozer blade - Develop a steel replacement for the existing aluminum dozer blade. The current aluminum blade suffers damage when used in rocky terrain, is marginally suited for use with scarifier teeth, and generally wears down. Repair is difficult and involves time-consuming aluminum welding, resulting in extensive mission downtime. The complex hollow-box design also means that replacement blades are very expensive and have long leadtimes. A steel dozer blade will be less expensive, more resistant to wear and easier to repair if damaged.
"Dozer Blade Update" - The blades are no longer aluminum. The blades are made of steel. They are fabricated in Pennsylvania.
Automatic blade folder - This project is now part of SIP 4 - Let the operator remotely fold or unfold dozer blade from the crew compartment. This procedure now takes up to 1/2 hour to perform, requires crew to be exposed and stops the ongoing mission. Failure to fold the blade during cross-country travel could result in vehicle damage or operator injury. This project is not a readiness enhancement, rather it offers a major performance improvement to the mission.
Employment concept
The M9 is capable of performing mobility, countermobility and survivability tasks in support of light or heavy forces. Tasks to be performed are the excavation and preparation/reduction of obstacles, bridging operations, battle positions, strong points, and protective emplacements for command posts, air defense, communications equipment and critical supply/logistical bunkers. Other major tasks will be route clearing and maintenance in conjunction with both defensive and offensive operations.In Operation Desert Storm the M9 Armored Combat Earthmover (ACE) performed exceptionally well in support of combat operations. The ACE proved to be a successful combination of armored vehicle and combat earthmover that was capable of keeping pace with the manoeuvre units, while providing crew survivability. While not as efficient as the D7 Dozer in earth moving, its ability to move with maneuver forces over several hundred kilometers of desert allowed it to successfully perform a wide variety of missions such as construction of combat roads and trails, survivability positions and berms. It is however, a fallacy that the ACE can move as fast as an M1 or M2. The vehicle is governed to prevent this.
But the training of ACE operators appeared to be inadequate. Operators were unfamiliar with the techniques associated with dozing, scraping, cut and fill ops, and grading. The ACE experienced trouble in reducing the berms associated with Iraqi tank ditches (berm on enemy side). Due to the location of the driver in relation to the vehicle blade, he cannot see the blade or determine when he is about to tip over. The ACE needs a front mounted telescope or a side mounted periscope to overcome this deficiency. The ACE led the way in breaching the border berm between Saudi Arabia and Iraq, and in reducing trench-lines during the assault breach. In both instances the ACE performed extremely well. Problems were encountered, however, due to the ACE's shortcomings. One commander referred to the ACE operator as "Alone, Unarmed, and Unafraid". This highlights the ACE's major shortcomings as a piece of mobility equipment used during direct fire engagements. ACE operators, usually 19 year old PFC's, led the 7th Corps breach into hostile country, alone, unarmed and unafraid. Fortunately, they met with very light resistance. Otherwise, mortality among ACE operators would have been very high. The ACE is a single operator vehicle, without the moral and physical advantages of a crew with an NCO in charge, and without the advantage of a weapon for local suppression. Habitually, maneuver task forces provided two Bradley Fighting Vehicles to protect the ACE during breaching ops. While this is a high price to pay for protection of one vehicle, commanders deemed it necessary for the success of their operations. Commanders felt that the ACE needs an additional crewman and a protective weapon such as a .50 caliber machine gun or the Mark 19 automatic grenade launcher.
Basis of issue
- 7 per Engineer Company in a Heavy Division
- 6 per Armored Cavalry Regiment
- 6 per Engineer Company, Heavy Separate Brigade
- 6 per Engineer Combat Company (Mech) Corps
- 6 per HHC, Engineer Battalion, Light Infantry Division
- 4 per Engineer Company, Separate Infantry Brigade (Ribbon)
- 2 per Engineer Company (Assault Float Bridge)(Ribbon) at Corps
- 1 per Engineer Company (Medium Girder Bridge)
- 1 per Bridge Company (Ribbon)
Training/personnel
TRADOC instructors and New Equipment Training Teams (NETT) will be trained by the contractor. Initial training will be by NETT for Combat Engineer organizations issued the M9. Institutional training at U.S. Army Engineer Center at Fort Leonard Wood will provide training for the operator (MOS 12F) and maintainer (MOS 62B). Operator proficiency will be maintained by Training Extension Course tapes and extension training materials.External links
- Armored Combat Earthmover M9
- M-9 Armored Combat Earthmover at CombatIndex
- M9 Armored Combat Earthmover (ACE) abstract at Jane's