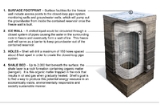
Mahogany Research Project
Encyclopedia
The Shell's in situ conversion process (Shell ICP) is an in situ
shale oil extraction technology to convert kerogen
in oil shale
to shale oil
. It is developed by the Shell Oil Company
.
Shell's in situ conversion process has been under development since the early 1980s. In 1997, the first small scale test was conducted on the Mahogany property, located 200 miles (321.9 km) west of Denver on Colorado's Western Slope
in the Piceance Creek Basin
. Since 2000, additional research and development activities have carried on as a part of the Mahogany Research Project. The oil shale heating at Mahogany started early 2004, and was completed mid-2005.
from the rock so that it can be pumped to the surface and made into fuel
. In this process, a freeze wall is first to be constructed to isolate the processing area from surrounding groundwater. To maximize the functionality of the freeze walls, adjacent working zones will be developed in succession. 2000 feet (610 m) wells, eight feet apart, are drilled and filled with a circulating super-chilled liquid to cool the ground to -60 °F. Water is then removed from the working zone. Heating and recovery wells are drilled at 40 feet (12.2 m) intervals within the working zone. Electrical heating element
s are lowered into the heating wells and used to heat oil shale to between 650 °F (343.3 °C) and 700 °F (371.1 °C) over a period of approximately four years. Kerogen
in oil shale is slowly converted into shale oil and gases, which are then flow to the surface through recovery wells.
In 2006, Shell estimated that over the project life cycle, for every unit of energy consumed, three to four units would be produced. Such an "energy returned on energy invested" would be significantly better than that achieved in the Mahogony trials. For the 1996 trial, Shell applied 440,000 kWh (which would require about 96 toe energy input in a coal-fired plant), to generate 250 barrels (39,746.8 l) of oil (37 toe output).
Extensive water use and the risk of groundwater
pollution are the technology's greatest challenges.
lease to pursue a large demonstration with a capacity of 1500 oilbbl/d; Shell has since dropped those plans and is planning a test based on ICP that would produce a total of minimum 1500 barrels (238,480.9 l), together with nahcolite
, over a seven year period.
In Israel, IEI, a subsidiary of IDT Corp.
is planning a shale pilot based on ICP technology. The project would produce a total of 1,500 barrels. However, IEI has also announced that any subsequent projects would not use ICP technology, but would instead utilize horizontal wells and hot gas heating methods.
In Jordan, Shell subsidiary JOSCO plans to use ICP technology to achieve commercial production by the "late 2020s." In October, 2011, it was reported that JOSCO had drilled more than 100 test holes over the prior two years, apparently for the sake of testing shale samples.
In situ
In situ is a Latin phrase which translated literally as 'In position'. It is used in many different contexts.-Aerospace:In the aerospace industry, equipment on board aircraft must be tested in situ, or in place, to confirm everything functions properly as a system. Individually, each piece may...
shale oil extraction technology to convert kerogen
Kerogen
Kerogen is a mixture of organic chemical compounds that make up a portion of the organic matter in sedimentary rocks. It is insoluble in normal organic solvents because of the huge molecular weight of its component compounds. The soluble portion is known as bitumen. When heated to the right...
in oil shale
Oil shale
Oil shale, an organic-rich fine-grained sedimentary rock, contains significant amounts of kerogen from which liquid hydrocarbons called shale oil can be produced...
to shale oil
Shale oil
Shale oil, known also as kerogen oil or oil-shale oil, is an unconventional oil produced from oil shale by pyrolysis, hydrogenation, or thermal dissolution. These processes convert the organic matter within the rock into synthetic oil and gas...
. It is developed by the Shell Oil Company
Shell Oil Company
Shell Oil Company is the United States-based subsidiary of Royal Dutch Shell, a multinational oil company of Anglo Dutch origins, which is amongst the largest oil companies in the world. Approximately 22,000 Shell employees are based in the U.S. The head office in the U.S. is in Houston, Texas...
.
History
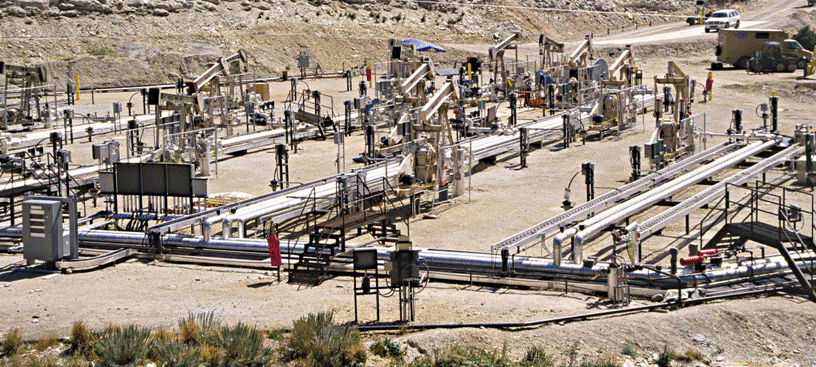
Colorado Western Slope
The Western Slope of Colorado refers to a region of the U.S. state of Colorado incorporating everything in the state west of the Continental Divide. The Colorado River and its tributaries divide the region into north and south at Grand Junction, Colorado...
in the Piceance Creek Basin
Piceance Basin
The Piceance Basin is a geologic structural basin in northwestern Colorado, in the United States. It includes geologic formations from Cambrian to Holocene in age, but the thickest section is made up of rocks from the Cretaceous Period...
. Since 2000, additional research and development activities have carried on as a part of the Mahogany Research Project. The oil shale heating at Mahogany started early 2004, and was completed mid-2005.
Process
The process heats sections of the vast oil shale field in situ, releasing the shale oil and oil shale gasOil shale gas
Oil shale gas is a synthetic gas mixture produced by oil shale pyrolysis. Although often referred to as shale gas, it differs from the natural gas produced from shale, which is also known as shale gas.-Process:...
from the rock so that it can be pumped to the surface and made into fuel
Fuel
Fuel is any material that stores energy that can later be extracted to perform mechanical work in a controlled manner. Most fuels used by humans undergo combustion, a redox reaction in which a combustible substance releases energy after it ignites and reacts with the oxygen in the air...
. In this process, a freeze wall is first to be constructed to isolate the processing area from surrounding groundwater. To maximize the functionality of the freeze walls, adjacent working zones will be developed in succession. 2000 feet (610 m) wells, eight feet apart, are drilled and filled with a circulating super-chilled liquid to cool the ground to -60 °F. Water is then removed from the working zone. Heating and recovery wells are drilled at 40 feet (12.2 m) intervals within the working zone. Electrical heating element
Heating element
A heating element converts electricity into heat through the process of Joule heating. Electric current through the element encounters resistance, resulting in heating of the element....
s are lowered into the heating wells and used to heat oil shale to between 650 °F (343.3 °C) and 700 °F (371.1 °C) over a period of approximately four years. Kerogen
Kerogen
Kerogen is a mixture of organic chemical compounds that make up a portion of the organic matter in sedimentary rocks. It is insoluble in normal organic solvents because of the huge molecular weight of its component compounds. The soluble portion is known as bitumen. When heated to the right...
in oil shale is slowly converted into shale oil and gases, which are then flow to the surface through recovery wells.
Energy consumption
A RAND study in 2005 estimated that production of 100000 oilbbl/d of oil (5.4 million tons/year) would theoretically require a dedicated power generating capacity of 1.2 gigawatts (10 billion kWh/year), assuming deposit richness of 25 gallons (94.6 l) per ton, with 100% pyrolysis efficiency, and 100% extraction of pyrolysis products. If this amount of electricity were to be generated by a coal-fired power plant, it would consume five million ton of coal annually (about 2.2 million toe).In 2006, Shell estimated that over the project life cycle, for every unit of energy consumed, three to four units would be produced. Such an "energy returned on energy invested" would be significantly better than that achieved in the Mahogony trials. For the 1996 trial, Shell applied 440,000 kWh (which would require about 96 toe energy input in a coal-fired plant), to generate 250 barrels (39,746.8 l) of oil (37 toe output).
Environmental impacts
Shell's underground conversion process requires significant development on the surface. The separation between drilled wells is less than five meters and wells must be connected by electrical wiring and by piping to storage and processing facilities. Shell estimates that the footprint of extraction operations would be similar to that for conventional oil and gas drilling. However, the dimensions of Shell's 2005 trial indicate that a much larger footprint is required. Production of 50,000 bbl/day would require that land be developed at a rate on the order of 1 square kilometre (0.386102158592535 sq mi) per year.Extensive water use and the risk of groundwater
Groundwater
Groundwater is water located beneath the ground surface in soil pore spaces and in the fractures of rock formations. A unit of rock or an unconsolidated deposit is called an aquifer when it can yield a usable quantity of water. The depth at which soil pore spaces or fractures and voids in rock...
pollution are the technology's greatest challenges.
Current implementations
In 2006, Shell received a Bureau of Land ManagementBureau of Land Management
The Bureau of Land Management is an agency within the United States Department of the Interior which administers America's public lands, totaling approximately , or one-eighth of the landmass of the country. The BLM also manages of subsurface mineral estate underlying federal, state and private...
lease to pursue a large demonstration with a capacity of 1500 oilbbl/d; Shell has since dropped those plans and is planning a test based on ICP that would produce a total of minimum 1500 barrels (238,480.9 l), together with nahcolite
Nahcolite
Nahcolite is a soft, colourless or white carbonate mineral with the composition of sodium bicarbonate also called thermokalite. It crystallizes in the monoclinic system....
, over a seven year period.
In Israel, IEI, a subsidiary of IDT Corp.
IDT Corp.
IDT Corporation is a telecommunications and energy company headquartered in Newark, New Jersey.-History:IDT was founded by entrepreneur Howard Jonas in August 1990...
is planning a shale pilot based on ICP technology. The project would produce a total of 1,500 barrels. However, IEI has also announced that any subsequent projects would not use ICP technology, but would instead utilize horizontal wells and hot gas heating methods.
In Jordan, Shell subsidiary JOSCO plans to use ICP technology to achieve commercial production by the "late 2020s." In October, 2011, it was reported that JOSCO had drilled more than 100 test holes over the prior two years, apparently for the sake of testing shale samples.