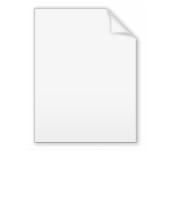
Metro Tunneling Group
Encyclopedia
Metro Tunneling Group is a Joint Venture of five companies:
1. Dywidag from Germany http://www.dywidag-international.com
2. L&T from India http://www.larsentoubro.com
3. Samsung from South Korea http://www.www.samsung.com.com
4. IRCON INTERNATIONAL LIMITED from India http://www.ircon.org
5. Shimizu from Japan http://www.shimz.co.jp
Currently working as the Main Contractor for the DMRC
On December 19, 2006, the international Joint Venture - Metro Tunneling Group received the Letter of Acceptance from Delhi Metro Rail Corporation for the Contract BC18.
The scope of work for the new contract includes the design and civil works for a 3.1 km long metro twin tunnel and two underground metro stations. Within the construction period of 36 month the tunnel will be built by Shield TBM whereas the stations will be constructed using the cut + cover method.
is the Joint Venture of Government of India and Government of Delhi.
Structure of DMRC:
1. Chairman - Shri M Ramachandran
2. Managing Director - Dr. E. Sreedharan
3. Total No. of Directors - 14
4. Nominee of Govt. of India - 5
5. Nominee of Govt. of NCTD - 5 (Including MD)
6. No. of full-time functional Directors at present including MD - 7
7. The corporate office of the company is located at IIIrd Floor, East Tower, NBCC Place, Pragati Vihar, Bhishma Pitahmah Marg, New Delhi - 110003.
In April 2001 the international Joint Venture “International Metro Civil Contractors” (IMCC) was awarded the contract for the design and construction of an approx. 6.5 km long underground section underneath the centre of Old and New Delhi.
The Joint Venture under the leadership of DYWIDAG International GmbH (Germany), together with Larsen & Toubro (India), Samsung Corporation (Korea), IRCON International (India) and Shimizu Corporation (Japan), who successfully completed the turn-key contract MC 1B for a 6.5 km metro twin tunnel system and 6 metro stations of the extension of the Metro Delhi in June 2005, 8 months ahead of the originally scheduled termination date.
During the phase I of the Delhi Metro, the JV has completed the Rs 1,940-crore plan of underground Metro Rail Corridor from Central Secretariat to Kashmiri Gate.
The scope of work of this US$ 380 m contract consists of a twin tunnel system including six underground stations, of which five are open-cut stations and one station in tunnel using New Austrian Tunneling method (NATM). To complete the seven km bored tunnel sections between stations, the Joint Venture has bought three Herrenknecht tunnel boring machine
s – two earth pressure balance machines (EPBM) and one hard rock shield machine. The first machine was launched in March 2002.
Whilst most of the project lies in the Delhi Silts, the section in the area of Old Delhi is situated in the bedrock, which rises up to almost ground level. Because of these ground conditions and the extremely congested locality, the 300 m long Chawri Bazar Station in the centre of Old Delhi cannot be constructed by open-cut, but must be excavated exclusively using the NATM. This is done from an access shaft, 25 x 40 m, with four NATM drives, with a diameter of 10 m each. All are progressing simultaneously parallel to the works for the shaft building, using both hydraulic excavators and smooth blasting techniques.
During the entire tunneling activities ground movements have been documented and controlled using an extensive monitoring programme installed both inside the tunnels and above ground. A large number of specialized instruments have been installed to monitor ground movements and strains in the surrounding structures.
In addition to civil and structural works the design-build contract also includes station air conditioning, tunnel ventilation, station E&M services, lighting, station finishes and landscaping.
Source: DYWIDAG International GmbH http://www.dywidag-international.com/en/projects/references/india_delhi_metropolitan/index.html
To provide a permanent alignment for the grab, To prevent the collapsing of soil near the surface, To provide the temporary supports for the reinforcing steel cage, To provide a support for suspending the stop - end joint.
Guide walls shall be constructed prior to the excavation of the diaphragm wall and shall be made from M20 reinforced concrete. The distance between guide walls shall be 800+50 (mm), 1000+50 (mm) and 1200 + 50(mm).
The guide wall will be constructed in such a way that the inner guide wall trench face shall be in exact alignment as the inner side of the Diaphragm Wall. The outer side of the guide wall will be constructed at distance equivalent to the Diaphragm Wall thickness plus tolerance of 50 mm.
Special care will be taken to ensure that the trench face of the guide wall is truly vertical & that there are no ridges or abrupt changes. Plywood shutters of required size shall be used to form a continuous wall to guide the operating grab at the ground level.
The spacing shall be maintained at 850 mm for 800mm thick (for 1000mm thick DW, the spacing shall be 1050mm and for 1200 mm thick DW, the spacing shall be 1250 mm) and shutters shall be kept vertical by checking with plumb bob and strutting the shutters accordingly.
After 3 days curing of the concrete in the Guide Wall, the inside space shall be filled with excavated soil and compacted by hammers.
Basically GW will be inverted “L” shape, whereas the horizontal leg is 600mm long and the vertical leg is 1500mm. The depth of Guide Wall as specified can ensure that the Grab moves vertically as the GW acts as a template for movement of grab.
The inner side of Grab shall be vertical. The shuttering shall be checked for alignment and verticality before concreting. Guide Wall design drawings are placed at attachments
) was first launched by IMCC in India.
TBM Main Drive:
Total length of tunnel section is 3.14 km.
1. Dywidag from Germany http://www.dywidag-international.com
2. L&T from India http://www.larsentoubro.com
3. Samsung from South Korea http://www.www.samsung.com.com
4. IRCON INTERNATIONAL LIMITED from India http://www.ircon.org
5. Shimizu from Japan http://www.shimz.co.jp
Currently working as the Main Contractor for the DMRC
On December 19, 2006, the international Joint Venture - Metro Tunneling Group received the Letter of Acceptance from Delhi Metro Rail Corporation for the Contract BC18.
The scope of work for the new contract includes the design and civil works for a 3.1 km long metro twin tunnel and two underground metro stations. Within the construction period of 36 month the tunnel will be built by Shield TBM whereas the stations will be constructed using the cut + cover method.
DMRC
DMRCDelhi Metro
Delhi Metro is a rapid transit system serving Delhi, Gurgaon, Noida and Ghaziabad in the National Capital Region of India. It is one of the largest metro networks in the world. The network consists of six lines with a total length of with 142 stations of which 35 are underground...
is the Joint Venture of Government of India and Government of Delhi.
Structure of DMRC:
1. Chairman - Shri M Ramachandran
2. Managing Director - Dr. E. Sreedharan
3. Total No. of Directors - 14
4. Nominee of Govt. of India - 5
5. Nominee of Govt. of NCTD - 5 (Including MD)
6. No. of full-time functional Directors at present including MD - 7
7. The corporate office of the company is located at IIIrd Floor, East Tower, NBCC Place, Pragati Vihar, Bhishma Pitahmah Marg, New Delhi - 110003.
What is IMCC ?
MTG previously known as IMCC (International Metro Civil Contractors).In April 2001 the international Joint Venture “International Metro Civil Contractors” (IMCC) was awarded the contract for the design and construction of an approx. 6.5 km long underground section underneath the centre of Old and New Delhi.
The Joint Venture under the leadership of DYWIDAG International GmbH (Germany), together with Larsen & Toubro (India), Samsung Corporation (Korea), IRCON International (India) and Shimizu Corporation (Japan), who successfully completed the turn-key contract MC 1B for a 6.5 km metro twin tunnel system and 6 metro stations of the extension of the Metro Delhi in June 2005, 8 months ahead of the originally scheduled termination date.
During the phase I of the Delhi Metro, the JV has completed the Rs 1,940-crore plan of underground Metro Rail Corridor from Central Secretariat to Kashmiri Gate.
The scope of work of this US$ 380 m contract consists of a twin tunnel system including six underground stations, of which five are open-cut stations and one station in tunnel using New Austrian Tunneling method (NATM). To complete the seven km bored tunnel sections between stations, the Joint Venture has bought three Herrenknecht tunnel boring machine
Tunnel boring machine
A tunnel boring machine also known as a "mole", is a machine used to excavate tunnels with a circular cross section through a variety of soil and rock strata. They can bore through anything from hard rock to sand. Tunnel diameters can range from a metre to almost 16 metres to date...
s – two earth pressure balance machines (EPBM) and one hard rock shield machine. The first machine was launched in March 2002.
Whilst most of the project lies in the Delhi Silts, the section in the area of Old Delhi is situated in the bedrock, which rises up to almost ground level. Because of these ground conditions and the extremely congested locality, the 300 m long Chawri Bazar Station in the centre of Old Delhi cannot be constructed by open-cut, but must be excavated exclusively using the NATM. This is done from an access shaft, 25 x 40 m, with four NATM drives, with a diameter of 10 m each. All are progressing simultaneously parallel to the works for the shaft building, using both hydraulic excavators and smooth blasting techniques.
During the entire tunneling activities ground movements have been documented and controlled using an extensive monitoring programme installed both inside the tunnels and above ground. A large number of specialized instruments have been installed to monitor ground movements and strains in the surrounding structures.
In addition to civil and structural works the design-build contract also includes station air conditioning, tunnel ventilation, station E&M services, lighting, station finishes and landscaping.
Source: DYWIDAG International GmbH http://www.dywidag-international.com/en/projects/references/india_delhi_metropolitan/index.html
Diaphragm Wall
It is a wall constructed with the help of rebar and concrete. Scope of works includes construction of guide walls, trench excavation under Bentonite, placing of reinforcement and concreting of diaphragm wall panels.Construction of Guide Wall
The purpose of guide walls is:To provide a permanent alignment for the grab, To prevent the collapsing of soil near the surface, To provide the temporary supports for the reinforcing steel cage, To provide a support for suspending the stop - end joint.
Guide walls shall be constructed prior to the excavation of the diaphragm wall and shall be made from M20 reinforced concrete. The distance between guide walls shall be 800+50 (mm), 1000+50 (mm) and 1200 + 50(mm).
The guide wall will be constructed in such a way that the inner guide wall trench face shall be in exact alignment as the inner side of the Diaphragm Wall. The outer side of the guide wall will be constructed at distance equivalent to the Diaphragm Wall thickness plus tolerance of 50 mm.
Special care will be taken to ensure that the trench face of the guide wall is truly vertical & that there are no ridges or abrupt changes. Plywood shutters of required size shall be used to form a continuous wall to guide the operating grab at the ground level.
The spacing shall be maintained at 850 mm for 800mm thick (for 1000mm thick DW, the spacing shall be 1050mm and for 1200 mm thick DW, the spacing shall be 1250 mm) and shutters shall be kept vertical by checking with plumb bob and strutting the shutters accordingly.
After 3 days curing of the concrete in the Guide Wall, the inside space shall be filled with excavated soil and compacted by hammers.
Basically GW will be inverted “L” shape, whereas the horizontal leg is 600mm long and the vertical leg is 1500mm. The depth of Guide Wall as specified can ensure that the Grab moves vertically as the GW acts as a template for movement of grab.
The inner side of Grab shall be vertical. The shuttering shall be checked for alignment and verticality before concreting. Guide Wall design drawings are placed at attachments
What is TBM ?
TBM (Tunel Boring MachineTunnel boring machine
A tunnel boring machine also known as a "mole", is a machine used to excavate tunnels with a circular cross section through a variety of soil and rock strata. They can bore through anything from hard rock to sand. Tunnel diameters can range from a metre to almost 16 metres to date...
) was first launched by IMCC in India.
Sequence of Tunneling Assembly
For starting the tunneling, the Tunnel Boring Machine (TBM) are required to be placed at tunnel axis level. A launching shaft of 60 X 23 m area was made at the north end of the station to lawer down and assembly the TBMs. The launching shaft either supported by bored piles with shotcrete in between or by Diaphragm Wall.Current Project
The Company is currently executing the Metro Project from Green Park to Saket (Phase II) - BC 18.TBM Main Drive:
- Malviya Nagar Station to Hauz Khas Station - 1454 M
- Hauz Khas Station to Green Park - 983 M
- Malviya Nagar to Saket - 716 M
Total length of tunnel section is 3.14 km.