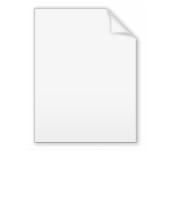
Petrosix
Encyclopedia
Petrosix is currently the world’s largest surface oil shale
pyrolysis
retort with an 11 metres (36 ft) diameter vertical shaft kiln
, operational since 1992. It is located in São Mateus do Sul
, Brazil
, and it is owned and operated by the Brazil energy company Petrobras
. Petrosix means also the Petrosix process, an externally generated hot gas technology of shale oil extraction. The technology is tailored to Irati
oil shale formation, a Permian
formation of the Paraná Basin
.
s per day, was brought on line in 1972, and began limited commercial operation in 1980. The first retort that used current Petrosix technology was a 0.2 metre (0.656167979002625 ft) internal diameter retort pilot plant started in 1982. It was followed by a 2 metres (6.6 ft) retort demonstration plant in 1984. A 11 metres (36 ft) retort was brought into service in December 1991, and commercial production started in 1992. At present, the company operates two retorts which process 8,500 tons of oil shale daily.
(i.e., 550 tons of oil, approximately 1 ton of oil per 11 tons of shale), as well as 132 tons of oil shale gas
, 50 tons of liquefied oil shale gas, and 82 tons of sulfur.
in the shale decomposes to yield oil vapor and more gas. Cold gas is injected into the bottom of the retort to cool and recover heat from the spent shale. Cooled spent shale is discharged through a water seal with drag conveyor below the retort. Oil mist and cooled gases are removed through the top of the retort and enter a wet electrostatic precipitator
where the oil droplets are coalesced and collected. The gas from the precipitator is compressed and split into three parts.
One part of the compressed retort gas is heated in a furnace to 600 °C (1,112 °F) and recirculated back to the middle of the retort for heating and pyrolyzing the oil shale, and another part is circulated cold into the bottom of the retort, where it cools down the spent shale, heats up itself, and ascends into the pyrolysis section as a supplementary heat source for heating the oil shale. The third part undergoes further cooling for light oil (naphtha) and water removal and then sent to the gas treatment unit, where fuel gas and liquefied petroleum gas (LPG) are produced and sulfur recovered.
One drawback of this process is that the potential heat from the combustion of the char contained in the shale is not utilized. Also oil shale particles smaller than 12 millimetre (0.47244094488189 in) can not be processed in the Petrosix retort. These fines may account for 10 to 30 per cent of the crushed feed.
Oil shale
Oil shale, an organic-rich fine-grained sedimentary rock, contains significant amounts of kerogen from which liquid hydrocarbons called shale oil can be produced...
pyrolysis
Pyrolysis
Pyrolysis is a thermochemical decomposition of organic material at elevated temperatures without the participation of oxygen. It involves the simultaneous change of chemical composition and physical phase, and is irreversible...
retort with an 11 metres (36 ft) diameter vertical shaft kiln
Kiln
A kiln is a thermally insulated chamber, or oven, in which a controlled temperature regime is produced. Uses include the hardening, burning or drying of materials...
, operational since 1992. It is located in São Mateus do Sul
São Mateus do Sul
São Mateus do Sul is a town and municipality in the state of Paraná in the Southern Region of Brazil.-References:...
, Brazil
Brazil
Brazil , officially the Federative Republic of Brazil , is the largest country in South America. It is the world's fifth largest country, both by geographical area and by population with over 192 million people...
, and it is owned and operated by the Brazil energy company Petrobras
Petrobras
Petróleo Brasileiro or Petrobras is a semi-public Brazilian multinational energy corporation headquartered in Rio de Janeiro, Brazil. It is the largest company in Latin America by market capitalization and revenue, and the largest company headquartered in the Southern Hemisphere by market...
. Petrosix means also the Petrosix process, an externally generated hot gas technology of shale oil extraction. The technology is tailored to Irati
Irati
Irati is a town in State of Paraná, Brazil with an estimated population 54,805 in 2006 based on the 2000 censusIrati sprang up in the 1890s as a railroad town along the São Paulo–Rio Grande do Sul railroad line...
oil shale formation, a Permian
Permian
The PermianThe term "Permian" was introduced into geology in 1841 by Sir Sir R. I. Murchison, president of the Geological Society of London, who identified typical strata in extensive Russian explorations undertaken with Edouard de Verneuil; Murchison asserted in 1841 that he named his "Permian...
formation of the Paraná Basin
Parana Basin
The Paraná Basin is a large sedimentary basin situated in the central-eastern part of South America. About 75% of its areal distribution occurs in Brazil, from Mato Grosso to Rio Grande do Sul states. The remainder area is distributed in eastern Paraguay, northeastern Argentina and northern...
.
History
Petrobras started oil shale processing activities in 1953 by developing Petrosix technology for extracting oil from oil shale of the Irati formation. A 5.5 metres (18 ft) inside diameter semi-works retort (the Irati Profile Plant) with capacity of 2,400 tonTon
The ton is a unit of measure. It has a long history and has acquired a number of meanings and uses over the years. It is used principally as a unit of weight, and as a unit of volume. It can also be used as a measure of energy, for truck classification, or as a colloquial term.It is derived from...
s per day, was brought on line in 1972, and began limited commercial operation in 1980. The first retort that used current Petrosix technology was a 0.2 metre (0.656167979002625 ft) internal diameter retort pilot plant started in 1982. It was followed by a 2 metres (6.6 ft) retort demonstration plant in 1984. A 11 metres (36 ft) retort was brought into service in December 1991, and commercial production started in 1992. At present, the company operates two retorts which process 8,500 tons of oil shale daily.
Retort
The Petrosix 11 metres (36.1 ft) vertical shaft retort is the world's largest operational surface oil shale pyrolysis reactor. It was designed by Cameron Engineers. The retort has the upper pyrolysis section and lower shale coke cooling section. The retort capacity is 6,200 tons of oil shale per day, and it yields a nominal daily output of 3,870 barrels of shale oilShale oil
Shale oil, known also as kerogen oil or oil-shale oil, is an unconventional oil produced from oil shale by pyrolysis, hydrogenation, or thermal dissolution. These processes convert the organic matter within the rock into synthetic oil and gas...
(i.e., 550 tons of oil, approximately 1 ton of oil per 11 tons of shale), as well as 132 tons of oil shale gas
Oil shale gas
Oil shale gas is a synthetic gas mixture produced by oil shale pyrolysis. Although often referred to as shale gas, it differs from the natural gas produced from shale, which is also known as shale gas.-Process:...
, 50 tons of liquefied oil shale gas, and 82 tons of sulfur.
Process
Petrosix is one of fives technologies of shale oil extraction, which is currently in commercial use. It is an above-ground retorting technology, which uses externally generated hot gas for the oil shale pyrolysis. After mining, the shale is transported by trucks to a crusher and screens, where it is reduced to particles (lump shale). These particles are between 12 millimetre (0.47244094488189 in) and 75 millimetres (3 in) and have an approximately parallelepipedic shape. These particles are transported on a belt to a vertical cylindrical vessel, where the shale is heated up to about 500 °C (932 °F) for pyrolysis. Oil shale enters through the top of the retort while hot gases are injected into the middle of the retort. The oil shale is heated by the gases as it moves down. As a result, the kerogenKerogen
Kerogen is a mixture of organic chemical compounds that make up a portion of the organic matter in sedimentary rocks. It is insoluble in normal organic solvents because of the huge molecular weight of its component compounds. The soluble portion is known as bitumen. When heated to the right...
in the shale decomposes to yield oil vapor and more gas. Cold gas is injected into the bottom of the retort to cool and recover heat from the spent shale. Cooled spent shale is discharged through a water seal with drag conveyor below the retort. Oil mist and cooled gases are removed through the top of the retort and enter a wet electrostatic precipitator
Electrostatic precipitator
An electrostatic precipitator , or electrostatic air cleaner is a particulate collection device that removes particles from a flowing gas using the force of an induced electrostatic charge...
where the oil droplets are coalesced and collected. The gas from the precipitator is compressed and split into three parts.
One part of the compressed retort gas is heated in a furnace to 600 °C (1,112 °F) and recirculated back to the middle of the retort for heating and pyrolyzing the oil shale, and another part is circulated cold into the bottom of the retort, where it cools down the spent shale, heats up itself, and ascends into the pyrolysis section as a supplementary heat source for heating the oil shale. The third part undergoes further cooling for light oil (naphtha) and water removal and then sent to the gas treatment unit, where fuel gas and liquefied petroleum gas (LPG) are produced and sulfur recovered.
One drawback of this process is that the potential heat from the combustion of the char contained in the shale is not utilized. Also oil shale particles smaller than 12 millimetre (0.47244094488189 in) can not be processed in the Petrosix retort. These fines may account for 10 to 30 per cent of the crushed feed.
See also
- Galoter processGaloter processThe Galoter process is a shale oil extraction technology for a production of shale oil, a type of synthetic crude oil. In this process, the oil shale is decomposed into shale oil, oil shale gas, and spent residue...
- Alberta Taciuk ProcessAlberta Taciuk ProcessThe Alberta Taciuk process is an above-ground dry thermal retorting technology for extracting oil from oil sands, oil shale and other organics-bearing materials, including oil contaminated soils, sludges and wastes...
- Kiviter processKiviter process-History:The Kiviter process is based on the earlier vertical retort technology . This technology underwent a long process of development...
- TOSCO II processTOSCO II processThe TOSCO II process is an above ground retorting technology for shale oil extraction, which uses fine particles of oil shale that are heated in a rotating kiln. The particularity of this process is that it use hot ceramic balls for the heat transfer between the retort and a heater...
- Fushun processFushun processThe Fushun process is an above-ground retorting technology for shale oil extraction. It is named after the main production site of Fushun, Liaoning province in northeastern China.-History:...
- Paraho processParaho processThe Paraho process is an above ground retorting technology for shale oil extraction. The name "Paraho" is delivered from the words "para homem", which means in Portuguese "for mankind".-History:...
- Lurgi-Ruhrgas processLurgi-Ruhrgas processThe Lurgi–Ruhrgas process is an above-ground coal liquefaction and shale oil extraction technology. It is classified as a hot recycled solids technology.-History:...
- Paraná BasinParana BasinThe Paraná Basin is a large sedimentary basin situated in the central-eastern part of South America. About 75% of its areal distribution occurs in Brazil, from Mato Grosso to Rio Grande do Sul states. The remainder area is distributed in eastern Paraguay, northeastern Argentina and northern...