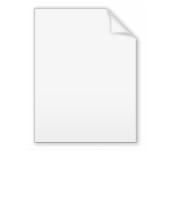
Reinforced rubber
Encyclopedia
Although seldom shared under this name, one of the largest groups of composite materials worldwide is that of the reinforced rubber products. Familiar examples are automobile tyres, hoses and conveyor belts.
matrix and a reinforcing material, so high strength to flexibility ratios can be achieved. The reinforcing material, usually a kind of fibre, provides the strength and stiffness. The rubber matrix, with low strength and stiffness, provides air-fluid tightness and supports the reinforcing materials to maintain their relative positions. These positions are of great importance because they influence the resulting mechanical properties.
path connects two arbitrary points on a continuous surface by means of the shortest possible way.
To achieve optimal loading in a straight rubber hose
the fibres must be positioned under an angle of approximately 54.7 angular degrees, also referred to as the magic angle
. In this situation the fibres are only loaded on tensile strength so they can use 100% of their strength to take up the forces acting on the hose due to the internal pressure. (The magic angle for cylindrical shapes of 54.7 angular degrees is based on calculations in which the influence of the matrix material is neglected. Therefore, depending on the stiffness of the rubber material used, the actual neutral angle can vary a few degrees from the magic angle.)
When the fibres of the reinforcement structure are placed under angles larger than 54.7 angular degrees, the fibres want to relocate to their optimal path when pressurized. This means that the fibres will re-orient themselves until they have reached their force equilibrium. In this case this will lead to an increase in length and a decrease in diameter. With angles smaller than 54.7 degrees the opposite will occur. A product which makes use of this principle is a pneumatic muscle.
Composite reinforced structure
Reinforced rubber products combine a rubberRubber
Natural rubber, also called India rubber or caoutchouc, is an elastomer that was originally derived from latex, a milky colloid produced by some plants. The plants would be ‘tapped’, that is, an incision made into the bark of the tree and the sticky, milk colored latex sap collected and refined...
matrix and a reinforcing material, so high strength to flexibility ratios can be achieved. The reinforcing material, usually a kind of fibre, provides the strength and stiffness. The rubber matrix, with low strength and stiffness, provides air-fluid tightness and supports the reinforcing materials to maintain their relative positions. These positions are of great importance because they influence the resulting mechanical properties.
Optimal loading condition
A composite structure where all fibres are loaded equally everywhere when pressurized, is called an isotropic structure and the type of loading is named an isotensoidal loading. To meet the isotensoidal concept the structure geometry must have an isotensoid meridian profile and the fibres must be positioned following geodesic paths. A geodesicGeodesic
In mathematics, a geodesic is a generalization of the notion of a "straight line" to "curved spaces". In the presence of a Riemannian metric, geodesics are defined to be the shortest path between points in the space...
path connects two arbitrary points on a continuous surface by means of the shortest possible way.
Straight rubber hoses
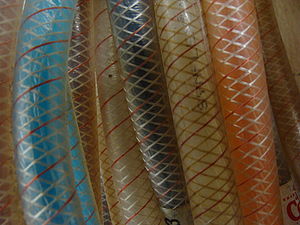
Hose
A hose is a hollow tube designed to carry fluids from one location to another. Hoses are also sometimes called pipes , or more generally tubing...
the fibres must be positioned under an angle of approximately 54.7 angular degrees, also referred to as the magic angle
Magic angle
The magic angle is a precisely defined angle, the value of which is approximately 54.7356°. The magic angle is a root of a second-order Legendre polynomial, P_2=0 \,, and so any interaction which depends on this second-order Legendre polynomial vanishes at the magic angle...
. In this situation the fibres are only loaded on tensile strength so they can use 100% of their strength to take up the forces acting on the hose due to the internal pressure. (The magic angle for cylindrical shapes of 54.7 angular degrees is based on calculations in which the influence of the matrix material is neglected. Therefore, depending on the stiffness of the rubber material used, the actual neutral angle can vary a few degrees from the magic angle.)
When the fibres of the reinforcement structure are placed under angles larger than 54.7 angular degrees, the fibres want to relocate to their optimal path when pressurized. This means that the fibres will re-orient themselves until they have reached their force equilibrium. In this case this will lead to an increase in length and a decrease in diameter. With angles smaller than 54.7 degrees the opposite will occur. A product which makes use of this principle is a pneumatic muscle.