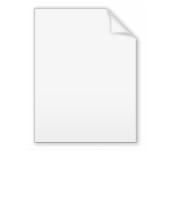
Rotary piercing
Encyclopedia
Rotary piercing is a hot working
metalworking
process for forming thick-walled seamless tubing. There are two types: the Mannesmann process and Stiefel process.
's longitudinal axis. The rollers are on opposite sides of the billet and the surface of their largest cross sections are separated by a distance slightly smaller than the outer diameter (OD) of the original billet. The load imparted by the rollers compresses the material and the 6° skew provides both rotation and translation to the billet. The friction from between the rollers and the billet is intentionally high and many times increased with knurling of the rollers. This friction sets up stresses
varying radially through the billet cross section with the highest stresses are at the OD and the central axis. The stress exceeds the yield strength of the billet and cause circumferential fissures to propagate at various radii near the OD and a central longitudinal void to form at the axis. A tapered mandrel
is set inside and a short distance from the start of the central void. This mandrel forces the material outward and compresses the material against the back side of the tapered rollers. This compressive loading fuses the various circumferential fissures and sets the initial internal diameter and OD values. The newly formed tube is then cooled and can be cold worked to further refine the diameters and to gain the desired yield strengths.
Mannesmann mills can produce tubes as large as 300 mm (12 in) in diameter.
Hot working
Hot working refers to processes where metals are plastically deformed above their recrystallization temperature. Being above the recrystallization temperature allows the material to recrystallize during deformation. This is important because recrystallization keeps the materials from strain...
metalworking
Metalworking
Metalworking is the process of working with metals to create individual parts, assemblies, or large scale structures. The term covers a wide range of work from large ships and bridges to precise engine parts and delicate jewelry. It therefore includes a correspondingly wide range of skills,...
process for forming thick-walled seamless tubing. There are two types: the Mannesmann process and Stiefel process.
Mannesmann process
A heated cylindrical billet is fed between two convex-tapered rollers, which are rotating in the same direction. The rollers are usually 6° askew from parallel with the billetBillet (manufacturing)
Semi-finished casting products are intermediate castings produced in a foundry that need further processing before being a finished good. There are four types: ingots, billets, blooms, and slabs.-Ingot:...
's longitudinal axis. The rollers are on opposite sides of the billet and the surface of their largest cross sections are separated by a distance slightly smaller than the outer diameter (OD) of the original billet. The load imparted by the rollers compresses the material and the 6° skew provides both rotation and translation to the billet. The friction from between the rollers and the billet is intentionally high and many times increased with knurling of the rollers. This friction sets up stresses
Stress (physics)
In continuum mechanics, stress is a measure of the internal forces acting within a deformable body. Quantitatively, it is a measure of the average force per unit area of a surface within the body on which internal forces act. These internal forces are a reaction to external forces applied on the body...
varying radially through the billet cross section with the highest stresses are at the OD and the central axis. The stress exceeds the yield strength of the billet and cause circumferential fissures to propagate at various radii near the OD and a central longitudinal void to form at the axis. A tapered mandrel
Mandrel
A mandrel is one of the following:* an object used to shape machined work.* a tool component that grips or clamps materials to be machined.* a tool component that can be used to grip other moving tool components.- Variants :...
is set inside and a short distance from the start of the central void. This mandrel forces the material outward and compresses the material against the back side of the tapered rollers. This compressive loading fuses the various circumferential fissures and sets the initial internal diameter and OD values. The newly formed tube is then cooled and can be cold worked to further refine the diameters and to gain the desired yield strengths.
Mannesmann mills can produce tubes as large as 300 mm (12 in) in diameter.