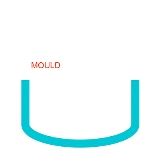
Rotational molding
Encyclopedia
Rotational molding, also known as rotomolding, rotocasting or spin casting, is a molding
process for creating many kinds of mostly hollow items, typically of plastic
.
A heated hollow mold is filled with a charge or shot weight of material, it is then slowly rotated (usually around two perpendicular axes) causing the softened material to disperse and stick to the walls of the mold. In order to maintain even thickness throughout the part, the mold continues to rotate at all times during the heating phase and to avoid sagging or deformation also during the cooling phase. The process was applied to plastics in the 1940s but in the early years was little used because it was a slow process restricted to a small number of plastics. Over the past two decades, improvements in process control and developments with plastic powders have resulted in a significant increase in usage.
Plastics were introduced to the rotational molding process in the early 1950s. One of the first applications was to manufacture doll heads. The machinery was made of an E Blue box-oven machine, inspired by a General Motors rear axle, powered by an external electric motor and heated by floor-mounted gas burners. The mold was made out of electroformed nickel-copper, and the plastic was a liquid PVC plastisol
. The cooling method consisted of placing the mold into cold water. This process of rotational molding led to the creation of other plastic toys. As demand and popularity of this process increased, it was used to create other products such as road cones, marine buoys, and car armrests. This popularity led to the development of larger machinery. A new system of heating was also created, going from the original direct gas jets to the current indirect high velocity air system. In Europe during the 1960s the Engel process was developed. This allowed the creation of large hollow containers to be created in low-density polyethylene. The cooling method consisted of turning off the burners and allowing the plastic to harden while still rocking in the mold.
In 1976, the Association of Rotational Moulders (ARM) was started in Chicago as a worldwide trade association. The main objective of this association is to increase awareness of the rotational molding technology and process.
In the 1980s, new plastics, such as polycarbonate
, polyester
, and nylon, were introduced to rotational molding. This has led to new uses for this process, such as the creation of fuel tanks and industrial moldings. The research that has been done since the late 1980s at Queen's University Belfast has led to the development of more precise monitoring and control of the cooling processes based on their development of the “Rotolog system”.
Molds (or tooling) are either fabricated from welded sheet steel or cast. The fabrication method is often driven by part size and complexity; most intricate parts are likely made out of cast tooling. Molds are typically manufactured from stainless steel
or aluminum. Aluminum molds are usually much thicker than an equivalent steel mold, as it is a softer metal. This thickness does not affect cycle times significantly since aluminum's thermal conductivity is many times greater than steel. Due to the need to develop a model prior to casting, cast molds tend to have additional costs associated with the manufacturing of the tooling, whereas fabricated steel or aluminum molds, particularly when used for less complex parts, are less expensive. However, some molds contain both aluminum and steel. This allows for variable thicknesses in the walls of the product. While this process is not as precise as injection molding
, it does provide the designer with more options. The aluminum addition to the steel provides more heat capacity
, causing the melt-flow to stay in a fluid state for a longer period.
Critics of the process point to its long cycle times—only one or two cycles an hour can typically occur, as opposed to other processes such as injection molding, where parts can be made in a few seconds. The process does have distinct advantages. Manufacturing large, hollow parts such as oil tanks is much easier by rotational molding than any other method. Rotational molds are significantly cheaper than other types of mold. Very little material is wasted using this process, and excess material can often be re-used, making it a very economically and environmentally viable manufacturing process.
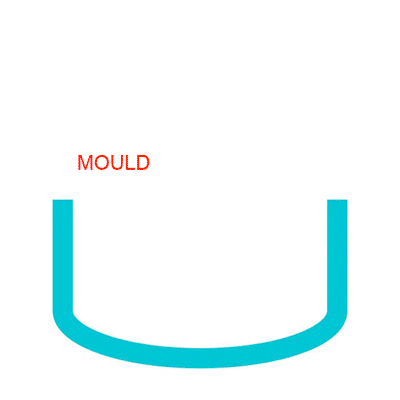
The rotational molding process consists of four distinct phases:
Much of the current research is into reducing the cycle time, as well as improving part quality. The most promising area is in mold pressurization. It is well known that applying a small amount of pressure internally to the mold at the correct point in the heating phase accelerates coalescence of the polymer particles during the melting, producing a part with fewer bubbles in less time than at atmospheric pressure
. This pressure delays the separation of the part from the mold wall due to shrinkage during the cooling phase, aiding cooling of the part. The main drawback to this is the danger to the operator of explosion of a pressurized part. This has prevented adoption of mold pressurization on a large scale by rotomolding manufacturers.
, nylons, and polypropylene
.
Order of materials most commonly used by industry :
These materials are also occasionally used (not in order of most used)::
composite can be created which is 80% natural non-processed material.
Rotational molding of plaster
is used to produce hollow statuettes.
Chocolate is rotationally molded to form hollow treats.
Designers can select the best material for their application, including materials that meet U.S. Food and Drug Administration (FDA) requirements. Additives for weather resistance, flame retardation, or static elimination can be incorporated.
Inserts, threads, handles, minor undercuts
, flat surfaces without draft angles, or fine surface detail can be part of the design. Designs can also be multi-wall, either hollow or foam filled.
Products that can be manufactured using rotational molding include storage tanks, bins and refuse containers,airplane parts, doll parts, road cones, footballs, helmets, rowing boats and kayak hulls. Playground slides and roofs are also generally rotomolded.
Another consideration is of structural support ribs. While solid ribs may be desirable and achievable in injection molding and other processes, a hollow rib is the best solution in rotational molding. A solid rib may be achieved through inserting a finished piece in the mold but this adds cost.
Rotational molding excels at producing hollow parts. However, care must be taken when this is done. When the depth of the recess is greater than the width there may be problems with even heating and cooling. Additionally, enough room must be left between the parallel walls to allow for the melt-flow to properly move throughout the mold. Otherwise webbing may occur. A desirable parallel wall scenario would have a gap at least three times the nominal wall thickness, with five times the nominal wall thickness being optimal. Sharp corners for parallel walls must also be considered. With angles of less than 45° bridging, webbing, and voids may occur.
, will require larger radii than other materials. Additionally, the stiffness of the set material may be a factor. More structural and strengthening measures may be required when a flimsy material is used.
, meaning they require different times in the heating chamber and cooling chamber. Ideally, the part will be tested to use the minimum thickness required for the application. This minimum will then be established as a nominal thickness.
For the designer, while variable thicknesses are possible, a process called stop rotation is required. This process is limited in that only one side of the mold may be thicker than the others. After the mold is rotated and all the surfaces are sufficiently coated with the melt-flow, the rotation stops and the melt-flow is allowed to pool at the bottom of the mold cavity.
Wall thickness is important for corner radii as well. Large outside radii are preferable to small radii. Large inside radii are also preferable to small inside radii. This allows for a more even flow of material and a more even wall thickness. However, an outside corner is generally stronger than an inside corner.
The process also has inherent design strengths, such as consistent wall thickness and strong outside corners that are virtually stress free. For additional strength, reinforcing ribs can be designed into the part. Along with being designed into the part, they can be added to the mold.
The ability to add prefinished pieces to the mold alone is a large advantage. Metal threads, internal pipes and structures, and even different colored plastics can all be added to the mold prior to the addition of plastic pellets. However, care must be taken to ensure that minimal shrinkage while cooling will not damage the part. This shrinking allows for mild undercuts and negates the need for ejection mechanisms (in most pieces).
Another advantage lies in the molds themselves. Since they require less tooling, they can be manufactured and put into production much more quickly than other molding processes. This is especially true for complex parts, which may require large amounts of tooling for other molding processes. Rotational molding is also the desired process for short runs and rush deliveries. The molds can be swapped quickly or different colors can be used without purging the mold. With other processes, purging may be required to swap colors.
Due to the uniform thicknesses achieved, large stretched sections are nonexistent, which makes large thin panels possible (although warping may occur). Also, there is little flow of plastic (stretching) but rather a placing of the material within the part. These thin walls also limit cost and production time.
Another cost limiting factor is the amount of material wasted in production. There are no sprues or runners (as in injection molding), no off-cuts (thermoforming), or pinch off scrap (blow molding). What material is wasted, through scrap or failed part testing, can usually be recycled.
Another limitation lies in the molds themselves. Unlike other processes where only the product needs to be cooled before being removed, with rotational molding the entire mold must be cooled. While water cooling processes are possible, there is still a significant down time of the mold. Additionally, this increases both financial and environmental costs. Some plastics will degrade with the long heating cycles or in the process of turning them into a powder to be melted.
Molding (process)
Molding or moulding is the process of manufacturing by shaping pliable raw material using a rigid frame or model called a pattern....
process for creating many kinds of mostly hollow items, typically of plastic
Plastic
A plastic material is any of a wide range of synthetic or semi-synthetic organic solids used in the manufacture of industrial products. Plastics are typically polymers of high molecular mass, and may contain other substances to improve performance and/or reduce production costs...
.
A heated hollow mold is filled with a charge or shot weight of material, it is then slowly rotated (usually around two perpendicular axes) causing the softened material to disperse and stick to the walls of the mold. In order to maintain even thickness throughout the part, the mold continues to rotate at all times during the heating phase and to avoid sagging or deformation also during the cooling phase. The process was applied to plastics in the 1940s but in the early years was little used because it was a slow process restricted to a small number of plastics. Over the past two decades, improvements in process control and developments with plastic powders have resulted in a significant increase in usage.
History
In 1855 R. Peters of Britain documented the first use of biaxial rotation and heat. This rotational molding process was used to create metal artillery shells and other hollow vessels. The main purpose of using rotational molding was to create consistency in wall thickness and density. In 1905 in the United States F.A. Voelke used this method for the hollowing of wax objects. This led to G.S. Baker's and G.W. Perks's process of making hollow chocolate eggs in 1910. Rotational molding developed further and R.J. Powell used this process for molding plaster of Paris in the 1920s. These early methods using different materials directed the advancements in the way rotational molding is used today with plastics.Plastics were introduced to the rotational molding process in the early 1950s. One of the first applications was to manufacture doll heads. The machinery was made of an E Blue box-oven machine, inspired by a General Motors rear axle, powered by an external electric motor and heated by floor-mounted gas burners. The mold was made out of electroformed nickel-copper, and the plastic was a liquid PVC plastisol
PVC
Polyvinyl chloride is a plastic.PVC may also refer to:*Param Vir Chakra, India's highest military honor*Peripheral venous catheter, a small, flexible tube placed into a peripheral vein in order to administer medication or fluids...
. The cooling method consisted of placing the mold into cold water. This process of rotational molding led to the creation of other plastic toys. As demand and popularity of this process increased, it was used to create other products such as road cones, marine buoys, and car armrests. This popularity led to the development of larger machinery. A new system of heating was also created, going from the original direct gas jets to the current indirect high velocity air system. In Europe during the 1960s the Engel process was developed. This allowed the creation of large hollow containers to be created in low-density polyethylene. The cooling method consisted of turning off the burners and allowing the plastic to harden while still rocking in the mold.
In 1976, the Association of Rotational Moulders (ARM) was started in Chicago as a worldwide trade association. The main objective of this association is to increase awareness of the rotational molding technology and process.
In the 1980s, new plastics, such as polycarbonate
Polycarbonate
PolycarbonatePhysical PropertiesDensity 1.20–1.22 g/cm3Abbe number 34.0Refractive index 1.584–1.586FlammabilityV0-V2Limiting oxygen index25–27%Water absorption – Equilibrium0.16–0.35%Water absorption – over 24 hours0.1%...
, polyester
Polyester
Polyester is a category of polymers which contain the ester functional group in their main chain. Although there are many polyesters, the term "polyester" as a specific material most commonly refers to polyethylene terephthalate...
, and nylon, were introduced to rotational molding. This has led to new uses for this process, such as the creation of fuel tanks and industrial moldings. The research that has been done since the late 1980s at Queen's University Belfast has led to the development of more precise monitoring and control of the cooling processes based on their development of the “Rotolog system”.
Equipment and tooling
Rotational molding machines are made in a wide range of sizes. They normally consist of molds, an oven, a cooling chamber, and mold spindles. The spindles are mounted on a rotating axis, which provides a uniform coating of the plastic inside each mold.Molds (or tooling) are either fabricated from welded sheet steel or cast. The fabrication method is often driven by part size and complexity; most intricate parts are likely made out of cast tooling. Molds are typically manufactured from stainless steel
Stainless steel
In metallurgy, stainless steel, also known as inox steel or inox from French "inoxydable", is defined as a steel alloy with a minimum of 10.5 or 11% chromium content by mass....
or aluminum. Aluminum molds are usually much thicker than an equivalent steel mold, as it is a softer metal. This thickness does not affect cycle times significantly since aluminum's thermal conductivity is many times greater than steel. Due to the need to develop a model prior to casting, cast molds tend to have additional costs associated with the manufacturing of the tooling, whereas fabricated steel or aluminum molds, particularly when used for less complex parts, are less expensive. However, some molds contain both aluminum and steel. This allows for variable thicknesses in the walls of the product. While this process is not as precise as injection molding
Injection molding
Injection molding is a manufacturing process for producing parts from both thermoplastic and thermosetting plastic materials. Material is fed into a heated barrel, mixed, and forced into a mold cavity where it cools and hardens to the configuration of the cavity...
, it does provide the designer with more options. The aluminum addition to the steel provides more heat capacity
Heat capacity
Heat capacity , or thermal capacity, is the measurable physical quantity that characterizes the amount of heat required to change a substance's temperature by a given amount...
, causing the melt-flow to stay in a fluid state for a longer period.
Standard setup and equipment for rotational molding
Normally all rotation molding systems have a number of parts including molds, oven, cooling chamber and mold spindles. The molds are used to create the part, and are typically made of aluminum. The quality and finish of the product is directly related to the quality of the mold being used. The oven is used to heat the part while also rotating the part to form the part desired. The cooling chamber is where the part is placed until it cools, and the spindles are mounted to rotate and provide a uniform coat of plastic inside each mold.Rock and roll machine
This is a specialized single arm machine. It rotates or rolls the mold 360 degrees in one direction and at the same time tips and rocks the mold 45 degrees above or below horizontal in the other direction. Newer machines use forced hot air to heat the mold. These machines are best for large parts that have large length-to-width ratio. Because of the smaller heating chambers, there is a saving in heating costs.Clamshell machine
This is a single arm rotational molding machine. The arm is usually supported by other arms on both ends. The clamshell machine heats and cools the mold in the same chamber. It takes up less space than equivalent shuttle and swing arm rotational molders. It is low in cost compared to the size of products made. It is available in smaller scales for schools interested in prototyping and for high quality models. More than one mold can be attached to the single arm.Vertical or up & over rotational machine
The loading and unloading area is at the front of the machine between the heating and cooling areas. These machines vary in size between small to medium compared to other rotational machines. Vertical rotational molding machines are energy efficient due to their compact heating and cooling chambers. These machines have the same (or similar) capabilities as the horizontal carousel multi-arm machines, but take up a much less space.Shuttle or swing arm machine
This is a single arm turret machine that moves the mold back and forth between the heating and cooling chambers. This machine moves the mold in a linear direction in and out of heating and cooling chambers. It is low in cost for the size of product produced. It is also available in smaller scale for schools and prototyping.Carousel machine
This is one of the most common machines in the industry. It can have up to 6 arms and comes in a wide range of sizes. The machine comes in two different models, fixed and independent. A fixed carousel consists of 3 fixed arms that must move together. One arm will be in the heating chamber while the other is in the cooling chamber and the other in the loading/reloading area. The fixed carousel works well when working with the same mold. The independent carousel machines are available with more arms that can move separately from the others. This allows for different size molds, with different heating and thickness needs.Production process
The rotational molding process is a high-temperature, low-pressure plastic-forming process that uses heat and biaxial rotation (i.e., angular rotation on two axes) to produce hollow, one-piece parts.Critics of the process point to its long cycle times—only one or two cycles an hour can typically occur, as opposed to other processes such as injection molding, where parts can be made in a few seconds. The process does have distinct advantages. Manufacturing large, hollow parts such as oil tanks is much easier by rotational molding than any other method. Rotational molds are significantly cheaper than other types of mold. Very little material is wasted using this process, and excess material can often be re-used, making it a very economically and environmentally viable manufacturing process.
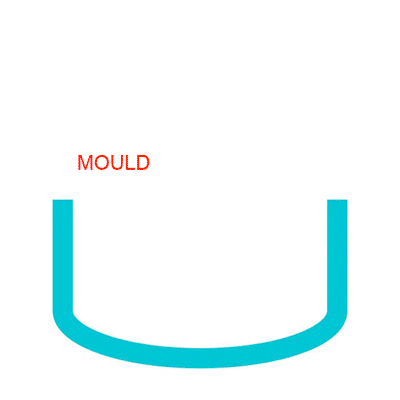
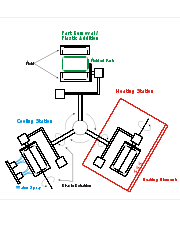
- Loading a measured quantity of polymerPolymerA polymer is a large molecule composed of repeating structural units. These subunits are typically connected by covalent chemical bonds...
(usually in powder form) into the mold. - Heating the mold in an oven while it rotates, until all the polymer has melted and adhered to the mold wall. The hollow part should be rotated through two or more axes, rotating at different speeds, in order to avoid the accumulation of polymer powder. The length of time the mold spends in the oven is critical: too long and the polymer will degrade, reducing impact strength. If the mold spends too little time in the oven, the polymer melt may be incomplete. The polymer grains will not have time to fully melt and coalesce on the mold wall, resulting in large bubbles in the polymer. This has an adverse effect on the mechanical properties of the finished product.
- Cooling the mold, usually by fan. This stage of the cycle can be quite lengthy. The polymer must be cooled so that it solidifies and can be handled safely by the operator. This typically takes tens of minutes. The part will shrink on cooling, coming away from the mold, and facilitating easy removal of the part. The cooling rate must be kept within a certain range. Very rapid cooling (for example, water spray) would result in cooling and shrinking at an uncontrolled rate, producing a warped part.
- Removal of the part.
Recent improvements
Until recently, the process was largely empirical, relying on both trial and error and the experience of the operator to judge when the part should be removed from the oven, and when it was cool enough to be removed from the mold. Technology has improved in recent years, allowing the air temperature in the mold to be monitored, removing much of the guesswork from the process.Much of the current research is into reducing the cycle time, as well as improving part quality. The most promising area is in mold pressurization. It is well known that applying a small amount of pressure internally to the mold at the correct point in the heating phase accelerates coalescence of the polymer particles during the melting, producing a part with fewer bubbles in less time than at atmospheric pressure
Atmospheric pressure
Atmospheric pressure is the force per unit area exerted into a surface by the weight of air above that surface in the atmosphere of Earth . In most circumstances atmospheric pressure is closely approximated by the hydrostatic pressure caused by the weight of air above the measurement point...
. This pressure delays the separation of the part from the mold wall due to shrinkage during the cooling phase, aiding cooling of the part. The main drawback to this is the danger to the operator of explosion of a pressurized part. This has prevented adoption of mold pressurization on a large scale by rotomolding manufacturers.
Mold release agents
A good mold release agent (MRA) will allow the material to be removed quickly and effectively. Mold releases can reduce cycle times, defects, and browning of finished product. There are a number of mold release types available; they can be categorized as follows:- Sacrificial coatings: the coating of MRA has to be applied each time because most of the MRA comes off on the molded part when it releases from the tool. Silicones are typical MRA compounds in this category.
- Semi-permanent coatings: the coating, if applied correctly, will last for a number of releases before requiring to be re-applied or touched up. This type of coating is most prevalent in today's rotational molding industry. The active chemistry involved in these coatings is typically a polysiloxane.
- Permanent coatings: most often some form of PTFE coating, which is applied to the mold. Permanent coatings avoid the need for operator application, but may become damaged by misuse.
Materials
More than 80% of all the material used is from the polyethylene family: cross-linked polyethylene (PEX), low-density polyethylene (LDPE), linear low-density polyethylene (LLDPE), high-density polyethylene (HDPE), and regrind. Other compounds are PVC plastisolsPolyvinyl chloride
Polyvinyl chloride, commonly abbreviated PVC, is a thermoplastic polymer. It is a vinyl polymer constructed of repeating vinyl groups having one hydrogen replaced by chloride. Polyvinyl chloride is the third most widely produced plastic, after polyethylene and polypropylene. PVC is widely used in...
, nylons, and polypropylene
Polypropylene
Polypropylene , also known as polypropene, is a thermoplastic polymer used in a wide variety of applications including packaging, textiles , stationery, plastic parts and reusable containers of various types, laboratory equipment, loudspeakers, automotive components, and polymer banknotes...
.
Order of materials most commonly used by industry :
- PolyethylenePolyethylenePolyethylene or polythene is the most widely used plastic, with an annual production of approximately 80 million metric tons...
- PolypropylenePolypropylenePolypropylene , also known as polypropene, is a thermoplastic polymer used in a wide variety of applications including packaging, textiles , stationery, plastic parts and reusable containers of various types, laboratory equipment, loudspeakers, automotive components, and polymer banknotes...
- Polyvinyl chloridePolyvinyl chloridePolyvinyl chloride, commonly abbreviated PVC, is a thermoplastic polymer. It is a vinyl polymer constructed of repeating vinyl groups having one hydrogen replaced by chloride. Polyvinyl chloride is the third most widely produced plastic, after polyethylene and polypropylene. PVC is widely used in...
- NylonNylonNylon is a generic designation for a family of synthetic polymers known generically as polyamides, first produced on February 28, 1935, by Wallace Carothers at DuPont's research facility at the DuPont Experimental Station...
- PolycarbonatePolycarbonatePolycarbonatePhysical PropertiesDensity 1.20–1.22 g/cm3Abbe number 34.0Refractive index 1.584–1.586FlammabilityV0-V2Limiting oxygen index25–27%Water absorption – Equilibrium0.16–0.35%Water absorption – over 24 hours0.1%...
These materials are also occasionally used (not in order of most used)::
- Aluminum
- Acrylonitrile butadiene styreneAcrylonitrile butadiene styreneAcrylonitrile butadiene styrene is a common thermoplastic. Its melting point is approximately 105 °C ....
(ABS) - AcetalAcetalAn acetal is a molecule with two single-bonded oxygen atoms attached to the same carbon atom.Traditional usages distinguish ketals from acetals...
- Acrylic
- EpoxyEpoxyEpoxy, also known as polyepoxide, is a thermosetting polymer formed from reaction of an epoxide "resin" with polyamine "hardener". Epoxy has a wide range of applications, including fiber-reinforced plastic materials and general purpose adhesives....
- Fluorocarbons
- IonomerIonomerAn ionomer is a polymer that comprises repeat units of both electrically neutral repeating units and a fraction of ionized units...
- PolybutylenePolybutylenePolybutylene is a polyolefin or saturated polymer with the chemical formula n. It should not be confused with polybutene, a low molecular weight oligomer with a different repeat unit....
- PolyesterPolyesterPolyester is a category of polymers which contain the ester functional group in their main chain. Although there are many polyesters, the term "polyester" as a specific material most commonly refers to polyethylene terephthalate...
- PolystyrenePolystyrenePolystyrene ) also known as Thermocole, abbreviated following ISO Standard PS, is an aromatic polymer made from the monomer styrene, a liquid hydrocarbon that is manufactured from petroleum by the chemical industry...
- PolyurethanePolyurethaneA polyurethane is any polymer composed of a chain of organic units joined by carbamate links. Polyurethane polymers are formed through step-growth polymerization, by reacting a monomer with another monomer in the presence of a catalyst.Polyurethanes are...
- SiliconeSiliconeSilicones are inert, synthetic compounds with a variety of forms and uses. Typically heat-resistant and rubber-like, they are used in sealants, adhesives, lubricants, medical applications , cookware, and insulation....
- Various foods (especially chocolateChocolateChocolate is a raw or processed food produced from the seed of the tropical Theobroma cacao tree. Cacao has been cultivated for at least three millennia in Mexico, Central and South America. Its earliest documented use is around 1100 BC...
)
Natural materials
Recently it has become possible to use natural materials in the molding process. Through the use of real sands and stone chip, sandstoneSandstone
Sandstone is a sedimentary rock composed mainly of sand-sized minerals or rock grains.Most sandstone is composed of quartz and/or feldspar because these are the most common minerals in the Earth's crust. Like sand, sandstone may be any colour, but the most common colours are tan, brown, yellow,...
composite can be created which is 80% natural non-processed material.
Rotational molding of plaster
Plaster
Plaster is a building material used for coating walls and ceilings. Plaster starts as a dry powder similar to mortar or cement and like those materials it is mixed with water to form a paste which liberates heat and then hardens. Unlike mortar and cement, plaster remains quite soft after setting,...
is used to produce hollow statuettes.
Chocolate is rotationally molded to form hollow treats.
Products
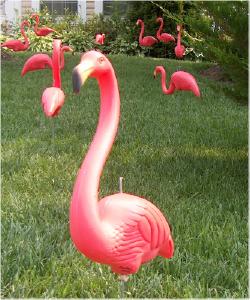
Inserts, threads, handles, minor undercuts
Undercut (manufacturing)
In manufacturing, an undercut is a special type of recessed surface. In turning it refers to a recess in a diameter. In machining it refers to a recess in a corner. In molding it refers to a feature that cannot be molded using only a single pull mold...
, flat surfaces without draft angles, or fine surface detail can be part of the design. Designs can also be multi-wall, either hollow or foam filled.
Products that can be manufactured using rotational molding include storage tanks, bins and refuse containers,airplane parts, doll parts, road cones, footballs, helmets, rowing boats and kayak hulls. Playground slides and roofs are also generally rotomolded.
Product design
There are many considerations for a designer when designing a part. Which factors are most important to a client? For instance, a part may need to be cheap and a certain color. However, if another color is cheaper, would the client be willing to change colors? Designers are responsible for considering all the limitations and benefits of using certain plastics. This may result in a new process being decided upon.Designing for rotational molding
Another consideration is in the draft angles. These are required to remove the piece from the mold. On the outside walls, a draft angle of 1° may work (assuming no rough surface or holes). On inside walls, such as the inside of a boat hull, a draft angle of 5° may be required. This is due to shrinkage and possible part warping.Another consideration is of structural support ribs. While solid ribs may be desirable and achievable in injection molding and other processes, a hollow rib is the best solution in rotational molding. A solid rib may be achieved through inserting a finished piece in the mold but this adds cost.
Rotational molding excels at producing hollow parts. However, care must be taken when this is done. When the depth of the recess is greater than the width there may be problems with even heating and cooling. Additionally, enough room must be left between the parallel walls to allow for the melt-flow to properly move throughout the mold. Otherwise webbing may occur. A desirable parallel wall scenario would have a gap at least three times the nominal wall thickness, with five times the nominal wall thickness being optimal. Sharp corners for parallel walls must also be considered. With angles of less than 45° bridging, webbing, and voids may occur.
Material limitations and considerations
Another consideration is the melt-flow of materials. Certain materials, such as nylonNylon
Nylon is a generic designation for a family of synthetic polymers known generically as polyamides, first produced on February 28, 1935, by Wallace Carothers at DuPont's research facility at the DuPont Experimental Station...
, will require larger radii than other materials. Additionally, the stiffness of the set material may be a factor. More structural and strengthening measures may be required when a flimsy material is used.
Wall thickness
One benefit of rotational molding is the ability to experiment, particularly with wall thicknesses. Cost is entirely dependent on wall thickness, with thicker walls being costlier and more time consuming to produce. While the wall thickness can be nearly any thickness, designers must remember that the thicker the wall, the more material and time will be required, increasing costs. In some cases, the plastics may significantly degrade due to extended periods at high temperature. Also, different materials have different thermal conductivityThermal conductivity
In physics, thermal conductivity, k, is the property of a material's ability to conduct heat. It appears primarily in Fourier's Law for heat conduction....
, meaning they require different times in the heating chamber and cooling chamber. Ideally, the part will be tested to use the minimum thickness required for the application. This minimum will then be established as a nominal thickness.
For the designer, while variable thicknesses are possible, a process called stop rotation is required. This process is limited in that only one side of the mold may be thicker than the others. After the mold is rotated and all the surfaces are sufficiently coated with the melt-flow, the rotation stops and the melt-flow is allowed to pool at the bottom of the mold cavity.
Wall thickness is important for corner radii as well. Large outside radii are preferable to small radii. Large inside radii are also preferable to small inside radii. This allows for a more even flow of material and a more even wall thickness. However, an outside corner is generally stronger than an inside corner.
Advantages
Rotational molding offers design advantages over other molding processes. With proper design, parts assembled from several pieces can be molded as one part, eliminating high fabrication costs.The process also has inherent design strengths, such as consistent wall thickness and strong outside corners that are virtually stress free. For additional strength, reinforcing ribs can be designed into the part. Along with being designed into the part, they can be added to the mold.
The ability to add prefinished pieces to the mold alone is a large advantage. Metal threads, internal pipes and structures, and even different colored plastics can all be added to the mold prior to the addition of plastic pellets. However, care must be taken to ensure that minimal shrinkage while cooling will not damage the part. This shrinking allows for mild undercuts and negates the need for ejection mechanisms (in most pieces).
Another advantage lies in the molds themselves. Since they require less tooling, they can be manufactured and put into production much more quickly than other molding processes. This is especially true for complex parts, which may require large amounts of tooling for other molding processes. Rotational molding is also the desired process for short runs and rush deliveries. The molds can be swapped quickly or different colors can be used without purging the mold. With other processes, purging may be required to swap colors.
Due to the uniform thicknesses achieved, large stretched sections are nonexistent, which makes large thin panels possible (although warping may occur). Also, there is little flow of plastic (stretching) but rather a placing of the material within the part. These thin walls also limit cost and production time.
Another cost limiting factor is the amount of material wasted in production. There are no sprues or runners (as in injection molding), no off-cuts (thermoforming), or pinch off scrap (blow molding). What material is wasted, through scrap or failed part testing, can usually be recycled.
Limitations
Rotationally molded parts have to follow some restrictions that are different from other plastic processes. As it is a low pressure process, sometimes designers face hard to reach areas in the mold. Good quality powder may help overcome some situations, but usually the designers have to keep in mind that it is not possible to make some sharp threads used in injection molded goods. Some products based on polyethylene can be put in the mold before filling it with the main material. This can help to avoid holes that otherwise would appear in some areas. This could also be achieved using molds with movable sections.Another limitation lies in the molds themselves. Unlike other processes where only the product needs to be cooled before being removed, with rotational molding the entire mold must be cooled. While water cooling processes are possible, there is still a significant down time of the mold. Additionally, this increases both financial and environmental costs. Some plastics will degrade with the long heating cycles or in the process of turning them into a powder to be melted.
Material requirements
Due to the nature of the process, materials selection must take into account the following:- Due to high temperatures within the mold the plastic must have a high resistance to permanent change in properties caused by heat (high thermal stabilityThermal stabilityThermal stability is the stability of a molecule at high temperatures; i.e. a molecule with more stability has more resistance to decomposition at high temperatures....
). - The molten plastic will come into contact with the oxygenOxygenOxygen is the element with atomic number 8 and represented by the symbol O. Its name derives from the Greek roots ὀξύς and -γενής , because at the time of naming, it was mistakenly thought that all acids required oxygen in their composition...
inside the mold—this can potentially lead to oxidation of the melted plastic and deterioration of the material's properties. Therefore, the chosen plastic must have a sufficient amount of antioxidantAntioxidantAn antioxidant is a molecule capable of inhibiting the oxidation of other molecules. Oxidation is a chemical reaction that transfers electrons or hydrogen from a substance to an oxidizing agent. Oxidation reactions can produce free radicals. In turn, these radicals can start chain reactions. When...
molecules to prevent such degradation in its liquid state. - Because there is no pressure to push the plastic into the mold, the chosen plastic must be able to flow easily through the cavities of the mold. The parts design must also take into account the flow characteristics of the particular plastic chosen.
Further reading
- Crawford, R, Throne, James L., Rotational Moulding of Plastics, William Andrew Inc. (2002). ISBN 1884207855
- Crawford, R, Kearns, M, Practical Guide to Rotational Moulding, Rapra Technology Ltd. (2003). ISBN 1859573878