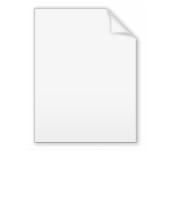
Selective Laser melting
Encyclopedia
Selective laser melting is an additive manufacturing
process that uses 3D CAD data as a digital information source and energy in the form of a high powered laser beam (usually an ytterbium fiber laser) to create three-dimensional metal parts by fusing fine metallic powders together. The industry standard term, chosen by the ASTM F42 standards committee, is laser sintering
, although this is acknowledged as a misnomer
because the process fully melts the metal into a solid homogeneous mass. The process is also sometimes referred to by the trade names DMLS or LaserCusing. A similar process is electron beam melting (EBM or E-beam), which, as the name suggests, uses electron beams as an energy source.
Early experiments using lasers to fully fuse metal powders go back many years, however the current generation of machines all emerged from a European project at the Fraunhofer Institute in Aachen Germany in the mid 1990s. Following this the process was developed by two of the original Fraunhofer researchers, Dr. Fockele and Dr. Schwarze, who formed F&S (subsequently Realizer GmbH) and entered into a commercial partnership with MTT Technologies Group (formerly MCP).
The process starts by slicing the 3D CAD file data into layers, usually from 20 to 100 micrometres thick, creating a 2D image of each layer; this file format is the industry standard .stl file used on most layer-based 3D printing or stereolithography technologies. This file is then loaded into a file preparation software package that assigns parameters, values and physical supports that allow the file to be interpreted and built by different types of additive manufacturing machines.
With SLM thin layers of atomized fine metal powder are evenly distributed using a coating mechanism onto a substrate plate, usually metal, that is fastened to an indexing table that moves in the vertical (Z) axis. This takes place inside a chamber containing a tightly controlled atmosphere of inert gas, either argon or nitrogen at oxygen levels below 500 parts per million. Once each layer has been distributed each 2D slice of the part geometry is fused by selectively applying the laser energy to the powder surface, by directing the focused laser beam using two high frequency scanning mirrors in the X and Y axes. The laser energy is intense enough to permit full melting (welding) of the particles to form solid metal. The process is repeated layer after layer until the part is complete.
components.
Additive manufacturing
Additive manufacturing is defined by ASTM as the "process of joining materials to make objects from 3D model data, usually layer upon layer, as opposed to subtractive manufacturing methodologies, such as traditional machining...
process that uses 3D CAD data as a digital information source and energy in the form of a high powered laser beam (usually an ytterbium fiber laser) to create three-dimensional metal parts by fusing fine metallic powders together. The industry standard term, chosen by the ASTM F42 standards committee, is laser sintering
Selective laser sintering
Selective laser sintering is an additive manufacturing technique that uses a high power laser to fuse small particles of plastic, metal , ceramic, or glass powders into a mass that has a desired 3-dimensional shape...
, although this is acknowledged as a misnomer
Misnomer
A misnomer is a term which suggests an interpretation that is known to be untrue. Such incorrect terms sometimes derive their names because of the form, action, or origin of the subject becoming named popularly or widely referenced—long before their true natures were known.- Sources of misnomers...
because the process fully melts the metal into a solid homogeneous mass. The process is also sometimes referred to by the trade names DMLS or LaserCusing. A similar process is electron beam melting (EBM or E-beam), which, as the name suggests, uses electron beams as an energy source.
Early experiments using lasers to fully fuse metal powders go back many years, however the current generation of machines all emerged from a European project at the Fraunhofer Institute in Aachen Germany in the mid 1990s. Following this the process was developed by two of the original Fraunhofer researchers, Dr. Fockele and Dr. Schwarze, who formed F&S (subsequently Realizer GmbH) and entered into a commercial partnership with MTT Technologies Group (formerly MCP).
The process starts by slicing the 3D CAD file data into layers, usually from 20 to 100 micrometres thick, creating a 2D image of each layer; this file format is the industry standard .stl file used on most layer-based 3D printing or stereolithography technologies. This file is then loaded into a file preparation software package that assigns parameters, values and physical supports that allow the file to be interpreted and built by different types of additive manufacturing machines.
With SLM thin layers of atomized fine metal powder are evenly distributed using a coating mechanism onto a substrate plate, usually metal, that is fastened to an indexing table that moves in the vertical (Z) axis. This takes place inside a chamber containing a tightly controlled atmosphere of inert gas, either argon or nitrogen at oxygen levels below 500 parts per million. Once each layer has been distributed each 2D slice of the part geometry is fused by selectively applying the laser energy to the powder surface, by directing the focused laser beam using two high frequency scanning mirrors in the X and Y axes. The laser energy is intense enough to permit full melting (welding) of the particles to form solid metal. The process is repeated layer after layer until the part is complete.
Materials
Most machines operate with a build chamber of 250 mm in X & Y and up to 350 mm Z (although larger machines up to 500 mm X,Y,Z and smaller machines do exist). The types of materials that can be processed include stainless steel, tool steel, cobalt chrome, titanium & aluminium. All must exist in atomized form and exhibit certain flow characteristics in order to be process capable.Applications
The types of applications most suited to the SLM process are complex geometries & structures with thin walls and hidden voids or channels. Advantage can be gained when producing hybrid forms where solid and partially formed or lattice type geometries can be produced together to create a single object, such as a hip stem or acetabular cup or other orthopedic implant where oseointegration is enhanced by the surface geometry. Much of the pioneering work with SLM technologies is on lightweight parts for aerospace where traditional manufacturing constraints, such as tooling and physical access to surfaces for machining, restrict the design of components. SLM allows parts to be built additively rather than by removing waste material to form near net shapeNear net shape
Near net shape is an industrial manufacturing technique. The name implies that the initial production of the item is very close to the final shape, reducing the need for surface finishing...
components.
Potential
SLM or additive manufacturing (sometimes referred to as rapid manufacturing or rapid prototyping) is in its infancy with relatively few users in comparison to conventional methods such as machining, casting or forging metals, although those that are using the technology have become highly proficient. Like any process or method SLM must be suited to the task at hand. Certain markets such as aerospace or medical orthopedics are actively evaluating the technology as a future manufacturing process, but barriers to acceptance are high and compliance issues result in long periods of certification & qualification. This is currently demonstrated by the lack of fully formed international standards by which to measure the performance of competing systems. The standard in question is ASTM F2792-10 Standard Terminology for Additive Manufacturing Technologies.See also
- 3D printing3D printing3D printing is a form of additive manufacturing technology where a three dimensional object is created by laying down successive layers of material. 3D printers are generally faster, more affordable, and easier to use than other additive manufacturing technologies. However, the term 3D printing is...
- Desktop manufacturing
- Digital fabricator
- Direct digital manufacturing
- Rapid manufacturing
- Selective laser sinteringSelective laser sinteringSelective laser sintering is an additive manufacturing technique that uses a high power laser to fuse small particles of plastic, metal , ceramic, or glass powders into a mass that has a desired 3-dimensional shape...
- Solid freeform fabrication
- StereolithographyStereolithographyStereolithography is an additive manufacturing technology for producing models, prototypes, patterns, and in some cases, production parts.-Technology description:...