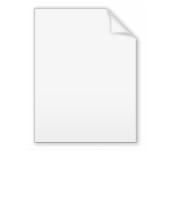
Shell molding
Encyclopedia
Shell molding, also known as shell-mold casting, is an expendable mold casting
process that uses a resin
covered sand
to form the mold. As compared to sand casting
, this process has better dimensional accuracy, a higher productivity rate, and lower labor requirements. It is used for small to medium parts that require high precision.
Examples of shell molded items include gear housings, cylinder heads and connecting rods. It is also used to make high-precision molding cores.
The machine that is used for this process is called a shell molding machine. It heats the pattern, applies the sand mixture, and bakes the shell.
, aluminum and copper
alloys. Aluminum and magnesium
products average about 13.5 kg (29.8 lb) as a normal limit, but it is possible to cast items in the 45–90 kg (99.2–198.4 lb) range. The small end of the limit is 30 g (1 oz). Depending on the material, the thinnest cross-section castable is 1.5 to 6 mm (0.0590551181102362 to 0.236220472440945 in). The minimum draft is 0.25 to 0.5 degrees.
Typical tolerances are 0.005 mm/mm or in/in because the sand compound is designed to barely shrink and a metal pattern is used. The cast surface finish
is 0.3–4.0 micrometers (50–150 μin) because a finer sand is used. The resin also assists in forming a very smooth surface. The process, in general, produces very consistent castings from one casting to the next.
The sand-resin mix can be recycled by burning off the resin at high temperatures.
. The high productivity, low labor costs, good surface finishes, and precision of the process can more than pay for itself if it reduces machining costs. There are also few problems due to gases, because of the absence of moisture in the shell, and the little gas that is still present easily escapes through the thin shell. When the metal is poured some of the resin binder burns out on the surface of the shell, which makes shaking out easy.
One disadvantage is that the gating system must be part of the pattern because the entire mold is formed from the pattern, which can be expensive. Another is the resin for the sand is expensive, however not much is required because only a shell is being formed.
Casting
In metalworking, casting involves pouring liquid metal into a mold, which contains a hollow cavity of the desired shape, and then allowing it to cool and solidify. The solidified part is also known as a casting, which is ejected or broken out of the mold to complete the process...
process that uses a resin
Resin
Resin in the most specific use of the term is a hydrocarbon secretion of many plants, particularly coniferous trees. Resins are valued for their chemical properties and associated uses, such as the production of varnishes, adhesives, and food glazing agents; as an important source of raw materials...
covered sand
Sand
Sand is a naturally occurring granular material composed of finely divided rock and mineral particles.The composition of sand is highly variable, depending on the local rock sources and conditions, but the most common constituent of sand in inland continental settings and non-tropical coastal...
to form the mold. As compared to sand casting
Sand casting
Sand casting, also known as sand molded casting, is a metal casting process characterized by using sand as the mold material.It is relatively cheap and sufficiently refractory even for steel foundry use. A suitable bonding agent is mixed or occurs with the sand...
, this process has better dimensional accuracy, a higher productivity rate, and lower labor requirements. It is used for small to medium parts that require high precision.
Examples of shell molded items include gear housings, cylinder heads and connecting rods. It is also used to make high-precision molding cores.
Process
The process of creating a shell mold consists of six steps:- Fine silica sand that is covered in a thin (3–6%) thermosetting phenolic resin and liquid catalyst is dumped, blown, or shot onto a hot patternPattern (casting)In casting, a pattern is a replica of the object to be cast, used to prepare the cavity into which molten material will be poured during the casting process.Patterns used in sand casting may be made of wood, metal, plastics or other materials...
. The pattern is usually made from cast iron and is heated to 230 to 315 °C (450 to 600 °F). The sand is allowed to sit on the pattern for a few minutes to allow the sand to partially cure. - The pattern and sand are then inverted so the excess sand drops free of the pattern, leaving just the "shell". Depending on the time and temperature of the pattern the thickness of the shell is 10 to 20 mm (0.393700787401575 to 0.78740157480315 in).
- The pattern and shell together are placed in an oven to finish curing the sand. The shell now has a tensile strengthTensile strengthUltimate tensile strength , often shortened to tensile strength or ultimate strength, is the maximum stress that a material can withstand while being stretched or pulled before necking, which is when the specimen's cross-section starts to significantly contract...
of 350 to 450 psi (2.4 to 3.1 MPa). - The hardened shell is then stripped from the pattern.
- Two or more shells are then combined, via clamping or gluing using a thermoset adhesive, to form a mold. This finished mold can then be used immediately or stored almost indefinitely.
- For casting the shell mold is placed inside a flask and surrounded with shotLead shotLead shot is a collective term for small balls of lead. These were the original projectiles for muskets and early rifles, but today lead shot is fired primarily from shotguns. It is also used for a variety of other purposes...
, sand, or gravelGravelGravel is composed of unconsolidated rock fragments that have a general particle size range and include size classes from granule- to boulder-sized fragments. Gravel can be sub-categorized into granule and cobble...
to reinforce the shell.
The machine that is used for this process is called a shell molding machine. It heats the pattern, applies the sand mixture, and bakes the shell.
Details
Setup and production of shell mold patterns takes weeks, after which an output of 5–50 pieces/hr-mold is attainable. Common materials include cast ironCast iron
Cast iron is derived from pig iron, and while it usually refers to gray iron, it also identifies a large group of ferrous alloys which solidify with a eutectic. The color of a fractured surface can be used to identify an alloy. White cast iron is named after its white surface when fractured, due...
, aluminum and copper
Copper
Copper is a chemical element with the symbol Cu and atomic number 29. It is a ductile metal with very high thermal and electrical conductivity. Pure copper is soft and malleable; an exposed surface has a reddish-orange tarnish...
alloys. Aluminum and magnesium
Magnesium
Magnesium is a chemical element with the symbol Mg, atomic number 12, and common oxidation number +2. It is an alkaline earth metal and the eighth most abundant element in the Earth's crust and ninth in the known universe as a whole...
products average about 13.5 kg (29.8 lb) as a normal limit, but it is possible to cast items in the 45–90 kg (99.2–198.4 lb) range. The small end of the limit is 30 g (1 oz). Depending on the material, the thinnest cross-section castable is 1.5 to 6 mm (0.0590551181102362 to 0.236220472440945 in). The minimum draft is 0.25 to 0.5 degrees.
Typical tolerances are 0.005 mm/mm or in/in because the sand compound is designed to barely shrink and a metal pattern is used. The cast surface finish
Surface finish
Surface finish, also known as surface texture, is the characteristics of a surface. It has three components: lay, surface roughness, and waviness.-Lay:...
is 0.3–4.0 micrometers (50–150 μin) because a finer sand is used. The resin also assists in forming a very smooth surface. The process, in general, produces very consistent castings from one casting to the next.
The sand-resin mix can be recycled by burning off the resin at high temperatures.
Advantages and disadvantages
One of the greatest advantages of this process is that it can be completely automated for mass productionMass production
Mass production is the production of large amounts of standardized products, including and especially on assembly lines...
. The high productivity, low labor costs, good surface finishes, and precision of the process can more than pay for itself if it reduces machining costs. There are also few problems due to gases, because of the absence of moisture in the shell, and the little gas that is still present easily escapes through the thin shell. When the metal is poured some of the resin binder burns out on the surface of the shell, which makes shaking out easy.
One disadvantage is that the gating system must be part of the pattern because the entire mold is formed from the pattern, which can be expensive. Another is the resin for the sand is expensive, however not much is required because only a shell is being formed.