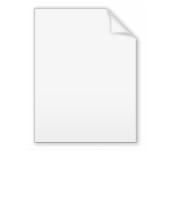
Stock management
Encyclopedia
Stock management is the function of understanding the stock mix
of a company and the different demands on that stock. The demands are influenced by both external and internal factors and are balanced by the creation of Purchase order request
s to keep supplies at a reasonable or prescribed level.
The management of the inventory in the supply chain involves managing the physical quantities as well as the costing of the goods as it flows through the supply chain.
In managing the cost prices of the goods throughout the supply chain, several costing methods are employed:
If the calculation is done on a monthly basis, then it is referred to the periodic method.
In this method, the available stock is calculated by:
ADD Stock at beginning of period
ADD Stock purchased during the period
AVERAGE total cost by total qty to arrive at the Average Cost of Goods for the period.
This Average Cost Price is applied to all movements and adjustments in that period.
Ending stock in qty is arrived at by Applying all the changes in qty to the Available balance.
Multiplying the stock balance in qty by the Average cost gives the Stock cost at the end of the period.
Using the perpetual method, the calculation is done upon every purchase transaction.
Thus, the calculation is the same based on the periodic calculation whether by period (periodic) or by transaction (perpetual).
The only difference is the 'periodicity' or scope of the calculation.
- Periodic is done monthly
- Perpetual is done for the duration of the purchase until the next purchase
In practice, the daily averaging has been used to closely approximate the perpetual method.
6. Bottle neck method ( depends on proper planning support)
(VMI) and Customer Managed Inventory (CMI) are a few of the popular models being employed by organizations looking to have greater stock management control.
JIT is a model which attempts to replenish inventory for organizations when the inventory is required. The model attempts to avoid excess inventory and its associated costs. As a result, companies receive inventory only when the need for more stock is approaching.
VMI and CMI are two business models that adhere to the JIT inventory principles. VMI gives the vendor in a vendor/customer relationship the ability to monitor, plan and control inventory for their customers. Customers relinquish the order making responsibilities in exchange for timely inventory replenishment that increases organizational efficiency.
CMI allows the customer to order and control their inventory from their vendors/suppliers. Both VMI and CMI benefit the vendor as well as the customer. Vendors see a significant increase in sales due to increased inventory turns and cost savings realized by their customers, while customers realize similar benefits.
Stock mix
Stock mix - is the combination of products a company sells or manufactures. The stock mix is determined by the demand for certain products and the profitability of those products....
of a company and the different demands on that stock. The demands are influenced by both external and internal factors and are balanced by the creation of Purchase order request
Purchase Order Request
A purchase order request or purchase requisition is a request sent internally within a company to obtain purchased goods and services, including stock...
s to keep supplies at a reasonable or prescribed level.
Retail supply chain
Stock management in the retail supply chain follows the following sequence:- Request for new stock from stores to head office
- Head office issues purchase orders to the vendor
- Vendor ships the goods
- Warehouse receives the goods
- Warehouse stocks and distributes to the stores
- Stores receive the goods
- Goods are sold to customers at the stores
The management of the inventory in the supply chain involves managing the physical quantities as well as the costing of the goods as it flows through the supply chain.
In managing the cost prices of the goods throughout the supply chain, several costing methods are employed:
- Retail method
- Weighted Average Price method
- FIFO (First In First Out) method chillin
- LIFO (Last In First Out) method
- LPP (Last Purchase Price) method
- BNM (Bottle neck method)
Weighted Average Price Method
The calculation can be done for different periods.If the calculation is done on a monthly basis, then it is referred to the periodic method.
In this method, the available stock is calculated by:
ADD Stock at beginning of period
ADD Stock purchased during the period
AVERAGE total cost by total qty to arrive at the Average Cost of Goods for the period.
This Average Cost Price is applied to all movements and adjustments in that period.
Ending stock in qty is arrived at by Applying all the changes in qty to the Available balance.
Multiplying the stock balance in qty by the Average cost gives the Stock cost at the end of the period.
Using the perpetual method, the calculation is done upon every purchase transaction.
Thus, the calculation is the same based on the periodic calculation whether by period (periodic) or by transaction (perpetual).
The only difference is the 'periodicity' or scope of the calculation.
- Periodic is done monthly
- Perpetual is done for the duration of the purchase until the next purchase
In practice, the daily averaging has been used to closely approximate the perpetual method.
6. Bottle neck method ( depends on proper planning support)
Software applications
The implementation of inventory management applications has become a valuable tool for organizations looking to more efficiently manage stock. While the capabilities of applications vary, most inventory management applications give organizations a structured method of accounting for all incoming and outgoing inventory within their facilities. Organizations save a significant amount in costs associated with manual inventory counts, administrative errors and reductions in inventory stock-outs.Business models
Just-in-time Inventory (JIT), Vendor Managed InventoryVendor Managed Inventory
Vendor-managed inventory is a family of business models in which the buyer of a product provides certain information to a supplier of that product and the supplier takes full responsibility for maintaining an agreed inventory of the material, usually at the buyer's consumption location .A...
(VMI) and Customer Managed Inventory (CMI) are a few of the popular models being employed by organizations looking to have greater stock management control.
JIT is a model which attempts to replenish inventory for organizations when the inventory is required. The model attempts to avoid excess inventory and its associated costs. As a result, companies receive inventory only when the need for more stock is approaching.
VMI and CMI are two business models that adhere to the JIT inventory principles. VMI gives the vendor in a vendor/customer relationship the ability to monitor, plan and control inventory for their customers. Customers relinquish the order making responsibilities in exchange for timely inventory replenishment that increases organizational efficiency.
CMI allows the customer to order and control their inventory from their vendors/suppliers. Both VMI and CMI benefit the vendor as well as the customer. Vendors see a significant increase in sales due to increased inventory turns and cost savings realized by their customers, while customers realize similar benefits.