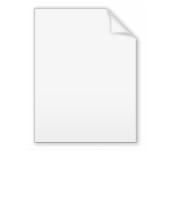
Ultrasonic consolidation
Encyclopedia
Ultrasonic Consolidation (UC), sometimes referred to as Ultrasonic Additive Manufacturing (UAM), is an additive manufacturing
technique based on the ultrasonic welding
of metal
foils and CNC contour milling. High-frequency (typically 20,000 hertz
) ultrasonic vibrations are locally applied to metal foil materials, held together under pressure
, to create a solid-state weld. CNC contour milling is then used to create the required shape for the given layer. This process is then repeated until a solid component has been created or a feature repaired/added to a component. UC has the ability to join dissimilar metal materials of different thicknesses and allows the embedment of fibre materials at relatively low temperature
, (typically less than 50% of the metal matrix melting temperature), and pressure into solid metal matrices.
The general manufacturing process is:
Additive manufacturing
Additive manufacturing is defined by ASTM as the "process of joining materials to make objects from 3D model data, usually layer upon layer, as opposed to subtractive manufacturing methodologies, such as traditional machining...
technique based on the ultrasonic welding
Ultrasonic welding
Ultrasonic welding is an industrial technique whereby high-frequency ultrasonic acoustic vibrations are locally applied to workpieces being held together under pressure to create a solid-state weld. It is commonly used for plastics, and especially for joining dissimilar materials...
of metal
Metal
A metal , is an element, compound, or alloy that is a good conductor of both electricity and heat. Metals are usually malleable and shiny, that is they reflect most of incident light...
foils and CNC contour milling. High-frequency (typically 20,000 hertz
Hertz
The hertz is the SI unit of frequency defined as the number of cycles per second of a periodic phenomenon. One of its most common uses is the description of the sine wave, particularly those used in radio and audio applications....
) ultrasonic vibrations are locally applied to metal foil materials, held together under pressure
Pressure
Pressure is the force per unit area applied in a direction perpendicular to the surface of an object. Gauge pressure is the pressure relative to the local atmospheric or ambient pressure.- Definition :...
, to create a solid-state weld. CNC contour milling is then used to create the required shape for the given layer. This process is then repeated until a solid component has been created or a feature repaired/added to a component. UC has the ability to join dissimilar metal materials of different thicknesses and allows the embedment of fibre materials at relatively low temperature
Temperature
Temperature is a physical property of matter that quantitatively expresses the common notions of hot and cold. Objects of low temperature are cold, while various degrees of higher temperatures are referred to as warm or hot...
, (typically less than 50% of the metal matrix melting temperature), and pressure into solid metal matrices.
History
The Ultrasonic Consolidation process was invented and patented by Dawn White. In 1999, White founded Solidica Inc. which is the commercial owner and provider of the UC technology. The commercial equipment for UC is called the Form-ation machine.Process
As with most other additive manufacturing processes UC creates objects directly from a CAD model of the required object. The file is then "sliced" into layers which results in the production of a .STL file that can be used by the UC machine to build the required object, layer by layer.The general manufacturing process is:
- A base plate is placed onto the machine anvilAnvilAn anvil is a basic tool, a block with a hard surface on which another object is struck. The inertia of the anvil allows the energy of the striking tool to be transferred to the work piece. In most cases the anvil is used as a forging tool...
and fixed into place. - Metal foil is then drawn under the sonotrodeSonotrodeThe sonotrode is a piece of metal or tool that is exposed to ultrasonic vibration, and then gives this vibratory energy in an element to apply ....
, which applies pressure through a normal force and the ultrasonic oscillations, and bonded to the plate. - This process is then repeated until the required area has been covered in ultrasonically consolidated material.
- A CNC mill is then used to trim the excess foil from the component and achieve the required geometry.
- The deposit and trim cycle is repeated until a specified height is reached, (typically 3–6 mm).
- At this height a smaller finishing mill is used to create the required tolerance and surface finishSurface finishSurface finish, also known as surface texture, is the characteristics of a surface. It has three components: lay, surface roughness, and waviness.-Lay:...
of the part. - The deposit, trim and finish cycle continues until the finished object has been manufactured; at which point it is taken off the anvil and the finished article is removed from the base plate.