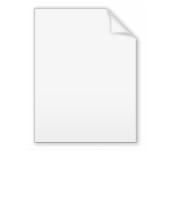
Compression molding
Encyclopedia
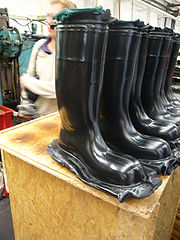
Molding (process)
Molding or moulding is the process of manufacturing by shaping pliable raw material using a rigid frame or model called a pattern....
in which the molding material, generally preheated, is first placed in an open, heated mold
Mold
Molds are fungi that grow in the form of multicellular filaments called hyphae. Molds are not considered to be microbes but microscopic fungi that grow as single cells called yeasts...
cavity. The mold is closed with a top force or plug member, pressure is applied to force the material into contact with all mold areas, while heat
Heat
In physics and thermodynamics, heat is energy transferred from one body, region, or thermodynamic system to another due to thermal contact or thermal radiation when the systems are at different temperatures. It is often described as one of the fundamental processes of energy transfer between...
and pressure
Pressure
Pressure is the force per unit area applied in a direction perpendicular to the surface of an object. Gauge pressure is the pressure relative to the local atmospheric or ambient pressure.- Definition :...
are maintained until the molding material has cured. The process employs thermosetting resin
Resin
Resin in the most specific use of the term is a hydrocarbon secretion of many plants, particularly coniferous trees. Resins are valued for their chemical properties and associated uses, such as the production of varnishes, adhesives, and food glazing agents; as an important source of raw materials...
s in a partially cured stage, either in the form of granules, putty
Putty
Putty is a generic term for a plastic material similar in texture to clay or dough typically used in domestic construction and repair as a sealant or filler. Painter's Putty is typically a linseed oil based product used for filling holes, minor cracks and defacements in wood only...
-like masses, or preforms. Compression molding is a high-volume, high-pressure method suitable for molding complex, high-strength fiberglass
Fiberglass
Glass fiber is a material consisting of numerous extremely fine fibers of glass.Glassmakers throughout history have experimented with glass fibers, but mass manufacture of glass fiber was only made possible with the invention of finer machine tooling...
reinforcements. Advanced composite thermoplastic
Thermoplastic
Thermoplastic, also known as a thermosoftening plastic, is a polymer that turns to a liquid when heated and freezes to a very glassy state when cooled sufficiently...
s can also be compression molded with unidirectional tapes, woven fabrics, randomly oriented fiber mat or chopped strand. The advantage of compression molding is its ability to mold large, fairly intricate parts. Also, it is one of the lowest cost molding methods compared with other methods such as transfer molding
Transfer molding
Transfer molding, like compression molding, is a process where the amount of molding material is measured and inserted before the molding takes place. The molding material is preheated and loaded into a chamber known as the pot...
and injection molding
Injection molding
Injection molding is a manufacturing process for producing parts from both thermoplastic and thermosetting plastic materials. Material is fed into a heated barrel, mixed, and forced into a mold cavity where it cools and hardens to the configuration of the cavity...
; moreover it wastes relatively little material, giving it an advantage when working with expensive compounds. However, compression molding often provides poor product consistency and difficulty in controlling flashing, and it is not suitable for some types of parts. Fewer knit lines are produced and a smaller amount of fiber-length degradation is noticeable when compared to injection molding. Compression-molding is also suitable for ultra-large basic shape production in sizes beyond the capacity of extrusion techniques. Materials that are typically manufactured through compression molding include: Polyester fiberglass resin systems (SMC/BMC), Torlon, Vespel, Poly(p-phenylene sulfide)
Poly(p-phenylene sulfide)
Polyphenylene sulfide is an organic polymer consisting of aromatic rings linked with sulfides. Synthetic fiber and textiles derived from this polymer are known to resist chemical and thermal attack. PPS is used to make filter fabric for coal boilers, papermaking felts, electrical insulation,...
(PPS), and many grades of PEEK
PEEK
Polyether ether ketone is a colourless organic polymer thermoplastic used in engineering applications.-Synthesis:PEEK polymers are obtained by step-growth polymerization by the dialkylation of bisphenolate salts. Typical is the reaction of 4,4'-difluorobenzophenone with the disodium salt of...
.
Compression molding was first developed to manufacture composite parts for metal replacement applications, compression molding is typically used to make larger flat or moderately curved parts. This method of molding is greatly used in manufacturing automotive parts such as hoods, fenders, scoops, spoilers, as well as smaller more intricate parts.
The material to be molded is positioned in the mold cavity and the heated platens are closed by a hydraulic ram. Bulk molding compound (BMC) or sheet molding compound (SMC), are conformed to the mold form by the applied pressure and heated until the curing reaction occurs. SMC feed material usually is cut to conform to the surface area of the mold. The mold is then cooled and the part removed.
Materials may be loaded into the mold either in the form of pellets or sheet, or the mold may be loaded from a plasticating extruder. Materials are heated above their melting points, formed and cooled. The more evenly the feed material is distributed over the mold surface, the less flow orientation occurs during the compression stage.
Thermoplastic matrices are commonplace in mass production industries e.g. automotive applications where the leading technologies are Long Fibre reinforced Thermoplastics (LFT) and Glass fiber Mat reinforced Thermoplastics (GMT).
In compression molding there are six important considerations that an engineer should bear in mind:
- Determining the proper amount of material.
- Determining the minimum amount of energy required to heat the material.
- Determining the minimum time required to heat the material.
- Determining the appropriate heating technique.
- Predicting the required force, to ensure that shot attains the proper shape.
- Designing the mold for rapid cooling after the material has been compressed into the mold.
Process definition
Compression molding is a forming process in which a plastic material is placed directly into a heated metal mold, then is softened by the heat, and forced to conform to the shape of the mold as the mold closes.Process characteristics
The use of thermoset plastic compounds characterizes this molding process from many of the other molding processes. These thermosets can be in either preform or granule shapes. Unlike some of the other processes we find that the materials are usually preheated and measured before molding. This helps to reduce excess flash. Inserts, usually metallic, can also be molded with the plastic. As a side note, remember not to allow any undercuts on the shape, it will make ejection especially difficult. Thermoplastic matrices with an inherent indefinite shelf-life and shorter cycle moulding times are widely used and examples are shown in Ref 3.Process schematic
The compression molding starts, with an allotted amount of plastic or gelatin placed over or inserted into a mold. Afterward the material is heated to a pliable state in and by the mold. Shortly there after the hydraulic press compresses the pliable plastic against the mold, resulting in a perfectly molded piece, retaining the shape of the inside surface of the mold. After the hydraulic press releases, an ejector pin in the bottom of the mold quickly ejects the finish piece out of the mold and then the process is finished. Also depending on the type of plunger used in the press there will or won't be excess material on the mold.Workpiece geometry
This process is commonly used for manufacturing electrical parts, dinnerware, and gears. This process is also used to produce buttons, buckles, knobs, handles, appliance housing, radio cases, and large containers. Common commercial examples are shown in Ref 3.Setup and equipment
Compression mold presses are manufactured in a wide variety of sizes. Most presses utilize a hydraulic ram in order to produce sufficient force during the molding operation. The tools consist of a male mold plunger and a female mold.Typical tools and geometry produced
Three types of molds used are the flash plunger-type, straight plunger-type, and the "landed" plunger-type molds. The flash type mold must have an accurate charge of plastic and produces a horizontal flash (this is excess material that protrudes out of the mold). The straight plunger-type mold allows for some inaccuracy in the charge of plastic and produces a vertical flash. The landed plunger type mold must have an accurate charge of plastic, and no flash is produced. Further details are explained in Ref 3.Further reading
- Compression Molding, ASM Handbook 2001, volume 21 Composites, Peterson, Charles W, Ehnert G, Liebold R and Kühfusz R pp516–535, ISBN 0-817170-703-9