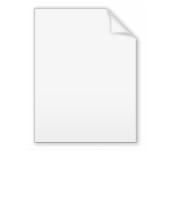
Hardfacing
Encyclopedia
Hardfacing is a metalworking process where harder or tougher material is applied to a base metal. It is welded
to the base material, and generally takes the form of specialized electrodes for arc welding
or filler rod for oxyacetylene
and TIG
welding. Powder metal alloys are used in (PTA) also called Powder plasma welding system and Thermal spray processes like HVOF , Plasma spray, Fuse and spray etc.
Hardfacing may be applied to a new part during production to increase its wear resistance, or it may be used to restore a worn-down surface.
Hardfacing by arc welding is a surfacing operation to extend the service life of industrial components, pre-emptively on new components, or as part of a maintenance program. The result of significant savings in machine down time and production costs has meant that this process has been adopted across many industries such as Steel, Cement, Mining, Petrochemical, Power, Sugar cane and Food.
Extensive work in research has resulted in the development of a wide range of alloys and welding procedures. The optimum alloy selection is made considering the component service conditions and feedback of the service performance.
For each industrial application and wear phenomena, there is a welding electrode to provide wear resistance.
Hardfacing can be deposited by various welding methods:
Commonly applied materials include cobalt-based alloys (such as stellite
), nickel-based alloys, chromium carbide
alloys and NOREM
.
Welding
Welding is a fabrication or sculptural process that joins materials, usually metals or thermoplastics, by causing coalescence. This is often done by melting the workpieces and adding a filler material to form a pool of molten material that cools to become a strong joint, with pressure sometimes...
to the base material, and generally takes the form of specialized electrodes for arc welding
Arc welding
Arc welding is a type of welding that uses a welding power supply to create an electric arc between an electrode and the base material to melt the metals at the welding point. They can use either direct or alternating current, and consumable or non-consumable electrodes...
or filler rod for oxyacetylene
Oxy-fuel welding and cutting
Oxy-fuel welding and oxy-fuel cutting are processes that use fuel gases and oxygen to weld and cut metals, respectively. French engineers Edmond Fouché and Charles Picard became the first to develop oxygen-acetylene welding in 1903...
and TIG
Gas tungsten arc welding
Gas tungsten arc welding , also known as tungsten inert gas welding, is an arc welding process that uses a nonconsumable tungsten electrode to produce the weld...
welding. Powder metal alloys are used in (PTA) also called Powder plasma welding system and Thermal spray processes like HVOF , Plasma spray, Fuse and spray etc.
Hardfacing may be applied to a new part during production to increase its wear resistance, or it may be used to restore a worn-down surface.
Hardfacing by arc welding is a surfacing operation to extend the service life of industrial components, pre-emptively on new components, or as part of a maintenance program. The result of significant savings in machine down time and production costs has meant that this process has been adopted across many industries such as Steel, Cement, Mining, Petrochemical, Power, Sugar cane and Food.
Extensive work in research has resulted in the development of a wide range of alloys and welding procedures. The optimum alloy selection is made considering the component service conditions and feedback of the service performance.
For each industrial application and wear phenomena, there is a welding electrode to provide wear resistance.
Hardfacing can be deposited by various welding methods:
- Shielded Metal Arc Welding (SMAW)
- Gas Metal Arc Welding (GMAW), including both gas-shielded and open arc welding
- Oxyfuel Welding (OFW)
- Submerged Arc Welding (SAW)
- Electrolag Welding (ESW)
- Plasma Arc Welding (PAW), also called Powder Plasma welding system
- Thermal spraying
- Cold polymer compounds
Commonly applied materials include cobalt-based alloys (such as stellite
Stellite
Stellite alloy is a range of cobalt-chromium alloys designed for wear resistance. It may also contain tungsten or molybdenum and a small but important amount of carbon...
), nickel-based alloys, chromium carbide
Chromium carbide
Chromium carbide is an extremely hard refractory ceramic material. It is usually processed by sintering. It has the appearance of a gray powder with orthorhombic crystal structure. The orthorhombic Cr3C2 occurs extremely rarely as mineral tongbaite....
alloys and NOREM
NOREM
NOREM is a hardfacing material developed by Electric Power Research Institute to deal with radio safety issues associated with the use of cobalt alloys in nuclear power station coolant systems . It is a solid-solution strengthened austenitic matrix with a continuous network of eutectic and...
.