.gif)
Honing (metalworking)
Encyclopedia

Abrasive machining
Abrasive machining is a machining process where material is removed from a workpiece using a multitude of small abrasive particles. Common examples include grinding, honing, and polishing...
process that produces a precision surface
Surface integrity
Surface integrity is the surface condition of a workpiece after being modified by a manufacturing process. The term was coined by Michael Field and John F. Kahles in 1964.The surface integrity of a workpiece or item changes the material's properties...
on a metal
Metal
A metal , is an element, compound, or alloy that is a good conductor of both electricity and heat. Metals are usually malleable and shiny, that is they reflect most of incident light...
workpiece by scrubbing an abrasive
Abrasive
An abrasive is a material, often a mineral, that is used to shape or finish a workpiece through rubbing which leads to part of the workpiece being worn away...
stone against it along a controlled path. Honing is primarily used to improve the geometric form of a surface, but may also improve the surface texture.
Typical applications are the finishing of cylinders
Cylinder (engine)
A cylinder is the central working part of a reciprocating engine or pump, the space in which a piston travels. Multiple cylinders are commonly arranged side by side in a bank, or engine block, which is typically cast from aluminum or cast iron before receiving precision machine work...
for internal combustion engines, air bearing spindle
Spindle (tool)
In machine tools, a spindle is a rotating axis of the machine, which often has a shaft at its heart. The shaft itself is called a spindle, but also, in shop-floor practice, the word often is used metonymically to refer to the entire rotary unit, including not only the shaft itself, but its bearings...
s and gear
Gear
A gear is a rotating machine part having cut teeth, or cogs, which mesh with another toothed part in order to transmit torque. Two or more gears working in tandem are called a transmission and can produce a mechanical advantage through a gear ratio and thus may be considered a simple machine....
s. Types of hone are many and various but all consist of one or more abrasive stones that are held under pressure
Pressure
Pressure is the force per unit area applied in a direction perpendicular to the surface of an object. Gauge pressure is the pressure relative to the local atmospheric or ambient pressure.- Definition :...
against the surface they are working on.
In everyday use, a honing steel is used to hone knives, especially kitchen knives, and is a fine process, there contrasted with more abrasive sharpening
Sharpening
Sharpening is the process of creating or refining a sharp edge of appropriate shape on a tool or implement designed for cutting. Sharpening is done by grinding away material on the implement with an abrasive substance harder than the material of the implement, followed sometimes by processes to...
.
Other similar processes are lapping
Lapping
Lapping is a machining operation, in which two surfaces are rubbed together with an abrasive between them, by hand movement or by way of a machine.This can take two forms...
and superfinishing
Superfinishing
Superfinishing, also known as micromachining and short-stroke honing, is a metalworking process that improves surface finish and workpiece geometry. This is achieved by removing just the thin amorphous surface layer left by the last process with an abrasive stone; this layer is usually about...
.
Honing stones
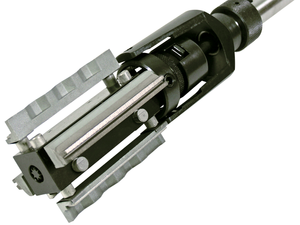

A honing stone is similar to a grinding wheel in many ways, but honing stones are usually more friable so that they conform to the shape of the workpiece as they wear in. To counteract their friability, honing stones may be treated with wax or sulfur to improve life; wax is usually preferred for environmental reasons.
Any abrasive material may be used to create a honing stone, but the most commonly used are corundum
Corundum
Corundum is a crystalline form of aluminium oxide with traces of iron, titanium and chromium. It is a rock-forming mineral. It is one of the naturally clear transparent materials, but can have different colors when impurities are present. Transparent specimens are used as gems, called ruby if red...
, silicon carbide
Silicon carbide
Silicon carbide , also known as carborundum, is a compound of silicon and carbon with chemical formula SiC. It occurs in nature as the extremely rare mineral moissanite. Silicon carbide powder has been mass-produced since 1893 for use as an abrasive...
, cubic boron nitride, or diamond
Diamond
In mineralogy, diamond is an allotrope of carbon, where the carbon atoms are arranged in a variation of the face-centered cubic crystal structure called a diamond lattice. Diamond is less stable than graphite, but the conversion rate from diamond to graphite is negligible at ambient conditions...
. The choice of abrasive material is usually driven by the characteristics of the workpiece material. In most cases, corundum or silicon carbide are acceptable, but extremely hard workpiece materials must be honed using superabrasives.
The hone is usually turned in the bore while being moved in and out. Special cutting fluid
Cutting fluid
Cutting fluid is a type of coolant and lubricant designed specifically for metalworking and machining processes. There are various kinds of cutting fluids, which include oils, oil-water emulsions, pastes, gels, aerosols , and air or other gases. They may be made from petroleum distillates, animal...
s are used to give a smooth cutting action and to remove the material that has been abraded. Machines can be portable, simple manual machines, or fully automatic with gauging
Gauge (engineering)
In engineering, a gauge or gage, is used to make measurements. A wide variety of tools exist which serve such funtions, ranging from simple pieces of material against which sizes can be measured to complex pieces of machinery...
depending on the application.
Modern advances in abrasives have made it possible to remove much larger amount of material than was previously possible. This has displaced grinding in many applications where "through machining" is possible. External hones perform the same function on shafts.
Process mechanics
Since honing stones look similar to grinding wheels, it is tempting to think of honing as a form of low-stock removal grindingGrinding (abrasive cutting)
Grinding is an abrasive machining process that uses a grinding wheel as the cutting tool.A wide variety of machines are used for grinding:* Hand-cranked knife-sharpening stones * Handheld power tools such as angle grinders and die grinders...
. Instead, it is better to think of it as a self-truing grinding process.
In grinding, the wheel follows a simple path. For example, in plunge grinding a shaft, the wheel moves in towards the axis of the part, grinds it, and then moves back out. Since each slice of the wheel repeatedly contacts the same slice of the workpiece, any inaccuracies in the geometric shape of the grinding wheel will be transferred onto the part. Therefore, the accuracy of the finished workpiece geometry is limited to the accuracy of the truing dresser. The accuracy becomes even worse as the grind wheel wears, so truing must occur periodically to reshape it.
The limitation on geometric accuracy is overcome in honing because the honing stone follows a complex path. In bore honing for example, the stone moves along two paths simultaneously. The stones are pressed radially outward to enlarge the hole while they simultaneously oscillate axially. Due to the oscillation, each slice of the honing stones touch a large area of the workpiece. Therefore, imperfections in the honing stone's profile cannot transfer to the bore. Instead both the bore and the honing stones conform to the average shape of the honing stones' motion, which in the case of bore honing is a cylinder. This averaging effect occurs in all honing processes; both the workpiece and stones erode until they conform to the average shape of the stones' cutting surface. Since the honing stones tend to erode towards a desired geometric shape, there is no need to true them. As a result of the averaging effect, the accuracy of a honed component often exceeds the accuracy of the machine tool that created it.
The path of the stone is not the only difference between grinding and honing machines, they also differ in the stiffness of their construction. Honing machines are much more compliant than grinders. The purpose of grinding is to achieve a tight size tolerance. To do this, the grinding wheel must be moved to an exact position relative to the workpiece. Therefore a grinding machine must be very stiff and its axes must move with very high precision.
A honing machine, ironically, is relatively inaccurate and compliant. Instead of relying on the accuracy of the machine tool, it relies on the averaging effect between the stone and the workpiece. In fact, compliance is a requirement of a honing machine that is necessary for the averaging effect to occur. This leads to an obvious difference between the two machines: in a grinder the stone is rigidly attached to a slide, while in honing the stone is actuated with pneumatic or hydraulic pressure.
High-precision workpieces are usually ground and then honed. Grinding determines the size, and honing improves the shape.
The difference between honing and grinding is not always distinct. Some grinders have complex movements and are self-truing, and some honing machines are equipped with in-process gaging for size control. Many through-feed grinding operations rely on the same averaging effect as honing.
Honing configurations
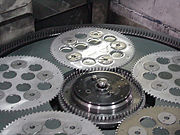
- Track/Raceway honing
- Spherical honing
- OD through-feed honing (taper and straight)
- Flat honingFlat honingFlat honing is a metalworking grinding process used to provide high quality flat surfaces. It combines the speed of grinding or honing with the precision of lapping. It has also been known under the terms high speed lapping and high precision grinding.- Origin of term :The term is derived from...
- Bore honing
Economics
Since honing is a high precision process, it is also relatively expensive. Therefore it is only used in components that demand the highest level of precision. It is typically the last manufacturing operation before the part is shipped to a customer. The dimensional size of the object is established by preceding operations, the last of which is usually grinding. Then the part is honed to improve a form characteristic such as roundness, flatness, cylindricity, or sphericity.Performance advantages of honed surfaces
Since honing is a relatively expensive manufacturing process, it can only be economically justified for applications that require very good form accuracy. The improved shape after honing may result in a quieter running or higher precision component.Cross-hatch finish
A "cross-hatch" pattern is used to retain oil or grease to ensure proper lubrication and ring seal of pistons in cylinders. A smooth glazed cylinder wall can cause piston ring and cylinder scuffing. The "cross-hatch" pattern is used on brake rotors, and flywheels.Plateau finish
A tool with the brand name Flex-Hone made by Brush Research Manufacturing Co., Inc. was introduced as a hone with many of the benefits of honing without the need for labor intensive set up or training. The tool is often referred to as a "ball-hone" for its many abrasive globules mounted to the ends of flexible nylon filament. The result of using this tool is that it provides a cross hatched finish while achieving a plateau finish at the same time.The Plateau Finish is one characterized by the removal of "peaks" in the metal while leaving the cross hatch intact for oil retention. The plateaued finish increases the bearing area of the finish, and does not require the piston or ring to "break in" the cylinder walls.