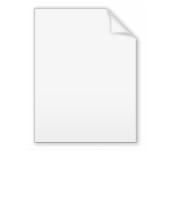
Hot metal gas forming
Encyclopedia
Hot metal gas forming is a method of die
forming in which a metal
tube is heated to a pliable state, near but below its melting point
, then pressurized internally by a gas
in order to form the tube outward into the shape defined by an enclosing die cavity. The high temperatures allow the metal to elongate, or stretch, to much greater degrees without rupture than are possible in previously utilized cold and warm forming methods. In addition, the metal can be formed into finer details and requires less overall forming force than traditional methods.
, hot blow forming, and hydroforming
.
Complex tubes can be made from multiple sheet components formed and welded together, but this adds unnecessary cost and creates quality concerns at the joints. Hydroforming uses liquid under extreme pressures to form metal tubes. It was developed for the plumbing industry and by 1990 achieved production efficiencies suited for high volume autos. Typically hydroforming is done at ambient temperatures, and limits the forming elongation of metals to 8‐12% diameter increase for aluminum, and 25‐40% for steel
. This limits the part shape complexity that can be produced. In addition, the workcenters and tooling can be large and expensive because of the internal fluid pressures required to form ambient tubes.
Blow forming started with glass
long ago, and is now a widespread method for forming plastic into hollow structures. Again, the heated material properties provide for many processing advantages. Warm forming, defined as forming above ambient but below the recrystallization temperature of an alloy, has been the subject of extensive research in the past decades. Warm forming, using hydroform principles can be done on tubes. Temperatures are typically limited due to safety concerns surrounding the heated forming fluids. At these temperatures, cycle times may still be relatively long, and elongation
s still do not approach that of hot forming.
As a natural evolution, the need for HMGF created research starting in the 1990s. Fast cycle times, inexpensive tooling and machinery resulting from pressures an order of magnitude lower than hydroforming, and extreme forming ratios due to high temperature forming create a compelling business case for high volume low cost manufacturing.
In 1999, development of the HMGF techniques began as an Advanced Technology Program
(ATP) project funded by the US National Institute of Standards and Technology
(NIST). This project completed in 1993 and research showed up to 150% expansion ratios for aluminum and 50% with steel were possible, with further expansion capabilities by use of end feeding of material to minimize wall thinning.
In order to keep pace with the US research, a European project was funded by the Research Fund for Coal and Steel (RFCS). Starting in July 2004, with a duration of 3 years, this project further investigated the HMGF process. By 2007, the consortium of European research and commercial entities proved concepts of simpler heating and die construction, and while focusing on the more demanding steel alloys, illustrated free deformation of 140% by use of end feeding to control wall thinning and delay rupture. The method used in these experiments is patented under .
Also in Europe, parallel research yielded an innovative approach to the concept. By 2006, the HEATform method of hot metal gas forming showed evidence of unique metal shapes that had “historically only been possible in the domain of glass blowing and blow molded parts” with aluminum forming in excess of 270% expansion ratio at a production intended cycle time of 20 seconds. Citing that hardening and subsequent breakage will limit forming of the aluminum alloy below 460 °C (860 °F), the best flow behavior was observed at 550 °C (1,022 °F). This is significantly higher than the capabilities of warm liquid or warm gas pressure forming. The HEATform techniques of end feeding control achieved uniform wall thickness up to 300% strain values.
While significant research into material compatibility and predictive analysis techniques is ongoing, hot metal gas forming has been commercialized by at least one company who is providing hot expansion coupled with material end feeding.
and aerospace industries where the precursor technology of hydroforming is well known. Other applications include sports equipment
and furniture
. The multi-material capability are used in decorative workpieces and plumbing fixture
s.
, however with HMFG a less expensive alloy can be used, which reduces piece prices. One example is the use of ferritic stainless steels, like the 1.4512 alloy for exhaust components. Typically, the more expensive austenitic stainless
is chosen, like the 1.4301 alloy, for parts requiring complex forming due to its 40% advantage in ambient formability (38.5% vs. 27.4% typical A%).
Die (manufacturing)
A die is a specialized tool used in manufacturing industries to cut or shape material using a press. Like molds, dies are generally customized to the item they are used to create...
forming in which a metal
Metal
A metal , is an element, compound, or alloy that is a good conductor of both electricity and heat. Metals are usually malleable and shiny, that is they reflect most of incident light...
tube is heated to a pliable state, near but below its melting point
Melting point
The melting point of a solid is the temperature at which it changes state from solid to liquid. At the melting point the solid and liquid phase exist in equilibrium. The melting point of a substance depends on pressure and is usually specified at standard atmospheric pressure...
, then pressurized internally by a gas
Gas
Gas is one of the three classical states of matter . Near absolute zero, a substance exists as a solid. As heat is added to this substance it melts into a liquid at its melting point , boils into a gas at its boiling point, and if heated high enough would enter a plasma state in which the electrons...
in order to form the tube outward into the shape defined by an enclosing die cavity. The high temperatures allow the metal to elongate, or stretch, to much greater degrees without rupture than are possible in previously utilized cold and warm forming methods. In addition, the metal can be formed into finer details and requires less overall forming force than traditional methods.
History
HMGF is an evolution that further improves upon the cost effectiveness and applicability of several existing commercial processes: superplastic formingSuperplastic forming
Superplastic forming is a metalworking process for forming sheet metal. It works upon the theory of superplasticity, which means that a material can elongate beyond 100% of its original size.-Process:...
, hot blow forming, and hydroforming
Hydroforming
Hydroforming is a cost-effective way of shaping malleable metals such as aluminum or brass into lightweight, structurally stiff and strong pieces. One of the largest applications of hydroforming is the automotive industry, which makes use of the complex shapes possible by hydroforming to produce...
.
Complex tubes can be made from multiple sheet components formed and welded together, but this adds unnecessary cost and creates quality concerns at the joints. Hydroforming uses liquid under extreme pressures to form metal tubes. It was developed for the plumbing industry and by 1990 achieved production efficiencies suited for high volume autos. Typically hydroforming is done at ambient temperatures, and limits the forming elongation of metals to 8‐12% diameter increase for aluminum, and 25‐40% for steel
Steel
Steel is an alloy that consists mostly of iron and has a carbon content between 0.2% and 2.1% by weight, depending on the grade. Carbon is the most common alloying material for iron, but various other alloying elements are used, such as manganese, chromium, vanadium, and tungsten...
. This limits the part shape complexity that can be produced. In addition, the workcenters and tooling can be large and expensive because of the internal fluid pressures required to form ambient tubes.
Blow forming started with glass
Glass
Glass is an amorphous solid material. Glasses are typically brittle and optically transparent.The most familiar type of glass, used for centuries in windows and drinking vessels, is soda-lime glass, composed of about 75% silica plus Na2O, CaO, and several minor additives...
long ago, and is now a widespread method for forming plastic into hollow structures. Again, the heated material properties provide for many processing advantages. Warm forming, defined as forming above ambient but below the recrystallization temperature of an alloy, has been the subject of extensive research in the past decades. Warm forming, using hydroform principles can be done on tubes. Temperatures are typically limited due to safety concerns surrounding the heated forming fluids. At these temperatures, cycle times may still be relatively long, and elongation
Elongation
In astronomy, a planet's elongation is the angle between the Sun and the planet, as viewed from Earth. Elongations occur when an inner planet’s position, in its orbital path, is at tangent to the view from Earth. Because these inner planets are inside the Earth’s orbits their positions as viewed...
s still do not approach that of hot forming.
As a natural evolution, the need for HMGF created research starting in the 1990s. Fast cycle times, inexpensive tooling and machinery resulting from pressures an order of magnitude lower than hydroforming, and extreme forming ratios due to high temperature forming create a compelling business case for high volume low cost manufacturing.
In 1999, development of the HMGF techniques began as an Advanced Technology Program
Advanced Technology Program
The NIST Advanced Technology Program is a United States Government program designed to simulate early stage advanced technology development that would otherwise not be fundable.ATP unique in that it is designed for early stage research in industry, not academia, though it...
(ATP) project funded by the US National Institute of Standards and Technology
National Institute of Standards and Technology
The National Institute of Standards and Technology , known between 1901 and 1988 as the National Bureau of Standards , is a measurement standards laboratory, otherwise known as a National Metrological Institute , which is a non-regulatory agency of the United States Department of Commerce...
(NIST). This project completed in 1993 and research showed up to 150% expansion ratios for aluminum and 50% with steel were possible, with further expansion capabilities by use of end feeding of material to minimize wall thinning.
In order to keep pace with the US research, a European project was funded by the Research Fund for Coal and Steel (RFCS). Starting in July 2004, with a duration of 3 years, this project further investigated the HMGF process. By 2007, the consortium of European research and commercial entities proved concepts of simpler heating and die construction, and while focusing on the more demanding steel alloys, illustrated free deformation of 140% by use of end feeding to control wall thinning and delay rupture. The method used in these experiments is patented under .
Also in Europe, parallel research yielded an innovative approach to the concept. By 2006, the HEATform method of hot metal gas forming showed evidence of unique metal shapes that had “historically only been possible in the domain of glass blowing and blow molded parts” with aluminum forming in excess of 270% expansion ratio at a production intended cycle time of 20 seconds. Citing that hardening and subsequent breakage will limit forming of the aluminum alloy below 460 °C (860 °F), the best flow behavior was observed at 550 °C (1,022 °F). This is significantly higher than the capabilities of warm liquid or warm gas pressure forming. The HEATform techniques of end feeding control achieved uniform wall thickness up to 300% strain values.
While significant research into material compatibility and predictive analysis techniques is ongoing, hot metal gas forming has been commercialized by at least one company who is providing hot expansion coupled with material end feeding.
Applications
Typical applications are in the automotiveAutomotive industry
The automotive industry designs, develops, manufactures, markets, and sells motor vehicles, and is one of the world's most important economic sectors by revenue....
and aerospace industries where the precursor technology of hydroforming is well known. Other applications include sports equipment
Sports equipment
Sports equipment is a general term for any object used for sport or exercise. Examples of sports equipment include:-Exercise equipment:Examples for exercise include swiss balls, weights, equipment for the gym...
and furniture
Furniture
Furniture is the mass noun for the movable objects intended to support various human activities such as seating and sleeping in beds, to hold objects at a convenient height for work using horizontal surfaces above the ground, or to store things...
. The multi-material capability are used in decorative workpieces and plumbing fixture
Plumbing fixture
A plumbing fixture is an exchangeable device which can be connected to an existing plumbing system to deliver and drain away water but which is also configured to enable a particular use.-Common fixtures:The most common plumbing fixtures are:*Bathtubs...
s.
Materials
The HMGF process is compatible with almost any metal. The most significant benefit of HMGF is that cold form resistant materials become viable for complex forming. Often, alloys are enhanced with expensive materials to enable cold forming and increase machinabilityMachinability
The term machinability refers to the ease with which a metal can be machined to an acceptable surface finish. Materials with good machinability require little power to cut, can be cut quickly, easily obtain a good finish, and do not wear the tooling much; such materials are said to be free machining...
, however with HMFG a less expensive alloy can be used, which reduces piece prices. One example is the use of ferritic stainless steels, like the 1.4512 alloy for exhaust components. Typically, the more expensive austenitic stainless
Stainless
Stainless may refer to:* Stainless steel, a corrosion-resistant metal alloy* Stainless Games, a British video game developer* Stainless Broadcasting Company, a TV broadcaster based in Michigan, US...
is chosen, like the 1.4301 alloy, for parts requiring complex forming due to its 40% advantage in ambient formability (38.5% vs. 27.4% typical A%).