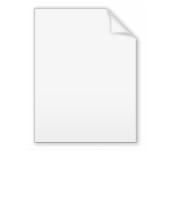
Knifemaking
Encyclopedia
Knife making is the process of manufacturing a knife
by any one or a combination of processes: stock removal
, forging to shape
, welded lamination
or investment cast
. Typical metals used come from the carbon steel, tool
, or stainless steel
families. Primitive knives have been made from bronze, copper, brass, iron, obsidian, and flint.
Unusual non-metallic materials may also be used; manufacturing techniques are quite different from metal:
or blanking
.
When forging, the blade material is heated to a high temperature or forging temperature in a forge
and shaped with a hammer on an anvil
to achieve the desired shape, often to near final dimension, where very little stock removal, if any, is required to finish. Steel can be folded either to form decorative pattern welded steel
or to refine raw steel, or as the Japanese call it, tamahagane. Grain size is kept at a minimum as grain growth can happen quite easily if the blade material is overheated. Randall Made Knives
forges all of their blade material in-house.
In a mass production environment, or in a well equipped private shop, the blanking process is used to make "blade blanks". This can be achieved by a number of different methods, depending upon the thickness of the material and the alloy content of steel to be cut. Thinner cross section, lower alloy blanks can be stamped from sheet material. Materials that are more difficult to work with, or jobs that require higher production volume, can be accomplished with water jet cutter
s, laser
s or electron beam cutting. These two lend themselves towards larger custom shops. Some custom knife makers cut their blanks from steel using a metal-cutting bandsaw.
Knife makers will sometimes contract out to a shop with the above capabilities to do blanking. For lower production makers, or lower budgets, other methods must suffice. Knife makers may use many different methods to profile a blank. These can include hacksaw
s, file
s, belt grinder
s, wheel grinders, oxy-acetylene torches, CNC mills, or any number of other methods depending on budget.
Knife
A knife is a cutting tool with an exposed cutting edge or blade, hand-held or otherwise, with or without a handle. Knives were used at least two-and-a-half million years ago, as evidenced by the Oldowan tools...
by any one or a combination of processes: stock removal
Stock removal
High stock removal is a technological process with the goal to remove large / substantial amounts of material. The quantity of material, which can be removed in a specific process, depends on the material properties and the machining tool used.-Materials:...
, forging to shape
Bladesmith
Bladesmithing is the art of making knives, swords, daggers and other blades using a forge, hammer, anvil, and other smithing tools. Bladesmiths employ a variety of metalworking techniques similar to those used by blacksmiths, as well as woodworking for knife and sword handles, and often...
, welded lamination
Damascus steel
Damascus steel was a term used by several Western cultures from the Medieval period onward to describe a type of steel used in swordmaking from about 300 BCE to 1700 CE. These swords are characterized by distinctive patterns of banding and mottling reminiscent of flowing water...
or investment cast
Investment casting
Investment casting is an industrial process based on and also called lost-wax casting, one of the oldest known metal-forming techniques. From 5,000 years ago, when beeswax formed the pattern, to today’s high-technology waxes, refractory materials and specialist alloys, the castings allow the...
. Typical metals used come from the carbon steel, tool
Tool steel
Tool steel refers to a variety of carbon and alloy steels that are particularly well-suited to be made into tools. Their suitability comes from their distinctive hardness, resistance to abrasion, their ability to hold a cutting edge, and/or their resistance to deformation at elevated temperatures...
, or stainless steel
Stainless steel
In metallurgy, stainless steel, also known as inox steel or inox from French "inoxydable", is defined as a steel alloy with a minimum of 10.5 or 11% chromium content by mass....
families. Primitive knives have been made from bronze, copper, brass, iron, obsidian, and flint.
Materials for blades
Different steels are suited to different applications. There is a trade off between hardness, toughness, edge retention, corrosion resistance, and achievable sharpness. Some examples of blade material and their relative trade offs:- The newest powder metallurgyPowder metallurgyPowder metallurgy is the process of blending fine powdered materials, pressing them into a desired shape , and then heating the compressed material in a controlled atmosphere to bond the material . The powder metallurgy process generally consists of four basic steps: powder manufacture, powder...
steels can be made very hard, but can quickly wear out abrasives and tooling.
- A blade made from low carbon or mild steel would be inexpensive to produce and of poor quality. A low carbon blade would be very hard to break, but would bend easily and be too soft to hold an edge. High carbon (or high alloy, in some listings) can take a much higher hardness but must be tempered carefully after heat treatment to avoid brittleness.
Unusual non-metallic materials may also be used; manufacturing techniques are quite different from metal:
- The natural volcanic glass obsidianObsidianObsidian is a naturally occurring volcanic glass formed as an extrusive igneous rock.It is produced when felsic lava extruded from a volcano cools rapidly with minimum crystal growth...
can achieve a nearly molecular edge (high achievable sharpness) and only requires stone ageStone AgeThe Stone Age is a broad prehistoric period, lasting about 2.5 million years , during which humans and their predecessor species in the genus Homo, as well as the earlier partly contemporary genera Australopithecus and Paranthropus, widely used exclusively stone as their hard material in the...
technology to work, but is so brittle that it cannot maintain that sharpness for very long. Also the entire blade is very easy to break by accident. Obsidian is used to make extremely sharp surgical scalpelScalpelA scalpel, or lancet, is a small and extremely sharp bladed instrument used for surgery, anatomical dissection, and various arts and crafts . Scalpels may be single-use disposable or re-usable. Re-usable scalpels can have attached, resharpenable blades or, more commonly, non-attached, replaceable...
s. - Ceramic knivesCeramic knifeA ceramic knife is a knife made out of very hard and tough ceramic, often zirconium dioxide . These knives are usually produced by dry pressing zirconia powder and firing them through solid-state sintering. The resultant blade is sharpened by grinding the edges with a diamond-dust-coated grinding...
hold their edge for a long time, but are brittle.
Initial shaping
The initial shaping of a knife is done through forgingForging
Forging is a manufacturing process involving the shaping of metal using localized compressive forces. Forging is often classified according to the temperature at which it is performed: '"cold," "warm," or "hot" forging. Forged parts can range in weight from less than a kilogram to 580 metric tons...
or blanking
Blanking (metalworking)
Blanking and piercing are shearing processes in which a punch and die are used to modify webs. The tooling and processes are the same between the two, only the terminology is different: in blanking the punched out piece is used and called a blank; in piercing the punched out piece is...
.
When forging, the blade material is heated to a high temperature or forging temperature in a forge
Forge
A forge is a hearth used for forging. The term "forge" can also refer to the workplace of a smith or a blacksmith, although the term smithy is then more commonly used.The basic smithy contains a forge, also known as a hearth, for heating metals...
and shaped with a hammer on an anvil
Anvil
An anvil is a basic tool, a block with a hard surface on which another object is struck. The inertia of the anvil allows the energy of the striking tool to be transferred to the work piece. In most cases the anvil is used as a forging tool...
to achieve the desired shape, often to near final dimension, where very little stock removal, if any, is required to finish. Steel can be folded either to form decorative pattern welded steel
Pattern welding
Pattern welding is the practice in sword and knife making of forming a blade of several metal pieces of differing composition that are forge-welded together and twisted and manipulated to form a pattern. Often called Damascus steel, blades forged in this manner often display bands of slightly...
or to refine raw steel, or as the Japanese call it, tamahagane. Grain size is kept at a minimum as grain growth can happen quite easily if the blade material is overheated. Randall Made Knives
Randall Made Knives
Randall Made Knives, usually referred to as Randall, is an American manufacturer specializing in custom handcrafted knives founded by Walter Doane "Bo" Randall, Jr. The factory and showroom is located in Orlando, Florida. Randall offers 28 models of knives for different applications, each...
forges all of their blade material in-house.
In a mass production environment, or in a well equipped private shop, the blanking process is used to make "blade blanks". This can be achieved by a number of different methods, depending upon the thickness of the material and the alloy content of steel to be cut. Thinner cross section, lower alloy blanks can be stamped from sheet material. Materials that are more difficult to work with, or jobs that require higher production volume, can be accomplished with water jet cutter
Water jet cutter
A water jet cutter, also known as a waterjet, is a tool capable of slicing into metal or other materials using a jet of water at high velocity and pressure, or a mixture of water and an abrasive substance. The process is essentially the same as water erosion found in nature but greatly accelerated...
s, laser
Laser
A laser is a device that emits light through a process of optical amplification based on the stimulated emission of photons. The term "laser" originated as an acronym for Light Amplification by Stimulated Emission of Radiation...
s or electron beam cutting. These two lend themselves towards larger custom shops. Some custom knife makers cut their blanks from steel using a metal-cutting bandsaw.
Knife makers will sometimes contract out to a shop with the above capabilities to do blanking. For lower production makers, or lower budgets, other methods must suffice. Knife makers may use many different methods to profile a blank. These can include hacksaw
Hacksaw
A hacksaw is a fine-tooth saw with a blade under tension in a frame, used for cutting materials such as metal or plastics. Hand-held hacksaws consist of a metal arch with a handle, usually a pistol grip, with pins for attaching a narrow disposable blade. A screw or other mechanism is used to put...
s, file
File (tool)
A file is a metalworking and woodworking tool used to cut fine amounts of material from a workpiece. It most commonly refers to the hand tool style, which takes the form of a steel bar with a case hardened surface and a series of sharp, parallel teeth. Most files have a narrow, pointed tang at one...
s, belt grinder
Grinding machine
A grinding machine, often shortened to grinder, is a machine tool used for grinding, which is a type of machining using an abrasive wheel as the cutting tool...
s, wheel grinders, oxy-acetylene torches, CNC mills, or any number of other methods depending on budget.