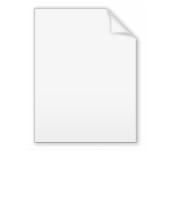
Metallurgical failure analysis
Encyclopedia
Metallurgical failure analysis is the process by which a metallurgist determines the mechanism that has caused a metal
component to fail. Typical failure modes involve various types of corrosion
and mechanical damage. It has been estimated that the direct annual cost of corrosion alone in the United States
is a staggering 276 billion, approximately 3.1% of GDP.
Metal components fail as a result of the environmental conditions to which they are exposed to as well as the mechanical stresses that they experience. Often a combination of both environmental conditions and stress will cause failure.
Metal components are designed to withstand the environment and stresses that they will be subjected to. The design of a metal component involves not only a specific elemental composition but also specific manufacturing processes such as heat treatments, machining
processes, etc.… The huge arrays of different metals that result all have unique physical properties. Specific properties are designed into metal components to make them more robust to various environmental conditions. These differences in physical properties will exhibit unique failure modes. A metallurgical failure analysis
takes into account as much of this information as possible during analysis.
Analysis of a failed part can be done using destructive testing
or non-destructive testing. Destructive testing involves removing a metal component from service and sectioning the component for analysis. Destructive testing gives the failure analyst the ability to conduct the analysis in a laboratory
setting and perform tests on the material that will ultimately destroy the component. Non destructive testing is a test method that allows certain physical properties of metal to be examined without taking the samples completely out of service. NDT is generally used to detect failures in components before the component fails catastrophically.
There is no standardized list of metallurgical failure mode
s and different metallurgists might use a different name for the same failure mode. The Failure Mode Terms listed below are those accepted by ASTM, ASM
, and/or NACE
as distinct metallurgical failure mechanisms.
Metal
A metal , is an element, compound, or alloy that is a good conductor of both electricity and heat. Metals are usually malleable and shiny, that is they reflect most of incident light...
component to fail. Typical failure modes involve various types of corrosion
Corrosion
Corrosion is the disintegration of an engineered material into its constituent atoms due to chemical reactions with its surroundings. In the most common use of the word, this means electrochemical oxidation of metals in reaction with an oxidant such as oxygen...
and mechanical damage. It has been estimated that the direct annual cost of corrosion alone in the United States
United States
The United States of America is a federal constitutional republic comprising fifty states and a federal district...
is a staggering 276 billion, approximately 3.1% of GDP.
Metal components fail as a result of the environmental conditions to which they are exposed to as well as the mechanical stresses that they experience. Often a combination of both environmental conditions and stress will cause failure.
Metal components are designed to withstand the environment and stresses that they will be subjected to. The design of a metal component involves not only a specific elemental composition but also specific manufacturing processes such as heat treatments, machining
Machining
Conventional machining is a form of subtractive manufacturing, in which a collection of material-working processes utilizing power-driven machine tools, such as saws, lathes, milling machines, and drill presses, are used with a sharp cutting tool to physical remove material to achieve a desired...
processes, etc.… The huge arrays of different metals that result all have unique physical properties. Specific properties are designed into metal components to make them more robust to various environmental conditions. These differences in physical properties will exhibit unique failure modes. A metallurgical failure analysis
Failure analysis
Failure analysis is the process of collecting and analyzing data to determine the cause of a failure. It is an important discipline in many branches of manufacturing industry, such as the electronics industry, where it is a vital tool used in the development of new products and for the improvement...
takes into account as much of this information as possible during analysis.
Analysis of a failed part can be done using destructive testing
Destructive testing
In destructive testing, tests are carried out to the specimen's failure, in order to understand a specimen's structural performance or material behaviour under different loads...
or non-destructive testing. Destructive testing involves removing a metal component from service and sectioning the component for analysis. Destructive testing gives the failure analyst the ability to conduct the analysis in a laboratory
Laboratory
A laboratory is a facility that provides controlled conditions in which scientific research, experiments, and measurement may be performed. The title of laboratory is also used for certain other facilities where the processes or equipment used are similar to those in scientific laboratories...
setting and perform tests on the material that will ultimately destroy the component. Non destructive testing is a test method that allows certain physical properties of metal to be examined without taking the samples completely out of service. NDT is generally used to detect failures in components before the component fails catastrophically.
There is no standardized list of metallurgical failure mode
Failure mode
Failure causes are defects in design, process, quality, or part application, which are the underlying cause of a failure or which initiate a process which leads to failure. Where failure depends on the user of the product or process, then human error must be considered.-Component failure:A part...
s and different metallurgists might use a different name for the same failure mode. The Failure Mode Terms listed below are those accepted by ASTM, ASM
ASM
ASM may refer to:Codes:* American Samoa using ISO 3166-1 alpha-3 country code* Asmara International Airport * Assamese language Computer science:...
, and/or NACE
NACE
NACE may refer to:* National Association of Colleges and Employers* National Association of Corrosion Engineers* Nomenclature statistique des activités économiques dans la Communauté européenne * National Association for Able Children in Education* National Association of Chimney Engineers...
as distinct metallurgical failure mechanisms.
Metallurgical Failure Modes Caused By Corrosion and Stress
- Stress Corrosion CrackingStress corrosion crackingStress corrosion cracking is the unexpected sudden failure of normally ductile metals subjected to a tensile stress in a corrosive environment, especially at elevated temperature in the case of metals. SCC is highly chemically specific in that certain alloys are likely to undergo SCC only when...
- Corrosion FatigueCorrosion fatigueCorrosion fatigue is fatigue in a corrosive environment. It is the mechanical degradation of a material under the joint action of corrosion and cyclic loading. Nearly all engineering structures experience some form of alternating stress, and are exposed to harmful environments during their service...
- Caustic Cracking (ASTM term)
- Caustic EmbrittlementCaustic embrittlementCaustic embrittlement is the phenomenon in which the material of a boiler becomes brittle due to the accumulation of caustic substances.-Cause:...
(ASM term) - Stress Corrosion (NACE term)
- Sulfide Stress Cracking (ASM, NACE term)
- Stress Accelerated Corrosion (NACE term)
- Hydrogen Stress Cracking (ASM term)
- Hydrogen Assisted Stress Corrosion Cracking (ASM term)
Metallurgical Failure Modes Caused By Stress
- FatigueFatigue (material)'In materials science, fatigue is the progressive and localized structural damage that occurs when a material is subjected to cyclic loading. The nominal maximum stress values are less than the ultimate tensile stress limit, and may be below the yield stress limit of the material.Fatigue occurs...
(ASTM, ASM term) - Mechanical OverloadMechanical overloadThe failure or fracture of a product or component in a single event is known as mechanical overload. It is a common failure mode, and may be contrasted with fatigue, creep, rupture, or stress relaxation. The terms are used in forensic engineering and structural engineering when analysing product...
- CreepCreepCreep may refer to:* CREEP, the Committee for the Re-Election of the President, associated with the Watergate scandal of U.S. president Nixon's administration....
- Rupture
- Cracking (NACE term)
- Embrittlement
Metallurgical Failure Modes Caused by Corrosion
- Erosion CorrosionErosion corrosionErosion corrosion is a degradation of material surface due to mechanical action, often by impinging liquid, abrasion by a slurry, particles suspended in fast flowing liquid or gas, bubbles or droplets, cavitation, etc...
- Oxygen Pitting
- Hydrogen EmbrittlementHydrogen embrittlementHydrogen embrittlement is the process by which various metals, most importantly high-strength steel, become brittle and fracture following exposure to hydrogen...
- Hydrogen Induced Cracking (ASM term)
- Corrosion Embrittlement (ASM term)
- Hydrogen Disintegration (NACE term)
- Hydrogen Assisted Cracking (ASM term)
- Hydrogen Blistering
- Corrosion