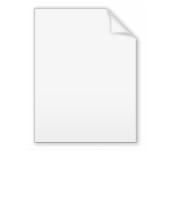
Piezoelectric accelerometer
Encyclopedia
A piezoelectric accelerometer
that utilizes the piezoelectric effect of certain materials to measure dynamic changes in mechanical variables. (e.g. acceleration, vibration, and mechanical shock)
As with all transducers, piezoelectric accelerometers convert one form of energy into another and provide an electrical signal in response to a quantity, property, or condition that is being measured. Using the general sensing method upon which all accelerometers are based, acceleration acts upon a seismic mass that is restrained by a spring or suspended on a cantilever beam, and converts a physical force into an electrical signal. Before the acceleration can be converted into an electrical quantity it must first be converted into either a force
or displacement
. This conversion is done via the mass spring system shown in the figure to the right.
). The force exerted on the piezoelectric material can be observed in the change in the electrostatic force or voltage generated by the piezoelectric material. This differs from a piezoresistive effect in that piezoresistive materials experience a change in the resistance of the material rather than a change in charge or voltage. Physical force exerted on the piezoelectric can be classified as one of two types; bending or compression. Stress of the compression type can be understood as a force exerted to one side of the piezoelectric while the opposing side rests against a fixed surface, while bending involves a force being exerted on the piezoelectric from both sides.
Piezoelectric materials used for the purpose of accelerometers can also fall into two categories. The first, and more widely used, is single-crystal materials (usually quartz). Though these materials do offer a long life span in terms of sensitivity, their disadvantage is that they are generally less sensitive than some piezoelectric ceramics. In addition to having a higher piezoelectric constant (sensitivity) than single-crystal materials, ceramics are more inexpensive to produce. The other category is ceramic material. That uses barium titanate
, lead-zirconate-lead-titanate, lead metaniobate, and other materials whose composition is considered proprietary by the company responsible for their development. The disadvantage to piezoelectric ceramics, however, is that their sensitivity degrades with time making the longevity of the device less than that of single-crystal materials.
In applications when low sensitivity piezoelectrics are used, two or more crystals can be connected together for output multiplication. The proper material can be chosen for particular applications based on the sensitivity
, frequency response
, bulk-resistivity, and thermal response. Due to the low output signal and high output impedance
that piezoelectric accelerometers possess, there is a need for amplification and impedance conversion of the signal produced. In the past this problem has been solved using a separate (external) amplifier
/impedance
converter. This method, however, is generally impractical due to the noise
that is introduced as well as the physical and environmental constraints posed on the system as a result. Today IC
amplifiers/impedance converters are commercially available and are generally packaged within the case of the accelerometer itself.
and Jacques Curie
published an experimental demonstration connecting mechanical stress and surface charge on a crystal. This phenomenon became known as the piezoelectric effect
. Closely related to this phenomenon is the Curie point
, named for the physicist Pierre Curie, which is the temperature above which piezoelectric material loses spontaneous polarization of its atoms.
The development of the commercial piezoelectric accelerometer came about through a number of attempts to find the most effective method to measure the vibration on large structures such as bridges and on vehicles in motion such as aircraft. One attempt involved using the resistance strain gage as a device to build an accelerometer. Incidentally, it was Hans J. Meier who, through his work at MIT, is given credit as the first to construct a commercial strain gage accelerometer (circa 1938). However, the strain gage accelerometers were fragile and could only produce low resonant frequencies and they also exhibited a low frequency response. These limitations in dynamic range
made it unsuitable for testing naval aircraft structures. On the other hand, the piezoelectric sensor
was proven to be a much better choice over the strain gage in designing an accelerometer. The high modulus of elasticity of piezoelectric materials makes the piezoelectric sensor a more viable solution to the problems identified with the strain gage accelerometer.
Simply stated, the inherent properties of the piezoelectric accelerometers made it a much better alternative to the strain gage types because of its high frequency response, and its ability to generate high resonant frequencies. The piezoelectric accelerometer allowed for a reduction in its physical size at the manufacturing level and it also provided for a higher g
(standard gravity) capability relative to the strain gage type. By comparison, the strain gage type exhibited a flat frequency response above 200 Hz while the piezoelectric type provided a flat response up to 10,000 Hz. These improvements made it possible for measuring the high frequency vibrations associated with the quick movements and short duration shocks of aircraft which before was not possible with the strain gage types. Before long, the technological benefits of the piezoelectric accelerometer became apparent and in the late 1940’s, large scale production of piezoelectric accelerometers began. Today, piezoelectric accelerometers are used for instrumentation in the fields of engineering, health and medicine, aeronautics and many other different industries.
Manufacturing an accelerometer that uses piezoresistance first starts with a semiconductor layer that is attached to a handle wafer by a thick oxide layer. The semiconductor layer is then patterned to the accelerometer’s geometry. This semiconductor layer has one or more apertures so that the underlying mass will have the corresponding apertures. Next the semiconductor layer is used as a mask to etch out a cavity in the underlying thick oxide. A mass in the cavity is supported in cantilever fashion by the piezoresistant arms of the semiconductor layer. Directly below the accelerometer’s geometry is a flex cavity that allows the mass in the cavity to flex or move in direction that is orthogonal to the surface of the accelerometer.
Accelerometers based upon piezoelectricity are constructed with two piezoelectric transducers. The unit consists of a hollow tube that is sealed by a piezoelectric transducer on each end. The transducers are oppositely polarized and are selected to have a specific series capacitance. The tube is then partially filled with a heavy liquid and the accelerometer is excited. While excited the total output voltage is continuously measured and the volume of the heavy liquid is microadjusted until the desired output voltage is obtained. Finally the outputs of the individual transducers are measured, the residual voltage difference is tabulated, and the dominate transducer is identified.
Accelerometer
An accelerometer is a device that measures proper acceleration, also called the four-acceleration. This is not necessarily the same as the coordinate acceleration , but is rather the type of acceleration associated with the phenomenon of weight experienced by a test mass that resides in the frame...
that utilizes the piezoelectric effect of certain materials to measure dynamic changes in mechanical variables. (e.g. acceleration, vibration, and mechanical shock)
As with all transducers, piezoelectric accelerometers convert one form of energy into another and provide an electrical signal in response to a quantity, property, or condition that is being measured. Using the general sensing method upon which all accelerometers are based, acceleration acts upon a seismic mass that is restrained by a spring or suspended on a cantilever beam, and converts a physical force into an electrical signal. Before the acceleration can be converted into an electrical quantity it must first be converted into either a force
Force
In physics, a force is any influence that causes an object to undergo a change in speed, a change in direction, or a change in shape. In other words, a force is that which can cause an object with mass to change its velocity , i.e., to accelerate, or which can cause a flexible object to deform...
or displacement
Displacement (vector)
A displacement is the shortest distance from the initial to the final position of a point P. Thus, it is the length of an imaginary straight path, typically distinct from the path actually travelled by P...
. This conversion is done via the mass spring system shown in the figure to the right.
Introduction
The word piezoelectric finds its roots in the Greek word piezein, which means to squeeze or press. When a physical force is exerted on the accelerometer, the seismic mass loads the piezoelectric element according to Newton’s second law of motion (
Piezoelectric materials used for the purpose of accelerometers can also fall into two categories. The first, and more widely used, is single-crystal materials (usually quartz). Though these materials do offer a long life span in terms of sensitivity, their disadvantage is that they are generally less sensitive than some piezoelectric ceramics. In addition to having a higher piezoelectric constant (sensitivity) than single-crystal materials, ceramics are more inexpensive to produce. The other category is ceramic material. That uses barium titanate
Barium titanate
Barium titanate is the inorganic compound with the chemical formula BaTiO3. Barium titanate is a white powder and transparent as larger crystals...
, lead-zirconate-lead-titanate, lead metaniobate, and other materials whose composition is considered proprietary by the company responsible for their development. The disadvantage to piezoelectric ceramics, however, is that their sensitivity degrades with time making the longevity of the device less than that of single-crystal materials.
In applications when low sensitivity piezoelectrics are used, two or more crystals can be connected together for output multiplication. The proper material can be chosen for particular applications based on the sensitivity
Sensitivity (electronics)
The sensitivity of an electronic device, such as a communications system receiver, or detection device, such as a PIN diode, is the minimum magnitude of input signal required to produce a specified output signal having a specified signal-to-noise ratio, or other specified criteria.Sensitivity is...
, frequency response
Frequency response
Frequency response is the quantitative measure of the output spectrum of a system or device in response to a stimulus, and is used to characterize the dynamics of the system. It is a measure of magnitude and phase of the output as a function of frequency, in comparison to the input...
, bulk-resistivity, and thermal response. Due to the low output signal and high output impedance
Output impedance
The output impedance, source impedance, or internal impedance of an electronic device is the opposition exhibited by its output terminals to an alternating current of a particular frequency as a result of resistance, inductance and capacitance...
that piezoelectric accelerometers possess, there is a need for amplification and impedance conversion of the signal produced. In the past this problem has been solved using a separate (external) amplifier
Amplifier
Generally, an amplifier or simply amp, is a device for increasing the power of a signal.In popular use, the term usually describes an electronic amplifier, in which the input "signal" is usually a voltage or a current. In audio applications, amplifiers drive the loudspeakers used in PA systems to...
/impedance
Electrical impedance
Electrical impedance, or simply impedance, is the measure of the opposition that an electrical circuit presents to the passage of a current when a voltage is applied. In quantitative terms, it is the complex ratio of the voltage to the current in an alternating current circuit...
converter. This method, however, is generally impractical due to the noise
Noise
In common use, the word noise means any unwanted sound. In both analog and digital electronics, noise is random unwanted perturbation to a wanted signal; it is called noise as a generalisation of the acoustic noise heard when listening to a weak radio transmission with significant electrical noise...
that is introduced as well as the physical and environmental constraints posed on the system as a result. Today IC
Integrated circuit
An integrated circuit or monolithic integrated circuit is an electronic circuit manufactured by the patterned diffusion of trace elements into the surface of a thin substrate of semiconductor material...
amplifiers/impedance converters are commercially available and are generally packaged within the case of the accelerometer itself.
History
Behind the mystery of the operation of the piezoelectric accelerometer lie some very fundamental concepts governing the behavior of crystallographic structures. In 1880, PierrePierre Curie
Pierre Curie was a French physicist, a pioneer in crystallography, magnetism, piezoelectricity and radioactivity, and Nobel laureate. He was the son of Dr. Eugène Curie and Sophie-Claire Depouilly Curie ...
and Jacques Curie
Jacques Curie
Paul-Jacques Curie was a French physicist and professor at the University of Montpellier. He and his brother, Pierre Curie, studied pyroelectricity in the 1880s, leading to their discovery of some of the mechanisms behind piezoelectricity....
published an experimental demonstration connecting mechanical stress and surface charge on a crystal. This phenomenon became known as the piezoelectric effect
Piezoelectricity
Piezoelectricity is the charge which accumulates in certain solid materials in response to applied mechanical stress. The word piezoelectricity means electricity resulting from pressure...
. Closely related to this phenomenon is the Curie point
Curie point
In physics and materials science, the Curie temperature , or Curie point, is the temperature at which a ferromagnetic or a ferrimagnetic material becomes paramagnetic on heating; the effect is reversible. A magnet will lose its magnetism if heated above the Curie temperature...
, named for the physicist Pierre Curie, which is the temperature above which piezoelectric material loses spontaneous polarization of its atoms.
The development of the commercial piezoelectric accelerometer came about through a number of attempts to find the most effective method to measure the vibration on large structures such as bridges and on vehicles in motion such as aircraft. One attempt involved using the resistance strain gage as a device to build an accelerometer. Incidentally, it was Hans J. Meier who, through his work at MIT, is given credit as the first to construct a commercial strain gage accelerometer (circa 1938). However, the strain gage accelerometers were fragile and could only produce low resonant frequencies and they also exhibited a low frequency response. These limitations in dynamic range
Dynamic range
Dynamic range, abbreviated DR or DNR, is the ratio between the largest and smallest possible values of a changeable quantity, such as in sound and light. It is measured as a ratio, or as a base-10 or base-2 logarithmic value.-Dynamic range and human perception:The human senses of sight and...
made it unsuitable for testing naval aircraft structures. On the other hand, the piezoelectric sensor
Piezoelectric sensor
A piezoelectric sensor is a device that uses the piezoelectric effect to measure pressure, acceleration, strain or force by converting them to an electrical charge.-Applications:...
was proven to be a much better choice over the strain gage in designing an accelerometer. The high modulus of elasticity of piezoelectric materials makes the piezoelectric sensor a more viable solution to the problems identified with the strain gage accelerometer.
Simply stated, the inherent properties of the piezoelectric accelerometers made it a much better alternative to the strain gage types because of its high frequency response, and its ability to generate high resonant frequencies. The piezoelectric accelerometer allowed for a reduction in its physical size at the manufacturing level and it also provided for a higher g
Standard gravity
Standard gravity, or standard acceleration due to free fall, usually denoted by g0 or gn, is the nominal acceleration of an object in a vacuum near the surface of the Earth. It is defined as precisely , or about...
(standard gravity) capability relative to the strain gage type. By comparison, the strain gage type exhibited a flat frequency response above 200 Hz while the piezoelectric type provided a flat response up to 10,000 Hz. These improvements made it possible for measuring the high frequency vibrations associated with the quick movements and short duration shocks of aircraft which before was not possible with the strain gage types. Before long, the technological benefits of the piezoelectric accelerometer became apparent and in the late 1940’s, large scale production of piezoelectric accelerometers began. Today, piezoelectric accelerometers are used for instrumentation in the fields of engineering, health and medicine, aeronautics and many other different industries.
Manufacturing
There are two common methods used to manufacture accelerometers. One is based upon the principles of piezoresistance and the other is based on the principles of piezoelectricity. Both methods ensure that unwanted orthogonal acceleration vectors are excluded from detection.Manufacturing an accelerometer that uses piezoresistance first starts with a semiconductor layer that is attached to a handle wafer by a thick oxide layer. The semiconductor layer is then patterned to the accelerometer’s geometry. This semiconductor layer has one or more apertures so that the underlying mass will have the corresponding apertures. Next the semiconductor layer is used as a mask to etch out a cavity in the underlying thick oxide. A mass in the cavity is supported in cantilever fashion by the piezoresistant arms of the semiconductor layer. Directly below the accelerometer’s geometry is a flex cavity that allows the mass in the cavity to flex or move in direction that is orthogonal to the surface of the accelerometer.
Accelerometers based upon piezoelectricity are constructed with two piezoelectric transducers. The unit consists of a hollow tube that is sealed by a piezoelectric transducer on each end. The transducers are oppositely polarized and are selected to have a specific series capacitance. The tube is then partially filled with a heavy liquid and the accelerometer is excited. While excited the total output voltage is continuously measured and the volume of the heavy liquid is microadjusted until the desired output voltage is obtained. Finally the outputs of the individual transducers are measured, the residual voltage difference is tabulated, and the dominate transducer is identified.