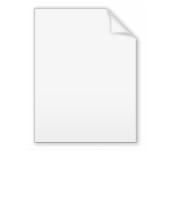
Spin coating
Encyclopedia
Spin coating is a procedure used to apply uniform thin film
s to flat substrate
s. In short, an excess amount of a solution
is placed on the substrate, which is then rotated at high speed in order to spread the fluid by centrifugal force
. A machine used for spin coating is called a spin coater, or simply spinner.
Rotation is continued while the fluid spins off the edges of the substrate, until the desired thickness of the film is achieved. The applied solvent is usually volatile
, and simultaneously evaporates
. So, the higher the angular speed of spinning, the thinner the film. The thickness of the film also depends on the concentration
of the solution and the solvent.
Spin coating is widely used in microfabrication
, where it can be used to create thin films with thicknesses below 10 nm. It is used intensively in photolithography
, to deposit layers of photoresist
about 1 micrometre
thick. Photoresist is typically spun at 20 to 80 revolutions per second for 30 to 60 seconds. Owing to the low values of thickness which can be achieved using spin coating methods, this method is often employed in the fabrication of transparent Titanium dioxide
thin films on quartz or glass substrates , such thin film coatings may exhibit self cleaning and self sterilizing properties.
This can be done by using a nozzle and pouring the coating solution or by spraying it onto the surface. A substantial excess of coating solution is usually applied compared to the amount that is required.
was once a traditional solvent commonly used in spin-coating, but due to toxicity issues cyclohexanone
is generally preferred and produces coatings of comparable quality. More polar solvents such as N,N-dimethylformamide (DMF) are also commonly used. Typically between 10 and 30% (w/w) polymer is dissolved in the solvent. Both the choice of solvent and especially the molecular weight of the polymer significantly affect the viscosity of the solution and thus the thickness of the resultant coating.
The bulk of semiconductors fabricated today have resist critical dimensions above 250 nm; this is also true of MEMS technology, GaAs, InP, LiNbO3, and other substrate-type technologies. For feature sizes of this magnitude and larger, positive i-line resist is the optimal lithographic film; i-line resists mainly consist of three components: resin, solvent, and PAC (photo-active compound). The most widely used resin is Novolak, which is a synthesized formaldehyde-phenolic, originally used as a furniture lacquer due to its physical resistant properties. The solvent is usually PGMEA (a healthier alternative to the once used EGMEA) – polyethylene glycol monomethyl ether acetate, or ethyl lactate
. The PAC, for i-line sensitivity (365 nm) is always diazonapthoquinone (DNQ). It liberates N2 (diazo) upon UV exposure of 365 nm wavelength – the UV source is a mercury lamp – and transforms the highly organic resist film into an alkaline aqueous soluble carboxylic acid. PMMA and triple-i resist formulations are now uncommon. They were once prevalent in the 1970s and can still be found in research laboratories and academia, but are rarely used in high volume manufacturing because of low cost efficiency and waste considerations.
For linewidths below 200 nm, a shorter wavelength of light is necessary to resolve the critical dimension. The resist needs to be chemically amplified to achieve such resolution. These are not DNQ resists since the 365 nm wavelength of light is too wide to adequately resolve features below 250 nanometres.
For many applications the solution is doped with an active dye or compound. In nonlinear optics
, typical doping compounds include Disperse Red and DANS with concentrations up to 30% w/w (dye/polymer). The active doping compound is typically referred to as the "guest," while the inert polymer is known as the "host."
Many substrates may be coated, but in many research applications one-inch square glass plates (for many applications often coated with a transparent electrode made of indium tin oxide or ITO) cut from microscope slides are commonly coated for experimental purposes. Prior to spin-coating, the polymer-solvent solution must be filtered to remove dust, typically with a 0.45 micrometre filter. Although it is preferable to spin-coat in a clean-room environment (Class 10 or 100), for many simple laboratory experiments, spin-coating may be performed in a clean fume-hood. The glass plate is placed upon the spin-coating apparatus, cleaned successively with acetone
and then methanol
using lint-free swabs, and followed up with isopropanol, then coated liberally with the polymer-solvent solution by use of syringe or eye-dropper. The plate is spun in at least two stages which may be programmed into most any simple spin-coating apparatus. During the first stage, the plate is spun at a low to moderate speed 500–1000 rpm for 5–10 seconds to evenly spread the solution. The thickness of the coating is then determined and controlled during the second stage by spinning the coating at a higher speed, between 1500–3000 rpm for anywhere between a few seconds and a minute. These conditions will typically produce high quality coatings of thickness between 2 and 10 micrometres.
Once spin-coating is complete, the plate is typically placed quickly onto a hot plate
(heated to somewhere around 100 °C) for several seconds or minutes to initially evaporate solvent and solidify the coating. The slide is then baked-out for several hours, or typically over night, in an oven or vacuum oven, at a temperature high enough to sufficiently remove the remaining solvent. Although it is not uncommon to place plates in a petri dish
during one or both bake-out steps to protect films from dust, condensation of solvent on the roof of the dish may greatly affect the film smoothness and quality and thus the lid of the dish must be set ajar to allow for the evaporating solvent to escape.
Many other polymers, such as polystyrene
or more polar polymers such as polysulfones or polyetherimides, may also be spin-coated. More polar polymers are typically dissolved in N,N-dimethylformamide (DMF). Some polymers are more difficult to coat than others. Most often poor quality, hazy, or "orange peel" coatings are the result of moisture absorption due to environmental humidity. Although strict control over the laboratory environment is the best way to improve coating quality, when this is difficult or infeasible one quick-fix to significantly improve film quality is to gently spray a dry inert gas
(such as nitrogen
, or preferably argon
) over the sample during coating while heating the sample with an infrared heat lamp (available at most any hardware store). The heat-lamp significantly reduces the local humidity while simultaneously speeding the rate of solvent evaporation so that the sample does not have a chance to absorb moisture.
Thin film
A thin film is a layer of material ranging from fractions of a nanometer to several micrometers in thickness. Electronic semiconductor devices and optical coatings are the main applications benefiting from thin film construction....
s to flat substrate
Substrate (printing)
Substrate is a term used in converting process such as printing and Lamination or coating as a more general term to describe the base material onto which e.g. images will be printed and to be laminated as per the packing specification required for the product...
s. In short, an excess amount of a solution
Solution
In chemistry, a solution is a homogeneous mixture composed of only one phase. In such a mixture, a solute is dissolved in another substance, known as a solvent. The solvent does the dissolving.- Types of solutions :...
is placed on the substrate, which is then rotated at high speed in order to spread the fluid by centrifugal force
Centrifugal force
Centrifugal force can generally be any force directed outward relative to some origin. More particularly, in classical mechanics, the centrifugal force is an outward force which arises when describing the motion of objects in a rotating reference frame...
. A machine used for spin coating is called a spin coater, or simply spinner.
Rotation is continued while the fluid spins off the edges of the substrate, until the desired thickness of the film is achieved. The applied solvent is usually volatile
Volatility (chemistry)
In chemistry and physics, volatility is the tendency of a substance to vaporize. Volatility is directly related to a substance's vapor pressure. At a given temperature, a substance with higher vapor pressure vaporizes more readily than a substance with a lower vapor pressure.The term is primarily...
, and simultaneously evaporates
Evaporation
Evaporation is a type of vaporization of a liquid that occurs only on the surface of a liquid. The other type of vaporization is boiling, which, instead, occurs on the entire mass of the liquid....
. So, the higher the angular speed of spinning, the thinner the film. The thickness of the film also depends on the concentration
Concentration
In chemistry, concentration is defined as the abundance of a constituent divided by the total volume of a mixture. Four types can be distinguished: mass concentration, molar concentration, number concentration, and volume concentration...
of the solution and the solvent.
Spin coating is widely used in microfabrication
Microfabrication
Microfabrication is the term that describes processes of fabrication of miniature structures, of micrometre sizes and smaller. Historically the earliest microfabrication processes were used for integrated circuit fabrication, also known as "semiconductor manufacturing" or "semiconductor device...
, where it can be used to create thin films with thicknesses below 10 nm. It is used intensively in photolithography
Photolithography
Photolithography is a process used in microfabrication to selectively remove parts of a thin film or the bulk of a substrate. It uses light to transfer a geometric pattern from a photomask to a light-sensitive chemical "photoresist", or simply "resist," on the substrate...
, to deposit layers of photoresist
Photoresist
A photoresist is a light-sensitive material used in several industrial processes, such as photolithography and photoengraving to form a patterned coating on a surface.-Tone:Photoresists are classified into two groups: positive resists and negative resists....
about 1 micrometre
Micrometre
A micrometer , is by definition 1×10-6 of a meter .In plain English, it means one-millionth of a meter . Its unit symbol in the International System of Units is μm...
thick. Photoresist is typically spun at 20 to 80 revolutions per second for 30 to 60 seconds. Owing to the low values of thickness which can be achieved using spin coating methods, this method is often employed in the fabrication of transparent Titanium dioxide
Titanium dioxide
Titanium dioxide, also known as titanium oxide or titania, is the naturally occurring oxide of titanium, chemical formula . When used as a pigment, it is called titanium white, Pigment White 6, or CI 77891. Generally it comes in two different forms, rutile and anatase. It has a wide range of...
thin films on quartz or glass substrates , such thin film coatings may exhibit self cleaning and self sterilizing properties.
Stages of spin coating
Although different engineers count things differently, there are four distinct stages to the spin coating process.- Deposition of the coating fluid onto the wafer or substrate
This can be done by using a nozzle and pouring the coating solution or by spraying it onto the surface. A substantial excess of coating solution is usually applied compared to the amount that is required.
- Acceleration of the substrate up to its final, desired, rotation speed
- Spinning of the substrate at a constant rate; fluid viscous forces dominate the fluid thinning behavior
- Spinning of the substrate at a constant rate; solvent evaporation dominates the coating thinning behavior
Tutorial & experimental technique
Although many polymers with a wide range of weights may be spin-coated, one of the easiest and most typical polymers to spin-coat is poly(methyl methacrylate) (PMMA) with a moderate molecular weight (e.g. ~120,000), dissolved in a solvent with some moderate polarity. The solvent 1,2,3-trichloropropane1,2,3-Trichloropropane
1,2,3-Trichloropropane is a chemical compound that is commonly used as an industrial solvent. Although it is not currently labeled as a contaminant by the United States federal government, new research shows that it could have severe health effects...
was once a traditional solvent commonly used in spin-coating, but due to toxicity issues cyclohexanone
Cyclohexanone
Cyclohexanone is the organic compound with the formula 5CO. The molecule consists of six-carbon cyclic molecule with a ketone functional group. This colorless oil has an odor reminiscent of peardrop sweets as well as acetone. Over time, samples assume a yellow color due to oxidation...
is generally preferred and produces coatings of comparable quality. More polar solvents such as N,N-dimethylformamide (DMF) are also commonly used. Typically between 10 and 30% (w/w) polymer is dissolved in the solvent. Both the choice of solvent and especially the molecular weight of the polymer significantly affect the viscosity of the solution and thus the thickness of the resultant coating.
The bulk of semiconductors fabricated today have resist critical dimensions above 250 nm; this is also true of MEMS technology, GaAs, InP, LiNbO3, and other substrate-type technologies. For feature sizes of this magnitude and larger, positive i-line resist is the optimal lithographic film; i-line resists mainly consist of three components: resin, solvent, and PAC (photo-active compound). The most widely used resin is Novolak, which is a synthesized formaldehyde-phenolic, originally used as a furniture lacquer due to its physical resistant properties. The solvent is usually PGMEA (a healthier alternative to the once used EGMEA) – polyethylene glycol monomethyl ether acetate, or ethyl lactate
Ethyl lactate
Ethyl lactate, also known as lactic acid ethyl ester, is a monobasic ester formed from lactic acid and ethanol, commonly used as a solvent. This compound is considered biodegradable and can be used as a water-rinsible degreaser. Ethyl lactate is found naturally in small quantities in a wide variety...
. The PAC, for i-line sensitivity (365 nm) is always diazonapthoquinone (DNQ). It liberates N2 (diazo) upon UV exposure of 365 nm wavelength – the UV source is a mercury lamp – and transforms the highly organic resist film into an alkaline aqueous soluble carboxylic acid. PMMA and triple-i resist formulations are now uncommon. They were once prevalent in the 1970s and can still be found in research laboratories and academia, but are rarely used in high volume manufacturing because of low cost efficiency and waste considerations.
For linewidths below 200 nm, a shorter wavelength of light is necessary to resolve the critical dimension. The resist needs to be chemically amplified to achieve such resolution. These are not DNQ resists since the 365 nm wavelength of light is too wide to adequately resolve features below 250 nanometres.
For many applications the solution is doped with an active dye or compound. In nonlinear optics
Nonlinear optics
Nonlinear optics is the branch of optics that describes the behavior of light in nonlinear media, that is, media in which the dielectric polarization P responds nonlinearly to the electric field E of the light...
, typical doping compounds include Disperse Red and DANS with concentrations up to 30% w/w (dye/polymer). The active doping compound is typically referred to as the "guest," while the inert polymer is known as the "host."
Many substrates may be coated, but in many research applications one-inch square glass plates (for many applications often coated with a transparent electrode made of indium tin oxide or ITO) cut from microscope slides are commonly coated for experimental purposes. Prior to spin-coating, the polymer-solvent solution must be filtered to remove dust, typically with a 0.45 micrometre filter. Although it is preferable to spin-coat in a clean-room environment (Class 10 or 100), for many simple laboratory experiments, spin-coating may be performed in a clean fume-hood. The glass plate is placed upon the spin-coating apparatus, cleaned successively with acetone
Acetone
Acetone is the organic compound with the formula 2CO, a colorless, mobile, flammable liquid, the simplest example of the ketones.Acetone is miscible with water and serves as an important solvent in its own right, typically as the solvent of choice for cleaning purposes in the laboratory...
and then methanol
Methanol
Methanol, also known as methyl alcohol, wood alcohol, wood naphtha or wood spirits, is a chemical with the formula CH3OH . It is the simplest alcohol, and is a light, volatile, colorless, flammable liquid with a distinctive odor very similar to, but slightly sweeter than, ethanol...
using lint-free swabs, and followed up with isopropanol, then coated liberally with the polymer-solvent solution by use of syringe or eye-dropper. The plate is spun in at least two stages which may be programmed into most any simple spin-coating apparatus. During the first stage, the plate is spun at a low to moderate speed 500–1000 rpm for 5–10 seconds to evenly spread the solution. The thickness of the coating is then determined and controlled during the second stage by spinning the coating at a higher speed, between 1500–3000 rpm for anywhere between a few seconds and a minute. These conditions will typically produce high quality coatings of thickness between 2 and 10 micrometres.
Once spin-coating is complete, the plate is typically placed quickly onto a hot plate
Hot plate
A hot plate is a portable self-contained tabletop small appliance that features one, two or more gas burners or electric heating elements. A hot plate can be used as a stand alone appliance, but is often used as a substitute for one of the burners from an oven range or the cook top of a stove...
(heated to somewhere around 100 °C) for several seconds or minutes to initially evaporate solvent and solidify the coating. The slide is then baked-out for several hours, or typically over night, in an oven or vacuum oven, at a temperature high enough to sufficiently remove the remaining solvent. Although it is not uncommon to place plates in a petri dish
Petri dish
A Petri dish is a shallow glass or plastic cylindrical lidded dish that biologists use to culture cells or small moss plants. It was named after German bacteriologist Julius Richard Petri, who invented it when working as an assistant to Robert Koch...
during one or both bake-out steps to protect films from dust, condensation of solvent on the roof of the dish may greatly affect the film smoothness and quality and thus the lid of the dish must be set ajar to allow for the evaporating solvent to escape.
Many other polymers, such as polystyrene
Polystyrene
Polystyrene ) also known as Thermocole, abbreviated following ISO Standard PS, is an aromatic polymer made from the monomer styrene, a liquid hydrocarbon that is manufactured from petroleum by the chemical industry...
or more polar polymers such as polysulfones or polyetherimides, may also be spin-coated. More polar polymers are typically dissolved in N,N-dimethylformamide (DMF). Some polymers are more difficult to coat than others. Most often poor quality, hazy, or "orange peel" coatings are the result of moisture absorption due to environmental humidity. Although strict control over the laboratory environment is the best way to improve coating quality, when this is difficult or infeasible one quick-fix to significantly improve film quality is to gently spray a dry inert gas
Inert gas
An inert gas is a non-reactive gas used during chemical synthesis, chemical analysis, or preservation of reactive materials. Inert gases are selected for specific settings for which they are functionally inert since the cost of the gas and the cost of purifying the gas are usually a consideration...
(such as nitrogen
Nitrogen
Nitrogen is a chemical element that has the symbol N, atomic number of 7 and atomic mass 14.00674 u. Elemental nitrogen is a colorless, odorless, tasteless, and mostly inert diatomic gas at standard conditions, constituting 78.08% by volume of Earth's atmosphere...
, or preferably argon
Argon
Argon is a chemical element represented by the symbol Ar. Argon has atomic number 18 and is the third element in group 18 of the periodic table . Argon is the third most common gas in the Earth's atmosphere, at 0.93%, making it more common than carbon dioxide...
) over the sample during coating while heating the sample with an infrared heat lamp (available at most any hardware store). The heat-lamp significantly reduces the local humidity while simultaneously speeding the rate of solvent evaporation so that the sample does not have a chance to absorb moisture.