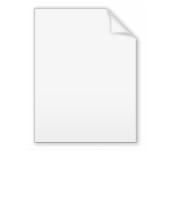
Tipped tool
Encyclopedia
A tipped tool generally refers to any cutting tool where the cutting edge consists of a separate piece of material, either brazed
, welded
or clamped on to a separate body. Common materials for tips include tungsten carbide
, polycrystalline diamond, and cubic boron nitride. Tools that are commonly tipped include: milling cutter
s (endmill
s, fly cutters), tool bit
s, and saw
blades.
material. In some situations a tipped tool is better than its solid counterpart because it combines the toughness of the tool holder with the hardness of the insert.
In other situations this is less than optimal, because the joint between the tool holder and the insert reduces rigidity. However, these tools may still be used because the overall cost savings is still greater.
, meaning that they can be rotated or flipped without disturbing the overall geometry of the tool (effective diameter, tool length offset, etc.). This saves time in manufacturing by allowing fresh cutting edges to be presented periodically without the need for tool grinding, setup changes, or entering of new values into a CNC program.
or a lathe
. It is designed for finish cutting, to give a smooth surface on the surface being cut. It uses special geometry to give a good finish on the workpiece at a higher-than-normal feedrate. Wiper inserts generally have a lot of area in contact with the workpiece, so they exert a lot of force on the workpiece. This makes them unsuitable for fragile workpieces.
Brazing
Brazing is a metal-joining process whereby a filler metal is heated above and distributed between two or more close-fitting parts by capillary action. The filler metal is brought slightly above its melting temperature while protected by a suitable atmosphere, usually a flux...
, welded
Welding
Welding is a fabrication or sculptural process that joins materials, usually metals or thermoplastics, by causing coalescence. This is often done by melting the workpieces and adding a filler material to form a pool of molten material that cools to become a strong joint, with pressure sometimes...
or clamped on to a separate body. Common materials for tips include tungsten carbide
Tungsten carbide
Tungsten carbide is an inorganic chemical compound containing equal parts of tungsten and carbon atoms. Colloquially, tungsten carbide is often simply called carbide. In its most basic form, it is a fine gray powder, but it can be pressed and formed into shapes for use in industrial machinery,...
, polycrystalline diamond, and cubic boron nitride. Tools that are commonly tipped include: milling cutter
Milling cutter
Milling cutters are cutting tools typically used in milling machines or machining centres . They remove material by their movement within the machine or directly from the cutter's shape .-Features of a milling cutter:Milling cutters come in several shapes and many sizes...
s (endmill
Endmill
An endmill is a type of milling cutter, a cutting tool used in industrial milling applications. It is distinguished from the drill bit, in its application, geometry, and manufacture...
s, fly cutters), tool bit
Tool bit
The term tool bit generally refers to a non-rotary cutting tool used in metal lathes, shapers, and planers. Such cutters are also often referred to by the set-phrase name of single-point cutting tool. The cutting edge is ground to suit a particular machining operation and may be resharpened or...
s, and saw
Saw
A saw is a tool that uses a hard blade or wire with an abrasive edge to cut through softer materials. The cutting edge of a saw is either a serrated blade or an abrasive...
blades.
Advantages and disadvantages
The advantage of tipped tools is only a small insert of the cutting material is needed to provide the cutting ability. The small size makes manufacturing of the insert easier than making a solid tool of the same material. This also reduces cost because the tool holder can be made of a less-expensive and tougherToughness
In materials science and metallurgy, toughness is the ability of a material to absorb energy and plastically deform without fracturing; Material toughness is defined as the amount of energy per volume that a material can absorb before rupturing...
material. In some situations a tipped tool is better than its solid counterpart because it combines the toughness of the tool holder with the hardness of the insert.
In other situations this is less than optimal, because the joint between the tool holder and the insert reduces rigidity. However, these tools may still be used because the overall cost savings is still greater.
Indexable inserts
Inserts are removable cutting tips, which means they are not brazed or welded to the tool body. They are usually indexableIndexing (motion)
Indexing in reference to motion is moving into a new position or location quickly and easily but also precisely. After a machine part has been indexed, its location is known to within a few hundredths of a millimeter , or often even to within a few thousandths of a millimeter , despite the fact...
, meaning that they can be rotated or flipped without disturbing the overall geometry of the tool (effective diameter, tool length offset, etc.). This saves time in manufacturing by allowing fresh cutting edges to be presented periodically without the need for tool grinding, setup changes, or entering of new values into a CNC program.
Wiper insert
A wiper insert is an insert used in a milling machineMilling machine
A milling machine is a machine tool used to machine solid materials. Milling machines are often classed in two basic forms, horizontal and vertical, which refers to the orientation of the main spindle. Both types range in size from small, bench-mounted devices to room-sized machines...
or a lathe
Lathe
A lathe is a machine tool which rotates the workpiece on its axis to perform various operations such as cutting, sanding, knurling, drilling, or deformation with tools that are applied to the workpiece to create an object which has symmetry about an axis of rotation.Lathes are used in woodturning,...
. It is designed for finish cutting, to give a smooth surface on the surface being cut. It uses special geometry to give a good finish on the workpiece at a higher-than-normal feedrate. Wiper inserts generally have a lot of area in contact with the workpiece, so they exert a lot of force on the workpiece. This makes them unsuitable for fragile workpieces.