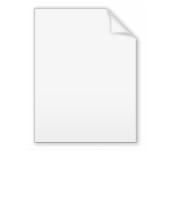
Shielding gas
Encyclopedia
Shielding gases are inert or semi-inert gas
es that are commonly used in several welding
processes, most notably gas metal arc welding
and gas tungsten arc welding
(GMAW and GTAW, more popularly known as MIG and TIG, respectively). Their purpose is to protect the weld area from atmospheric gases, such as oxygen
, nitrogen
, carbon dioxide
, and water vapour. Depending on the materials being welded, these atmospheric gases can reduce the quality of the weld or make the welding process more difficult to use. Other arc welding processes use other methods of protecting the weld from the atmosphere as well – shielded metal arc welding
, for example, uses an electrode
covered in a flux
that produces carbon dioxide when consumed, a semi-inert gas that is an acceptable shielding gas for welding steel.
Improper choice of a welding gas can lead to a porous and weak weld, or to excessive spatter; the latter, while not affecting the weld itself, causes loss of productivity due to the manpower needed to remove the scattered drops.
and argon
, are cost effective enough to be used in welding. These inert gases are used in gas tungsten arc welding, and also in gas metal arc welding for the welding of non-ferrous metal
s. Pure argon and helium are used only for some nonferrous metals. Semi-inert shielding gases, or active shield gases, include carbon dioxide, oxygen, nitrogen, and hydrogen
. Most of these gases, in large quantities, would damage the weld, but when used in small, controlled quantities, can improve weld characteristics.
Helium
is lighter than air; larger flow rates are required. It is an inert gas, not reacting with the molten metals. Its thermal conductivity
is high. It is not easy to ionize, requiring higher voltage to start the arc. Due to higher ionization potential it produces hotter arc at higher voltage, provides wide deep bead; this is an advantage for aluminium, magnesium, and copper alloys. Other gases are often added. Blends of helium with addition of 5–10% of argon and 2–5% of carbon dioxide ("tri-mix") can be used for welding of stainless steel. Used also for aluminium and other non-ferrous metals, especially for thicker welds. In comparison with argon, helium provides more energy-rich but less stable arc. Helium and carbon dioxide were the first shielding gases used, since the beginning of World War 2. Helium is used as a shield gas in laser welding for carbon dioxide laser
s. Helium is more expensive than argon and requires higher flow rates, so despite its advantages it may not be a cost-effective choice for higher-volume production. Pure helium is not used for steel, as it then provides erratic arc and encourages spatter.
Argon
is heavier than air; lower flow rates are needed to blanket the weld. It is an inert gas, not reacting with the molten metals. It has low thermal conductivity. It ionizes easily, providing a stable arc with an excellent current path and high current density. It produces a very narrow arc cone and narrow penetration profile. It is often used as pure when welding aluminium
and other nonferrous metals, though other gases can be added; pure argon does not provide sufficient penetration for welding steel. A blend of argon with 25–50% of helium is used for some nonferrous metals, as helium improves heat transfer into the base material and makes the molten metal more fluid. An oxidizing component (oxygen, carbon dioxide) is usually added to stabilize the arc for welding of steels; without it the arc control can be difficult as the arc tends to stray. In industrial gas business it is known as "the big A". Argon is used as a shield gas in laser welding for Nd:YAG laser
s.
Carbon dioxide
has good heat transfer properties; it dissociates
in the weld and recombines in contact with the colder metal. Produces very deep weld but somewhat unstable arc and, due to its reactivity, intense spatter. Due to the presence of dissociated oxygen, the weld zone has oxidizing properties, producing more slag
. Carbon dioxide can be used as pure (only for short-circuiting), or in a mixture with 5 to 25% argon, sometimes up to 50% (also for spray transfer); the argon addition inhibits sputtering. Increasing percentage of carbon dioxide increases the width and depth of the weld penetration. For welding of stainless steels where carbon content control is required, an argon-helium blend with 1–2% of carbon dioxide can be used. "Trimix" blends of argon – oxygen – carbon dioxide are more common in United Kingdom, while argon-carbon dioxide blends are more common in the USA. In comparison with argon-carbon dioxide mixture, for steel welding, pure carbon dioxide increases spatter and the arc is less stable. Pure carbon dioxide provides deep weld penetration and is very cheap. Pure carbon dioxide usage is limited to short circuit and globular transfer welding. It has high spatter and deep penetration. Provides good mechanical properties. Can be used for carbon steel. Has high production of smoke and fumes. It is very cheap.
Oxygen
is used in small amounts as an addition to other gases; typically as 2–5% addition to argon. It enhances arc stability and reduces the surface tension
of the molten metal, increasing wetting
of the solid metal. It is used for spray transfer welding of mild carbon steels, low alloy and stainless steel
s. Its presence increases the amount of slag. Argon-oxygen (Ar-O2) blends are often being replaced with argon-carbon dioxide ones. Argon-carbon dioxide-oxygen blends are also used. Oxygen causes oxidation of the weld, so it is not suitable for welding aluminium, magnesium, copper, and some exotic metals. Increased oxygen makes the shielding gas oxidize the electrode, which can lead to porosity in the deposit if the electrode does not contain sufficient deoxidizer
s. Excessive oxygen, especially when used in application for which it is not prescribed, can lead to brittleness in the heat affected zone. Argon-oxygen blends with 1–2% oxygen are used for austenitic stainless steel where argon-CO2 can not be used due to required low content of carbon in the weld; the weld has a tough oxide coating and may require cleaning.
Nitrogen
is used for welding of some stainless steels. It increases the weld penetration and enhances arc stability. It however can cause porosity in carbon steels. Argon-carbon dioxide-nitrogen blends can be used. Pure nitrogen is also used, or can be blended with 10% of hydrogen, depending on application. Blends with nitrogen content are used to weld nitrogen-containing alloys (up to 0.5% nitrogen increases mechanical properties and resistance to pitting corrosion
) to prevent loss of nitrogen from the metal. Nitrogen can be used in some cases of laser welding; it is almost as good as helium for plasma formation suppression but can cause embrittlement of some steels.
Hydrogen
is used for welding of nickel and some stainless steels, especially thicker pieces. It improves the molten metal fluidity, and enhances cleanness of the surface. It can however cause hydrogen embrittlement
of many alloys and especially carbon steel, so its application is usually limited only to some stainless steels. It is added to argon in amounts typically under 10%. It can be added to argon-carbon dioxide blends to counteract the oxidizing effects of carbon dioxide. Its addition narrows the arc and increases the arc temperature, leading to better weld penetration. In higher concentrations (up to 25% hydrogen), it may be used for welding conductive materials such as copper. However, it should not be used on steel, aluminum or magnesium because it can cause porosity and hydrogen embrittlement.
Nitric oxide
addition serves to reduce production of ozone
. It can also stabilize the arc when welding aluminium and high-alloyed stainless steel.
Other gases can be used for special applications, pure or as blend additives; e.g. sulfur hexafluoride
or dichlorodifluoromethane
.
Sulfur hexafluoride
can be added to shield gas for aluminium welding to bind hydrogen in the weld area to reduce weld porosity.
Dichlorodifluoromethane
with argon can be used for protective atmosphere for melting of aluminium-lithium alloys. It reduces the content of hydrogen in the aluminium weld, preventing the associated porosity.
The desirable rate of gas flow depends primarily on weld geometry, speed, current, the type of gas, and the metal transfer mode being utilized. Welding flat surfaces requires higher flow than welding grooved materials, since the gas is dispersed more quickly. Faster welding speeds, in general, mean that more gas needs to be supplied to provide adequate coverage. Additionally, higher current requires greater flow, and generally, more helium is required to provide adequate coverage than argon. Perhaps most importantly, the four primary variations of GMAW have differing shielding gas flow requirements—for the small weld pools of the short circuiting and pulsed spray modes, about 10 L
/min (20 ft3/h
) is generally suitable, while for globular transfer, around 15 L/min (30 ft3/h) is preferred. The spray transfer variation normally requires more because of its higher heat input and thus larger weld pool; along the lines of 20–25 L/min (40–50 ft3/h).
Inert gas
An inert gas is a non-reactive gas used during chemical synthesis, chemical analysis, or preservation of reactive materials. Inert gases are selected for specific settings for which they are functionally inert since the cost of the gas and the cost of purifying the gas are usually a consideration...
es that are commonly used in several welding
Welding
Welding is a fabrication or sculptural process that joins materials, usually metals or thermoplastics, by causing coalescence. This is often done by melting the workpieces and adding a filler material to form a pool of molten material that cools to become a strong joint, with pressure sometimes...
processes, most notably gas metal arc welding
Gas metal arc welding
Gas metal arc welding , sometimes referred to by its subtypes metal inert gas welding or metal active gas welding, is a semi-automatic or automatic arc welding process in which a continuous and consumable wire electrode and a shielding gas are fed through a welding gun...
and gas tungsten arc welding
Gas tungsten arc welding
Gas tungsten arc welding , also known as tungsten inert gas welding, is an arc welding process that uses a nonconsumable tungsten electrode to produce the weld...
(GMAW and GTAW, more popularly known as MIG and TIG, respectively). Their purpose is to protect the weld area from atmospheric gases, such as oxygen
Oxygen
Oxygen is the element with atomic number 8 and represented by the symbol O. Its name derives from the Greek roots ὀξύς and -γενής , because at the time of naming, it was mistakenly thought that all acids required oxygen in their composition...
, nitrogen
Nitrogen
Nitrogen is a chemical element that has the symbol N, atomic number of 7 and atomic mass 14.00674 u. Elemental nitrogen is a colorless, odorless, tasteless, and mostly inert diatomic gas at standard conditions, constituting 78.08% by volume of Earth's atmosphere...
, carbon dioxide
Carbon dioxide
Carbon dioxide is a naturally occurring chemical compound composed of two oxygen atoms covalently bonded to a single carbon atom...
, and water vapour. Depending on the materials being welded, these atmospheric gases can reduce the quality of the weld or make the welding process more difficult to use. Other arc welding processes use other methods of protecting the weld from the atmosphere as well – shielded metal arc welding
Shielded metal arc welding
Shielded metal arc welding , also known as manual metal arc welding, flux shielded arc welding or informally as stick welding, is a manual arc welding process that uses a consumable electrode coated in flux to lay the weld...
, for example, uses an electrode
Electrode
An electrode is an electrical conductor used to make contact with a nonmetallic part of a circuit...
covered in a flux
Flux (metallurgy)
In metallurgy, a flux , is a chemical cleaning agent, flowing agent, or purifying agent. Fluxes may have more than one function at a time...
that produces carbon dioxide when consumed, a semi-inert gas that is an acceptable shielding gas for welding steel.
Improper choice of a welding gas can lead to a porous and weak weld, or to excessive spatter; the latter, while not affecting the weld itself, causes loss of productivity due to the manpower needed to remove the scattered drops.
Common shielding gases
Shielding gases fall into two categories—inert or semi-inert. Only two of the noble gases, heliumHelium
Helium is the chemical element with atomic number 2 and an atomic weight of 4.002602, which is represented by the symbol He. It is a colorless, odorless, tasteless, non-toxic, inert, monatomic gas that heads the noble gas group in the periodic table...
and argon
Argon
Argon is a chemical element represented by the symbol Ar. Argon has atomic number 18 and is the third element in group 18 of the periodic table . Argon is the third most common gas in the Earth's atmosphere, at 0.93%, making it more common than carbon dioxide...
, are cost effective enough to be used in welding. These inert gases are used in gas tungsten arc welding, and also in gas metal arc welding for the welding of non-ferrous metal
Non-ferrous metal
In metallurgy, a non-ferrous metal is a metal that is not ferrous, that is, any metal, including alloys, that does not contain iron in appreciable amounts...
s. Pure argon and helium are used only for some nonferrous metals. Semi-inert shielding gases, or active shield gases, include carbon dioxide, oxygen, nitrogen, and hydrogen
Hydrogen
Hydrogen is the chemical element with atomic number 1. It is represented by the symbol H. With an average atomic weight of , hydrogen is the lightest and most abundant chemical element, constituting roughly 75% of the Universe's chemical elemental mass. Stars in the main sequence are mainly...
. Most of these gases, in large quantities, would damage the weld, but when used in small, controlled quantities, can improve weld characteristics.
Properties
The important properties of shielding gases are their thermal conductivity and heat transfer properties, their density relative to air, and how easy they undergo ionization. Gases heavier than air (e.g. argon) blanket the weld and require lower flow rates than gases lighter than air (e.g. helium). Heat transfer is important for heating the weld around the arc. Ionizability influences how easy the arc starts, and how high voltage is required. Shielding gases can be used pure, or as a blend of two or three gases. In laser welding, the shielding gas has an additional role, preventing formation of a cloud of plasma above the weld, absorbing significant fraction of the laser energy. This is important for CO2 lasers; Nd:YAG lasers show lower tendency to form such plasma. Helium plays this role best due to its high ionization potential; the gas can absorb high amount of energy before becoming ionized.Helium
Helium
Helium is the chemical element with atomic number 2 and an atomic weight of 4.002602, which is represented by the symbol He. It is a colorless, odorless, tasteless, non-toxic, inert, monatomic gas that heads the noble gas group in the periodic table...
is lighter than air; larger flow rates are required. It is an inert gas, not reacting with the molten metals. Its thermal conductivity
Thermal conductivity
In physics, thermal conductivity, k, is the property of a material's ability to conduct heat. It appears primarily in Fourier's Law for heat conduction....
is high. It is not easy to ionize, requiring higher voltage to start the arc. Due to higher ionization potential it produces hotter arc at higher voltage, provides wide deep bead; this is an advantage for aluminium, magnesium, and copper alloys. Other gases are often added. Blends of helium with addition of 5–10% of argon and 2–5% of carbon dioxide ("tri-mix") can be used for welding of stainless steel. Used also for aluminium and other non-ferrous metals, especially for thicker welds. In comparison with argon, helium provides more energy-rich but less stable arc. Helium and carbon dioxide were the first shielding gases used, since the beginning of World War 2. Helium is used as a shield gas in laser welding for carbon dioxide laser
Carbon dioxide laser
The carbon dioxide laser was one of the earliest gas lasers to be developed , and is still one of the most useful. Carbon dioxide lasers are the highest-power continuous wave lasers that are currently available...
s. Helium is more expensive than argon and requires higher flow rates, so despite its advantages it may not be a cost-effective choice for higher-volume production. Pure helium is not used for steel, as it then provides erratic arc and encourages spatter.
Argon
Argon
Argon is a chemical element represented by the symbol Ar. Argon has atomic number 18 and is the third element in group 18 of the periodic table . Argon is the third most common gas in the Earth's atmosphere, at 0.93%, making it more common than carbon dioxide...
is heavier than air; lower flow rates are needed to blanket the weld. It is an inert gas, not reacting with the molten metals. It has low thermal conductivity. It ionizes easily, providing a stable arc with an excellent current path and high current density. It produces a very narrow arc cone and narrow penetration profile. It is often used as pure when welding aluminium
Aluminium
Aluminium or aluminum is a silvery white member of the boron group of chemical elements. It has the symbol Al, and its atomic number is 13. It is not soluble in water under normal circumstances....
and other nonferrous metals, though other gases can be added; pure argon does not provide sufficient penetration for welding steel. A blend of argon with 25–50% of helium is used for some nonferrous metals, as helium improves heat transfer into the base material and makes the molten metal more fluid. An oxidizing component (oxygen, carbon dioxide) is usually added to stabilize the arc for welding of steels; without it the arc control can be difficult as the arc tends to stray. In industrial gas business it is known as "the big A". Argon is used as a shield gas in laser welding for Nd:YAG laser
Nd:YAG laser
Nd:YAG is a crystal that is used as a lasing medium for solid-state lasers. The dopant, triply ionized neodymium, typically replaces yttrium in the crystal structure of the yttrium aluminium garnet , since they are of similar size...
s.
Carbon dioxide
Carbon dioxide
Carbon dioxide is a naturally occurring chemical compound composed of two oxygen atoms covalently bonded to a single carbon atom...
has good heat transfer properties; it dissociates
Dissociation (chemistry)
Dissociation in chemistry and biochemistry is a general process in which ionic compounds separate or split into smaller particles, ions, or radicals, usually in a reversible manner...
in the weld and recombines in contact with the colder metal. Produces very deep weld but somewhat unstable arc and, due to its reactivity, intense spatter. Due to the presence of dissociated oxygen, the weld zone has oxidizing properties, producing more slag
Slag
Slag is a partially vitreous by-product of smelting ore to separate the metal fraction from the unwanted fraction. It can usually be considered to be a mixture of metal oxides and silicon dioxide. However, slags can contain metal sulfides and metal atoms in the elemental form...
. Carbon dioxide can be used as pure (only for short-circuiting), or in a mixture with 5 to 25% argon, sometimes up to 50% (also for spray transfer); the argon addition inhibits sputtering. Increasing percentage of carbon dioxide increases the width and depth of the weld penetration. For welding of stainless steels where carbon content control is required, an argon-helium blend with 1–2% of carbon dioxide can be used. "Trimix" blends of argon – oxygen – carbon dioxide are more common in United Kingdom, while argon-carbon dioxide blends are more common in the USA. In comparison with argon-carbon dioxide mixture, for steel welding, pure carbon dioxide increases spatter and the arc is less stable. Pure carbon dioxide provides deep weld penetration and is very cheap. Pure carbon dioxide usage is limited to short circuit and globular transfer welding. It has high spatter and deep penetration. Provides good mechanical properties. Can be used for carbon steel. Has high production of smoke and fumes. It is very cheap.
Oxygen
Oxygen
Oxygen is the element with atomic number 8 and represented by the symbol O. Its name derives from the Greek roots ὀξύς and -γενής , because at the time of naming, it was mistakenly thought that all acids required oxygen in their composition...
is used in small amounts as an addition to other gases; typically as 2–5% addition to argon. It enhances arc stability and reduces the surface tension
Surface tension
Surface tension is a property of the surface of a liquid that allows it to resist an external force. It is revealed, for example, in floating of some objects on the surface of water, even though they are denser than water, and in the ability of some insects to run on the water surface...
of the molten metal, increasing wetting
Wetting
Wetting is the ability of a liquid to maintain contact with a solid surface, resulting from intermolecular interactions when the two are brought together. The degree of wetting is determined by a force balance between adhesive and cohesive forces.Wetting is important in the bonding or adherence of...
of the solid metal. It is used for spray transfer welding of mild carbon steels, low alloy and stainless steel
Stainless steel
In metallurgy, stainless steel, also known as inox steel or inox from French "inoxydable", is defined as a steel alloy with a minimum of 10.5 or 11% chromium content by mass....
s. Its presence increases the amount of slag. Argon-oxygen (Ar-O2) blends are often being replaced with argon-carbon dioxide ones. Argon-carbon dioxide-oxygen blends are also used. Oxygen causes oxidation of the weld, so it is not suitable for welding aluminium, magnesium, copper, and some exotic metals. Increased oxygen makes the shielding gas oxidize the electrode, which can lead to porosity in the deposit if the electrode does not contain sufficient deoxidizer
Deoxidizer
A deoxidizer is a chemical used in a reaction or process to remove oxygen. In comparison with antioxidants, deoxidizers are not used for stabilization during storage but for oxygen removal during manufacture...
s. Excessive oxygen, especially when used in application for which it is not prescribed, can lead to brittleness in the heat affected zone. Argon-oxygen blends with 1–2% oxygen are used for austenitic stainless steel where argon-CO2 can not be used due to required low content of carbon in the weld; the weld has a tough oxide coating and may require cleaning.
Nitrogen
Nitrogen
Nitrogen is a chemical element that has the symbol N, atomic number of 7 and atomic mass 14.00674 u. Elemental nitrogen is a colorless, odorless, tasteless, and mostly inert diatomic gas at standard conditions, constituting 78.08% by volume of Earth's atmosphere...
is used for welding of some stainless steels. It increases the weld penetration and enhances arc stability. It however can cause porosity in carbon steels. Argon-carbon dioxide-nitrogen blends can be used. Pure nitrogen is also used, or can be blended with 10% of hydrogen, depending on application. Blends with nitrogen content are used to weld nitrogen-containing alloys (up to 0.5% nitrogen increases mechanical properties and resistance to pitting corrosion
Pitting corrosion
Pitting corrosion, or pitting, is a form of extremely localized corrosion that leads to the creation of small holes in the metal. The driving power for pitting corrosion is the depassivation of a small area, which becomes anodic while an unknown but potentially vast area becomes cathodic, leading...
) to prevent loss of nitrogen from the metal. Nitrogen can be used in some cases of laser welding; it is almost as good as helium for plasma formation suppression but can cause embrittlement of some steels.
Hydrogen
Hydrogen
Hydrogen is the chemical element with atomic number 1. It is represented by the symbol H. With an average atomic weight of , hydrogen is the lightest and most abundant chemical element, constituting roughly 75% of the Universe's chemical elemental mass. Stars in the main sequence are mainly...
is used for welding of nickel and some stainless steels, especially thicker pieces. It improves the molten metal fluidity, and enhances cleanness of the surface. It can however cause hydrogen embrittlement
Hydrogen embrittlement
Hydrogen embrittlement is the process by which various metals, most importantly high-strength steel, become brittle and fracture following exposure to hydrogen...
of many alloys and especially carbon steel, so its application is usually limited only to some stainless steels. It is added to argon in amounts typically under 10%. It can be added to argon-carbon dioxide blends to counteract the oxidizing effects of carbon dioxide. Its addition narrows the arc and increases the arc temperature, leading to better weld penetration. In higher concentrations (up to 25% hydrogen), it may be used for welding conductive materials such as copper. However, it should not be used on steel, aluminum or magnesium because it can cause porosity and hydrogen embrittlement.
Nitric oxide
Nitric oxide
Nitric oxide, also known as nitrogen monoxide, is a diatomic molecule with chemical formula NO. It is a free radical and is an important intermediate in the chemical industry...
addition serves to reduce production of ozone
Ozone
Ozone , or trioxygen, is a triatomic molecule, consisting of three oxygen atoms. It is an allotrope of oxygen that is much less stable than the diatomic allotrope...
. It can also stabilize the arc when welding aluminium and high-alloyed stainless steel.
Other gases can be used for special applications, pure or as blend additives; e.g. sulfur hexafluoride
Sulfur hexafluoride
Sulfur hexafluoride is an inorganic, colorless, odorless, and non-flammable greenhouse gas. has an octahedral geometry, consisting of six fluorine atoms attached to a central sulfur atom. It is a hypervalent molecule. Typical for a nonpolar gas, it is poorly soluble in water but soluble in...
or dichlorodifluoromethane
Dichlorodifluoromethane
Dichlorodifluoromethane , is a colorless gas, and usually sold under the brand name Freon-12, is a chlorofluorocarbon halomethane , used as a refrigerant and aerosol spray propellant. Complying with the Montreal Protocol, its manufacture was banned in the United States along with many other...
.
Sulfur hexafluoride
Sulfur hexafluoride
Sulfur hexafluoride is an inorganic, colorless, odorless, and non-flammable greenhouse gas. has an octahedral geometry, consisting of six fluorine atoms attached to a central sulfur atom. It is a hypervalent molecule. Typical for a nonpolar gas, it is poorly soluble in water but soluble in...
can be added to shield gas for aluminium welding to bind hydrogen in the weld area to reduce weld porosity.
Dichlorodifluoromethane
Dichlorodifluoromethane
Dichlorodifluoromethane , is a colorless gas, and usually sold under the brand name Freon-12, is a chlorofluorocarbon halomethane , used as a refrigerant and aerosol spray propellant. Complying with the Montreal Protocol, its manufacture was banned in the United States along with many other...
with argon can be used for protective atmosphere for melting of aluminium-lithium alloys. It reduces the content of hydrogen in the aluminium weld, preventing the associated porosity.
Common mixes
- Argon-carbon dioxide
- C-50 (50% argon/50% CO2) is used for short arc welding of pipesPipe (material)A pipe is a tubular section or hollow cylinder, usually but not necessarily of circular cross-section, used mainly to convey substances which can flow — liquids and gases , slurries, powders, masses of small solids...
, - C-40 (60% argon/40% CO2) is used for some flux-cored arc weldingFlux-cored arc weldingFlux-cored arc welding is a semi-automatic or automatic arc welding process. FCAW requires a continuously-fed consumable tubular electrode containing a flux and a constant-voltage or, less commonly, a constant-current welding power supply...
cases. Better weld penetration than C-25. - C-25 (75% argon/25% CO2) is commonly used by hobbyists and in small-scale production. Limited to short circuit and globular transfer welding. Common for short-circuit gas metal arc welding of low carbon steel.
- C-20 (80% argon/20% CO2) is used for short-circuiting and spray transfer of carbon steel.
- C-15 (85% argon/15% CO2) is common in production environment for carbon and low alloy steels. Has lower spatter and good weld penetration, suitable for thicker plates and steel significantly covered with mill scaleMill scaleMill scale, often shortened to just scale, is the flaky surface of hot rolled steel, iron oxides consisting of Iron oxide, hematite, and magnetite....
. Suitable for short circuit, globular, pulse and spray transfer welding. Maximum productivity for thin metals in short-circuiting mode; has lower tendency to burn through than higher-CO2 mixes and has suitably high deposition rates. - C-10 (90% argon/10% CO2) is common in production environment. Has low spatter and good weld penetration, though lower than C-15 one; suitable for many steels. Same applications as 85/15 mix. Sufficient for ferritic stainless steels.
- C-5 (95% argon/5% CO2) is used for pulse spray transfer and short-circuiting of low alloy steel. Has better tolerance for mill scale and better puddle control than argon-oxygen, though less than C-10. Less heat than C-10. Sufficient for ferritic stainless steels. Similar performance to argon with 1% oxygen.
- O-5 (95% argon/5% oxygen) is the most common gas for general carbon steel welding. Higher oxygen content allows higher speed of welding. More than 5% oxygen makes the shielding gas oxidize the electrode, which can lead to porosity in the deposit if the electrode does not contain sufficient deoxidizers.
- O-2 (98% argon/2% oxygen) is used for spray arc on stainless steel, carbon steels, and low alloy steels. Better wetting than O-1. Weld is darker and more oxidized than with O-1. The addition of 2% oxygen encourages spray transfer, which is critical for spray-arc and pulsed spray-arc GMAW.
- O-1 (99% argon/1% oxygen) is used for stainless steels. Oxygen stabilizes the arc.
- C-50 (50% argon/50% CO2) is used for short arc welding of pipes
- Argon-helium
- A-25 (75% argon/25% helium) is used for nonferrous base when higher heat input and good weld appearance are needed.
- A-50 (50% argon/50% helium) is used for nonferrous metals thinner than 0.75 inch for high-speed mechanized welding.
- A-75 (25% argon/75% helium) is used for mechanized welding of thick aluminium. Reduces weld porosity in copper.
- Argon-hydrogen
- H-2 (98% argon/2% hydrogen)
- H-5 (95% argon/5% hydrogen)
- H-10 (80% argon/20% hydrogen)
- H-35 (65% argon/35% hydrogen)
- Others
- Argon with 25–35% helium and 1–2% CO2 provides high productivity and good welds on austenitic stainless steels. Can be used for joining stainless steel to carbon steel.
- Argon-CO2 with 1–2% hydrogen provides a reducing atmosphere that lowers amount of oxide on the weld surface, improves wetting and penetration. Good for austenitic stainless steels.
- Argon with 2–5% nitrogen and 2–5% CO2 in short-circuiting yields good weld shape and color and increases welding speed. For spray and pulsed spray transfer it is nearly equivalent to other trimixes. When joining stainless to carbon steels in presence of nitrogen, care has to be taken to ensure the proper weld microstructure. Nitrogen increases arc stability and penetration and reduces distortion of the welded part. In duplex stainless steels assists in maintaining proper nitrogen content.
- 85–95% helium with 5–10% argon and 2–5% CO2 is an industry standard for short-circuit welding of carbon steel.
- Argon – carbon dioxide – oxygen
- Argon–helium–hydrogen
- Argon – helium – hydrogen – carbon dioxide
Applications
The applications of shielding gases are limited primarily by the cost of the gas, the cost of the equipment, and by the location of the welding. Some shielding gases, like argon, are expensive, limiting its use. The equipment used for the delivery of the gas is also an added cost, and as a result, processes like shielded metal arc welding, which require less expensive equipment, might be preferred in certain situations. Finally, because atmospheric movements can cause the dispersion of the shielding gas around the weld, welding processes that require shielding gases are often only done indoors, where the environment is stable and atmospheric gases can be effectively prevented from entering the weld area.The desirable rate of gas flow depends primarily on weld geometry, speed, current, the type of gas, and the metal transfer mode being utilized. Welding flat surfaces requires higher flow than welding grooved materials, since the gas is dispersed more quickly. Faster welding speeds, in general, mean that more gas needs to be supplied to provide adequate coverage. Additionally, higher current requires greater flow, and generally, more helium is required to provide adequate coverage than argon. Perhaps most importantly, the four primary variations of GMAW have differing shielding gas flow requirements—for the small weld pools of the short circuiting and pulsed spray modes, about 10 L
Litre
pic|200px|right|thumb|One litre is equivalent to this cubeEach side is 10 cm1 litre water = 1 kilogram water The litre is a metric system unit of volume equal to 1 cubic decimetre , to 1,000 cubic centimetres , and to 1/1,000 cubic metre...
/min (20 ft3/h
Hour
The hour is a unit of measurement of time. In modern usage, an hour comprises 60 minutes, or 3,600 seconds...
) is generally suitable, while for globular transfer, around 15 L/min (30 ft3/h) is preferred. The spray transfer variation normally requires more because of its higher heat input and thus larger weld pool; along the lines of 20–25 L/min (40–50 ft3/h).