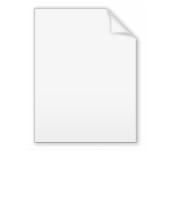
Surface finishing
Encyclopedia
Surface finishing is a broad range of industrial process
es that alter the surface of a manufactured item to achieve a certain property. Finishing processes may be employed to: improve appearance, adhesion or wettability, solderability
, corrosion resistance, tarnish resistance, chemical resistance, wear resistance, hardness, modify electrical conductivity, remove burrs and other surface flaws, and control the surface friction
. In limited cases some of these techniques can be used to restore original dimensions to salvage or repair an item.
Surface finishing processes can be categorized by how they affect the workpiece:
Mechanical processes may also be categorized together because of similarities the final surface finish.
The use of abrasives in metal polishing results in what is considered a "mechanical finish".
Also known as grinding, roughing or rough grinding. These finishes are coarse in nature and usually are a preliminary finish applied before manufacturing. An example would be grinding gates off of castings, deburring or removing excess weld material. It is coarse in appearance and applied by using 36–100 grit abrasive.
When the finish is specified as #3, the material is polished to a uniform 60–80 grit.
Also known as brushed, directional or satin finish. A #4 architectural finish is characterized by fine polishing grit lines that are uniform and directional in appearance. It is produced by polishing the metal with a 120–180 grit belt or wheel finish and then softened with an 80–120 grit greaseless compound or a medium non woven abrasive belt or pad.
This finish is commonly used for the medical and food industry and almost exclusively used on stainless steel. This finish is much finer than a #4 architectural finish. One takes great care to remove any surface defects in the metal, like pits, that could allow bacteria to grow. A #4 dairy or sanitary finish is produced by polishing with a 180–240 grit belt or wheel finish softened with 120–240 grit greaseless compound or a fine non woven abrasive belt or pad.
Also known as a fine satin finish. This finish is produced by polishing with a 220–280 grit belt or wheel softened with a 220–230 greaseless compound or very fine non woven abrasive belt or pad. Polishing lines will be soft and less reflective than a #4 architectural finish.
A #7 finish is produced by polishing with a 280–320 belt or wheel and sisal buffing with a cut and color compound. This is a semi-bright finish that will still have some polishing lines but they will be very dull. Carbon steel and iron are commonly polished to a #7 finish before chrome plating. A #7 finish can be made bright by color buffing with coloring compound and a cotton buff. This is commonly applied to keep polishing costs down when a part needs to be shiny but not flawless.
Also known as a mirror finish. This finish is produced by polishing with at least a 320 grit belt or wheel finish. Care will be taken in making sure all surface defects are removed. The part is sisal buffed and then color buffed to achieve a mirror finish. The quality of this finish is dependent on the quality of the metal being polished. Some alloys of steel and aluminum cannot be brought to a mirror finish. Castings that have slag or pits will also be difficult, if not impossible, to polish to a #8.
Industrial process
Industrial processes are procedures involving chemical or mechanical steps to aid in the manufacture of an item or items, usually carried out on a very large scale. Industrial processes are the key components of heavy industry....
es that alter the surface of a manufactured item to achieve a certain property. Finishing processes may be employed to: improve appearance, adhesion or wettability, solderability
Soldering
Soldering is a process in which two or more metal items are joined together by melting and flowing a filler metal into the joint, the filler metal having a lower melting point than the workpiece...
, corrosion resistance, tarnish resistance, chemical resistance, wear resistance, hardness, modify electrical conductivity, remove burrs and other surface flaws, and control the surface friction
Friction
Friction is the force resisting the relative motion of solid surfaces, fluid layers, and/or material elements sliding against each other. There are several types of friction:...
. In limited cases some of these techniques can be used to restore original dimensions to salvage or repair an item.
Surface finishing processes can be categorized by how they affect the workpiece:
- Removing or reshaping finishing
- Adding or altering finishing
Mechanical processes may also be categorized together because of similarities the final surface finish.
Adding and altering
- BlanchingBlanching (coinage)Blanching is the whitening of metal, by various means, such as soaking in acid or by coating with tin. This term is commonly used in coinage, in which pieces are given a lustre and brilliance before images are struck into the surface....
- Case hardeningCase hardeningCase hardening or surface hardening is the process of hardening the surface of a metal, often a low carbon steel, by infusing elements into the material's surface, forming a thin layer of a harder alloy...
- Ceramic glazeCeramic glazeGlaze is a layer or coating of a vitreous substance which has been fired to fuse to a ceramic object to color, decorate, strengthen or waterproof it.-Use:...
- CladdingCladding (metalworking)Cladding is the bonding together of dissimilar metals. It is distinct from welding or gluing as a method to fasten the metals together. Cladding is often achieved by extruding two metals through a die as well as pressing or rolling sheets together under high pressure.The United States Mint uses...
- Corona treatmentCorona treatmentCorona treatment is a surface modification technique that uses a low temperature corona discharge plasma to impart changes in the properties of a surface. The corona plasma is generated by the application of high voltage to sharp electrode tips which forms plasma at the ends of the sharp tips...
- Diffusion processes:
- Carburizing
- Nitriding
- ElectroplatingElectroplatingElectroplating is a plating process in which metal ions in a solution are moved by an electric field to coat an electrode. The process uses electrical current to reduce cations of a desired material from a solution and coat a conductive object with a thin layer of the material, such as a metal...
- Galvanizing
- GildingGildingThe term gilding covers a number of decorative techniques for applying fine gold leaf or powder to solid surfaces such as wood, stone, or metal to give a thin coating of gold. A gilded object is described as "gilt"...
- Glazing
- KnurlingKnurlingKnurling is a manufacturing process, typically conducted on a lathe, whereby a visually attractive diamond-shaped pattern is cut or rolled into metal.- Uses :...
- PaintPaintPaint is any liquid, liquefiable, or mastic composition which after application to a substrate in a thin layer is converted to an opaque solid film. One may also consider the digital mimicry thereof...
ing - PassivationPassivationPassivation is the process of making a material "passive", and thus less reactive with surrounding air, water, or other gases or liquids. The goal is to inhibit corrosion, whether for structural or cosmetic reasons. Passivation of metals is usually achieved by the deposition of a layer of oxide...
/Conversion coatingConversion coatingConversion coatings are coatings for metals where the part surface is converted into the coating with a chemical or electro-chemical process. Examples include chromate conversion coatings, phosphate conversion coatings, bluing, black oxide coatings on steel, and anodizing. They are used for...
- Anodizing
- BluingBluing (steel)Bluing is a passivation process in which steel is partially protected against rust, and is named after the blue-black appearance of the resulting protective finish. True gun bluing is an electrochemical conversion coating resulting from an oxidizing chemical reaction with iron on the surface...
- Chromate conversion coatingChromate conversion coatingChromate conversion coating is a type of conversion coating used to passivate aluminum, zinc, cadmium, copper, silver, magnesium, and tin alloys. It is primarily used as a corrosion inhibitor, primer, decorative finish, or to retain electrical conductivity. The process is named after the chromate...
- Phosphate conversion coatingPhosphate conversion coatingPhosphate coatings are used on steel parts for corrosion resistance, lubricity, or as a foundation for subsequent coatings or painting. It serves as a conversion coating in which a dilute solution of phosphoric acid and phosphate salts is applied via spraying or immersion and chemically reacts with...
- ParkerizingParkerizingParkerizing is a method of protecting a steel surface from corrosion and increasing its resistance to wear through the application of an electrochemical phosphate conversion coating...
- Parkerizing
- Plasma electrolytic oxidationPlasma electrolytic oxidationPlasma electrolytic oxidation , also known as microarc oxidation , is an electrochemical surface treatment process for generating oxide coatings on metals. It is similar to anodizing, but it employs higher potentials, so that discharges occur and the resulting plasma modifies the structure of the...
- Plasma spraying
- Powder coatingPowder coatingthumb|right|Aluminium extrusions being powder coatedPowder coating is a type of coating that is applied as a free-flowing, dry powder. The main difference between a conventional liquid paint and a powder coating is that the powder coating does not require a solvent to keep the binder and filler...
- Thin-film deposition
- Chemical vapor depositionChemical vapor depositionChemical vapor deposition is a chemical process used to produce high-purity, high-performance solid materials. The process is often used in the semiconductor industry to produce thin films. In a typical CVD process, the wafer is exposed to one or more volatile precursors, which react and/or...
(CVD) - ElectroplatingElectroplatingElectroplating is a plating process in which metal ions in a solution are moved by an electric field to coat an electrode. The process uses electrical current to reduce cations of a desired material from a solution and coat a conductive object with a thin layer of the material, such as a metal...
- Electrophoretic depositionElectrophoretic depositionElectrophoretic deposition , is a term for a broad range of industrial processes which includes electrocoating, e-coating, cathodic electrodeposition, and electrophoretic coating, or electrophoretic painting...
(EPD) - Mechanical plating
- Sputter depositionSputter depositionSputter deposition is a physical vapor deposition method of depositing thin films by sputtering, that is ejecting, material from a "target," that is source, which then deposits onto a "substrate," such as a silicon wafer...
- Physical vapor depositionPhysical vapor depositionPhysical vapor deposition is a variety of vacuum deposition and is a general term used to describe any of a variety of methods to deposit thin films by the condensation of a vaporized form of the desired film material onto various workpiece surfaces...
(PVD) - Vacuum plating
- Chemical vapor deposition
- Vitreous enamelVitreous enamelVitreous enamel, also porcelain enamel in U.S. English, is a material made by fusing powdered glass to a substrate by firing, usually between 750 and 850 °C...
Removing and reshaping
- Abrasive blastingAbrasive blastingAbrasive blasting is the operation of forcibly propelling a stream of abrasive material against a surface under high pressure to smooth a rough surface, roughen a smooth surface, shape a surface, or remove surface contaminants. A pressurized fluid, typically air, or a centrifugal wheel is used to...
- Sandblasting
- BurnishingBurnishing (metalworking)Burnishing is the plastic deformation of a surface due to sliding contact with another object. Visually, burnishing smears the texture of a rough surface and makes it shinier...
- Chemical-mechanical planarizationChemical-mechanical planarizationChemical Mechanical Polishing/Planarization is a process of smoothing surfaces with the combination of chemical and mechanical forces. It can be thought of as a hybrid of chemical etching and free abrasive polishing.-Description:...
(CMP) - ElectropolishingElectropolishingElectropolishing, also known as electrochemical polishing or electrolytic polishing , is an electrochemical process that removes material from a metallic workpiece. It is used to polish, passivate, and deburr metal parts. It is often described as the reverse of electroplating...
- Flame polishingFlame polishingFlame polishing is a method of polishing a material, usually thermoplastics or glass, by exposing it to a flame or heat. By melting the surface of the material, surface tension smooths the surface out. Operator skill is critical with this method. When done properly, flame plastic polishing produces...
- Gas cluster ion beamGas cluster ion beamGas Cluster Ion Beams is a new technology for nano-scale modification of surfaces. It can smooth a wide variety of surface material types to within an angstrom of roughness without subsurface damage. It is also used to chemically alter surfaces through infusion or deposition.-Process:Using GCIB a...
- Grinding
- Industrial etching
- Linishing
- Mass finishingMass finishingMass finishing is a group of manufacturing processes that allow large quantities of parts to be simultaneously finished. The goal of this type of finishing is to burnish, deburr, clean, radius, de-flash, descale, remove rust, polish, brighten, surface harden, prepare parts for further finishing, or...
processes- Tumble finishing
- Vibratory finishingVibratory finishingVibratory finishing is a type of mass finishing manufacturing process used to deburr, radius, descale, burnish, clean, and brighten a large number of relatively small workpieces....
- PicklingPickling (metal)Tarnision is a metal surface treatment used to remove impurities, such as stains, inorganic contaminants, rust or scale from ferrous metals, copper, and aluminum alloys. A solution called Tarnision liquor, which contains strong acids, is used to remove the surface impurities...
- PolishingPolishingPolishing is the process of creating a smooth and shiny surface by rubbing it or using a chemical action, leaving a surface with a significant specular reflection In some materials polishing is also able to reduce diffuse reflection to...
- Buffing
- PeeningPeeningPeening is the process of working a metal's surface to improve its material properties, usually by mechanical means such as hammer blows or by blasting with shot . Peening is normally a cold work process...
- Shot peeningShot peeningShot peening is a cold working process used to produce a compressive residual stress layer and modify mechanical properties of metals. It entails impacting a surface with shot with force sufficient to create plastic deformation...
- Shot peening
- SuperfinishingSuperfinishingSuperfinishing, also known as micromachining and short-stroke honing, is a metalworking process that improves surface finish and workpiece geometry. This is achieved by removing just the thin amorphous surface layer left by the last process with an abrasive stone; this layer is usually about...
- Magnetic field-assisted finishingMagnetic field-assisted finishingMagnetic field-assisted finishing, sometimes called magnetic abrasive finishing, is a surface finishing technique in which a magnetic field is used to force abrasive particles against the target surface. As such, finishing of conventionally inaccessible surfaces is possible...
Mechanical finishing
Mechanical finishing processes include:- Abrasive blasting
- Sandblasting
- Burnishing
- Grinding
- Mass finishing processes
- Tumble finishing
- Vibratory finishing
- Polishing
- Buffing
The use of abrasives in metal polishing results in what is considered a "mechanical finish".
Metal finish designations
- 3 Finish
Also known as grinding, roughing or rough grinding. These finishes are coarse in nature and usually are a preliminary finish applied before manufacturing. An example would be grinding gates off of castings, deburring or removing excess weld material. It is coarse in appearance and applied by using 36–100 grit abrasive.
When the finish is specified as #3, the material is polished to a uniform 60–80 grit.
- 4 Architectural finish
Also known as brushed, directional or satin finish. A #4 architectural finish is characterized by fine polishing grit lines that are uniform and directional in appearance. It is produced by polishing the metal with a 120–180 grit belt or wheel finish and then softened with an 80–120 grit greaseless compound or a medium non woven abrasive belt or pad.
- 4 Dairy or sanitary finish
This finish is commonly used for the medical and food industry and almost exclusively used on stainless steel. This finish is much finer than a #4 architectural finish. One takes great care to remove any surface defects in the metal, like pits, that could allow bacteria to grow. A #4 dairy or sanitary finish is produced by polishing with a 180–240 grit belt or wheel finish softened with 120–240 grit greaseless compound or a fine non woven abrasive belt or pad.
- 6 Finish
Also known as a fine satin finish. This finish is produced by polishing with a 220–280 grit belt or wheel softened with a 220–230 greaseless compound or very fine non woven abrasive belt or pad. Polishing lines will be soft and less reflective than a #4 architectural finish.
- 7 Finish
A #7 finish is produced by polishing with a 280–320 belt or wheel and sisal buffing with a cut and color compound. This is a semi-bright finish that will still have some polishing lines but they will be very dull. Carbon steel and iron are commonly polished to a #7 finish before chrome plating. A #7 finish can be made bright by color buffing with coloring compound and a cotton buff. This is commonly applied to keep polishing costs down when a part needs to be shiny but not flawless.
- 8 Finish
Also known as a mirror finish. This finish is produced by polishing with at least a 320 grit belt or wheel finish. Care will be taken in making sure all surface defects are removed. The part is sisal buffed and then color buffed to achieve a mirror finish. The quality of this finish is dependent on the quality of the metal being polished. Some alloys of steel and aluminum cannot be brought to a mirror finish. Castings that have slag or pits will also be difficult, if not impossible, to polish to a #8.
See also
- Industrial finishingIndustrial FinishingIndustrial finishing is a broad term used to describe any kind of secondary process done to any metal, plastic, or wood product used in a common market such as automotive, OEM, telecommunications or point-of-purchase....
- Surface engineeringSurface engineeringSurface engineering is the sub-discipline of materials science which deals with the surface of solid matter. It has applications to chemistry, mechanical engineering, and electrical engineering ....
- Surface scienceSurface scienceSurface science is the study of physical and chemical phenomena that occur at the interface of two phases, including solid–liquid interfaces, solid–gas interfaces, solid–vacuum interfaces, and liquid-gas interfaces. It includes the fields of surface chemistry and surface physics. Some related...
- Textile finishing