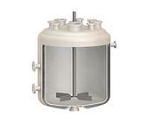
Batch reactor
Encyclopedia
The Batch reactor is the generic term for a type of vessel
widely used in the process industries. Its name is something of a misnomer
since vessels of this type are used for a variety of process operations such as solids dissolution
, product mixing
, chemical reaction
s, batch distillation
, crystallization
, liquid/liquid extraction and polymerization
. In some cases, they are not referred to as reactors
but have a name which reflects the role they perform (such as crystallizer, or bio reactor).
A typical batch reactor consists of a tank
with an agitator
and integral heating/cooling system. These vessels may vary in size from less than 1 litre to more than 15,000 litres. They are usually fabricated in steel
, stainless steel
, glass lined steel, glass
or exotic alloy
. Liquid
s and solid
s are usually charged via connections in the top cover of the reactor. Vapors and gases also discharge through connections in the top. Liquids are usually discharged out of the bottom.
The advantages of the batch reactor lie with its versatility. A single vessel can carry out a sequence of different operations without the need to break containment. This is particularly useful when processing, toxic or highly potent
compound
s.
with an overhead drive unit. Impeller
blades are mounted on the shaft. A wide variety of blade designs are used and typically the blades cover about two thirds of the diameter of the reactor. Where viscous products are handled, anchor
shaped paddles are often used which have a close clearance between the blade and the vessel walls.
Most batch reactors also use baffles. These are stationary blades which break up flow caused by the rotating agitator. These may be fixed to the vessel cover or mounted on the interior of the side walls.
Despite significant improvements in agitator blade and baffle design, mixing in large batch reactors is ultimately constrained by the amount of energy
that can be applied. On large vessels, mixing energies of more than 5 Watts per litre can put an unacceptable burden on the cooling system. High agitator loads can also create shaft stability problems. Where mixing is a critical parameter, the batch reactor is not the ideal solution. Much higher mixing rates can be achieved by using smaller flowing systems with high speed agitators, ultrasonic
mixing or static mixers
.
during processing. Even the action of stirring stored liquids generates heat. In order to hold the reactor contents at the desired temperature
, heat has to be added or removed by a cooling jacket
or cooling pipe
. Heating/cooling coils or external jackets are used for heating and cooling batch reactors. Heat transfer fluid passes through the jacket or coils to add or remove heat.
Within the chemical and pharmaceutical industries, external cooling jackets are generally preferred as they make the vessel easier to clean. The performance of these jackets can be defined by 3 parameters:
It can be argued that heat transfer coefficient is also an important parameter. It has to be recognized however that large batch reactors with external cooling jackets have severe heat transfer constraints by virtue of design. It is difficult to achieve better than 100 Watts/litre even with ideal heat transfer conditions. By contrast, continuous reactors can deliver cooling capacities in excess of 10,000 W/litre. For processes with very high heat loads, there are better solutions than batch reactors.
Fast temperature control response and uniform jacket heating and cooling is particularly important for crystallization processes or operations where the product or process is very temperature sensitive. There are several types of batch reactor cooling jackets:
The single jacket design consists of an outer jacket which surrounds the vessel. Heat transfer fluid flows around the jacket and is injected at high velocity
via nozzles. The temperature in the jacket is regulated to control heating or cooling.
The single jacket is probably the oldest design of external cooling jacket. Despite being a tried and tested solution, it has some limitations. On large vessels, it can take many minutes to adjust the temperature of the fluid in the cooling jacket. This results in sluggish temperature control. The distribution of heat transfer
fluid is also far from ideal and the heating or cooling tends to vary between the side walls and bottom dish. Another issue to consider is the inlet temperature of the heat transfer fluid which can oscillate (in response to the temperature control valve) over a wide temperature range to cause hot or cold spots at the jacket inlet points.
The half coil jacket is made by welding
a half pipe around the outside of the vessel to create a semi circular flow channel. The heat transfer fluid passes through the channel in a plug flow
fashion. A large reactor may use several coils to deliver the heat transfer fluid. Like the single jacket, the temperature in the jacket is regulated to control heating or cooling.
The plug flow characteristics of a half coil jacket permits faster displacement of the heat transfer fluid in the jacket (typically less than 60 seconds). This is desirable for good temperature control. It also provides good distribution of heat transfer fluid which avoids the problems of non uniform heating or cooling between the side walls and bottom dish. Like the single jacket design however the inlet heat transfer fluid is also vulnerable to large oscillations (in response to the temperature control valve) in temperature.
The constant flux cooling jacket is a relatively recent development. It is not a single jacket but has a series of 20 or more small jacket elements. The temperature control valve operates by opening and closing these channels as required. By varying the heat transfer area in this way, the process temperature can be regulated without altering the jacket temperature.
The constant flux jacket has very fast temperature control response (typically less than 5 seconds) due to the short length of the flow channels and high velocity of the heat transfer fluid. Like the half coil jacket the heating/cooling flux
is uniform. Because the jacket operates at substantially constant temperature however the inlet temperature oscillations seen in other jackets are absent. An unusual feature of this type jacket is that process heat can be measured very sensitively. This allows the user to monitor the rate of reaction for detecting end points, controlling addition rates, controlling crystallization
etc.
Chemical reactor
In chemical engineering, chemical reactors are vessels designed to contain chemical reactions. The design of a chemical reactor deals with multiple aspects of chemical engineering. Chemical engineers design reactors to maximize net present value for the given reaction...
widely used in the process industries. Its name is something of a misnomer
Misnomer
A misnomer is a term which suggests an interpretation that is known to be untrue. Such incorrect terms sometimes derive their names because of the form, action, or origin of the subject becoming named popularly or widely referenced—long before their true natures were known.- Sources of misnomers...
since vessels of this type are used for a variety of process operations such as solids dissolution
Dissolution (chemistry)
Dissolution is the process by which a solid, liquid or gas forms a solution in a solvent. In solids this can be explained as the breakdown of the crystal lattice into individual ions, atoms or molecules and their transport into the solvent. For liquids and gases, the molecules must be compatible...
, product mixing
Mixing (process engineering)
In industrial process engineering, mixing is a unit operation that involves manipulating a heterogeneous physical system, with the intent to make it more homogeneous...
, chemical reaction
Chemical reaction
A chemical reaction is a process that leads to the transformation of one set of chemical substances to another. Chemical reactions can be either spontaneous, requiring no input of energy, or non-spontaneous, typically following the input of some type of energy, such as heat, light or electricity...
s, batch distillation
Batch distillation
Batch distillation refers to the use of distillation in batches, meaning that a mixture is distilled to separate it into its component fractions before the distillation still is again charged with more mixture and the process is repeated...
, crystallization
Crystallization
Crystallization is the process of formation of solid crystals precipitating from a solution, melt or more rarely deposited directly from a gas. Crystallization is also a chemical solid–liquid separation technique, in which mass transfer of a solute from the liquid solution to a pure solid...
, liquid/liquid extraction and polymerization
Polymerization
In polymer chemistry, polymerization is a process of reacting monomer molecules together in a chemical reaction to form three-dimensional networks or polymer chains...
. In some cases, they are not referred to as reactors
Chemical reactor
In chemical engineering, chemical reactors are vessels designed to contain chemical reactions. The design of a chemical reactor deals with multiple aspects of chemical engineering. Chemical engineers design reactors to maximize net present value for the given reaction...
but have a name which reflects the role they perform (such as crystallizer, or bio reactor).
A typical batch reactor consists of a tank
Tank
A tank is a tracked, armoured fighting vehicle designed for front-line combat which combines operational mobility, tactical offensive, and defensive capabilities...
with an agitator
Agitator (device)
An agitator is a device or mechanism to put something into motion by shaking or stirring.-Manual agitator:* Manual dishwashers* A rock can be a device used to agitate dirt and other solids from fabric in washing* A stirring rod...
and integral heating/cooling system. These vessels may vary in size from less than 1 litre to more than 15,000 litres. They are usually fabricated in steel
Steel
Steel is an alloy that consists mostly of iron and has a carbon content between 0.2% and 2.1% by weight, depending on the grade. Carbon is the most common alloying material for iron, but various other alloying elements are used, such as manganese, chromium, vanadium, and tungsten...
, stainless steel
Stainless steel
In metallurgy, stainless steel, also known as inox steel or inox from French "inoxydable", is defined as a steel alloy with a minimum of 10.5 or 11% chromium content by mass....
, glass lined steel, glass
Glass
Glass is an amorphous solid material. Glasses are typically brittle and optically transparent.The most familiar type of glass, used for centuries in windows and drinking vessels, is soda-lime glass, composed of about 75% silica plus Na2O, CaO, and several minor additives...
or exotic alloy
Alloy
An alloy is a mixture or metallic solid solution composed of two or more elements. Complete solid solution alloys give single solid phase microstructure, while partial solutions give two or more phases that may or may not be homogeneous in distribution, depending on thermal history...
. Liquid
Liquid
Liquid is one of the three classical states of matter . Like a gas, a liquid is able to flow and take the shape of a container. Some liquids resist compression, while others can be compressed. Unlike a gas, a liquid does not disperse to fill every space of a container, and maintains a fairly...
s and solid
Solid
Solid is one of the three classical states of matter . It is characterized by structural rigidity and resistance to changes of shape or volume. Unlike a liquid, a solid object does not flow to take on the shape of its container, nor does it expand to fill the entire volume available to it like a...
s are usually charged via connections in the top cover of the reactor. Vapors and gases also discharge through connections in the top. Liquids are usually discharged out of the bottom.
The advantages of the batch reactor lie with its versatility. A single vessel can carry out a sequence of different operations without the need to break containment. This is particularly useful when processing, toxic or highly potent
Potent
Potent may refer to:*Vair#Potent for the heraldic fur*Warren Potent for the Australian Olympic medalist in shootingSee also:*Potency...
compound
Chemical compound
A chemical compound is a pure chemical substance consisting of two or more different chemical elements that can be separated into simpler substances by chemical reactions. Chemical compounds have a unique and defined chemical structure; they consist of a fixed ratio of atoms that are held together...
s.
Agitation
The usual agitator arrangement is a centrally mounted driveshaftDriveshaft
A drive shaft, driveshaft, driving shaft, propeller shaft, or Cardan shaft is a mechanical component for transmitting torque and rotation, usually used to connect other components of a drive train that cannot be connected directly because of distance or the need to allow for relative movement...
with an overhead drive unit. Impeller
Impeller
An impeller is a rotor inside a tube or conduit used to increase the pressure and flow of a fluid.- Impellers in pumps :...
blades are mounted on the shaft. A wide variety of blade designs are used and typically the blades cover about two thirds of the diameter of the reactor. Where viscous products are handled, anchor
Anchor
An anchor is a device, normally made of metal, that is used to connect a vessel to the bed of a body of water to prevent the vessel from drifting due to wind or current. The word derives from Latin ancora, which itself comes from the Greek ἄγκυρα .Anchors can either be temporary or permanent...
shaped paddles are often used which have a close clearance between the blade and the vessel walls.
Most batch reactors also use baffles. These are stationary blades which break up flow caused by the rotating agitator. These may be fixed to the vessel cover or mounted on the interior of the side walls.
Despite significant improvements in agitator blade and baffle design, mixing in large batch reactors is ultimately constrained by the amount of energy
Energy
In physics, energy is an indirectly observed quantity. It is often understood as the ability a physical system has to do work on other physical systems...
that can be applied. On large vessels, mixing energies of more than 5 Watts per litre can put an unacceptable burden on the cooling system. High agitator loads can also create shaft stability problems. Where mixing is a critical parameter, the batch reactor is not the ideal solution. Much higher mixing rates can be achieved by using smaller flowing systems with high speed agitators, ultrasonic
Ultrasound
Ultrasound is cyclic sound pressure with a frequency greater than the upper limit of human hearing. Ultrasound is thus not separated from "normal" sound based on differences in physical properties, only the fact that humans cannot hear it. Although this limit varies from person to person, it is...
mixing or static mixers
Static mixer
A static mixer is a device for mixing two fluid materials. Most commonly, the fluids are liquid; however, static mixers are used to mix gas streams, disperse gas into liquid or disperse immiscible liquids. The device consists of mixer elements contained in a cylindrical or squared housing. These...
.
Heating and cooling systems
Products within batch reactors usually liberate or absorb heatHeat
In physics and thermodynamics, heat is energy transferred from one body, region, or thermodynamic system to another due to thermal contact or thermal radiation when the systems are at different temperatures. It is often described as one of the fundamental processes of energy transfer between...
during processing. Even the action of stirring stored liquids generates heat. In order to hold the reactor contents at the desired temperature
Temperature
Temperature is a physical property of matter that quantitatively expresses the common notions of hot and cold. Objects of low temperature are cold, while various degrees of higher temperatures are referred to as warm or hot...
, heat has to be added or removed by a cooling jacket
Heat exchanger
A heat exchanger is a piece of equipment built for efficient heat transfer from one medium to another. The media may be separated by a solid wall, so that they never mix, or they may be in direct contact...
or cooling pipe
Heat pipe
A heat pipe or heat pin is a heat-transfer device that combines the principles of both thermal conductivity and phase transition to efficiently manage the transfer of heat between two solid interfaces....
. Heating/cooling coils or external jackets are used for heating and cooling batch reactors. Heat transfer fluid passes through the jacket or coils to add or remove heat.
Within the chemical and pharmaceutical industries, external cooling jackets are generally preferred as they make the vessel easier to clean. The performance of these jackets can be defined by 3 parameters:
- Response time to modify the jacket temperature
- UniformityUniformityUniformity may refer to:* Distribution uniformity, a measure of how uniformly water is applied to the area being watered* Religious uniformity, the promotion of one state religion, denomination, or philosophy to the exclusion of all other religious beliefs...
of jacket temperature - Stability of jacket temperature
It can be argued that heat transfer coefficient is also an important parameter. It has to be recognized however that large batch reactors with external cooling jackets have severe heat transfer constraints by virtue of design. It is difficult to achieve better than 100 Watts/litre even with ideal heat transfer conditions. By contrast, continuous reactors can deliver cooling capacities in excess of 10,000 W/litre. For processes with very high heat loads, there are better solutions than batch reactors.
Fast temperature control response and uniform jacket heating and cooling is particularly important for crystallization processes or operations where the product or process is very temperature sensitive. There are several types of batch reactor cooling jackets:
Single external jacket
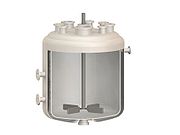
Velocity
In physics, velocity is speed in a given direction. Speed describes only how fast an object is moving, whereas velocity gives both the speed and direction of the object's motion. To have a constant velocity, an object must have a constant speed and motion in a constant direction. Constant ...
via nozzles. The temperature in the jacket is regulated to control heating or cooling.
The single jacket is probably the oldest design of external cooling jacket. Despite being a tried and tested solution, it has some limitations. On large vessels, it can take many minutes to adjust the temperature of the fluid in the cooling jacket. This results in sluggish temperature control. The distribution of heat transfer
Heat transfer
Heat transfer is a discipline of thermal engineering that concerns the exchange of thermal energy from one physical system to another. Heat transfer is classified into various mechanisms, such as heat conduction, convection, thermal radiation, and phase-change transfer...
fluid is also far from ideal and the heating or cooling tends to vary between the side walls and bottom dish. Another issue to consider is the inlet temperature of the heat transfer fluid which can oscillate (in response to the temperature control valve) over a wide temperature range to cause hot or cold spots at the jacket inlet points.
Half coil jacket
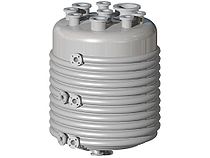
Welding
Welding is a fabrication or sculptural process that joins materials, usually metals or thermoplastics, by causing coalescence. This is often done by melting the workpieces and adding a filler material to form a pool of molten material that cools to become a strong joint, with pressure sometimes...
a half pipe around the outside of the vessel to create a semi circular flow channel. The heat transfer fluid passes through the channel in a plug flow
Plug flow
In fluid mechanics, plug flow is a simple model of the velocity profile of a fluid flowing in a pipe. In plug flow, the velocity of the fluid is assumed to be constant across any cross-section of the pipe perpendicular to the axis of the pipe...
fashion. A large reactor may use several coils to deliver the heat transfer fluid. Like the single jacket, the temperature in the jacket is regulated to control heating or cooling.
The plug flow characteristics of a half coil jacket permits faster displacement of the heat transfer fluid in the jacket (typically less than 60 seconds). This is desirable for good temperature control. It also provides good distribution of heat transfer fluid which avoids the problems of non uniform heating or cooling between the side walls and bottom dish. Like the single jacket design however the inlet heat transfer fluid is also vulnerable to large oscillations (in response to the temperature control valve) in temperature.
Constant flux cooling jacket
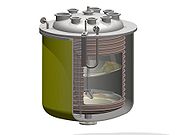
The constant flux jacket has very fast temperature control response (typically less than 5 seconds) due to the short length of the flow channels and high velocity of the heat transfer fluid. Like the half coil jacket the heating/cooling flux
Flux
In the various subfields of physics, there exist two common usages of the term flux, both with rigorous mathematical frameworks.* In the study of transport phenomena , flux is defined as flow per unit area, where flow is the movement of some quantity per time...
is uniform. Because the jacket operates at substantially constant temperature however the inlet temperature oscillations seen in other jackets are absent. An unusual feature of this type jacket is that process heat can be measured very sensitively. This allows the user to monitor the rate of reaction for detecting end points, controlling addition rates, controlling crystallization
Crystallization
Crystallization is the process of formation of solid crystals precipitating from a solution, melt or more rarely deposited directly from a gas. Crystallization is also a chemical solid–liquid separation technique, in which mass transfer of a solute from the liquid solution to a pure solid...
etc.